@droftarts thanks for taking the time to look at this. The remaining cfg pins are to set motor current. Its labeled on the back of the board but not in any documentation. I believe I have the other jumpers set correctly including Standalone mode. Tonight, I'll sketch up a simple schematic to show how the step stick adapter is labeled along with the voltages and a pic of the back. Probably too confusing to explain further without a visual representation.
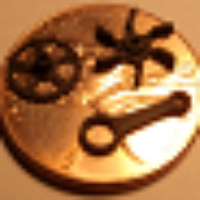
Posts made by 3DPMicro
-
RE: Duet Ethernet and BTT TMC5160T pro
-
Duet Ethernet and BTT TMC5160T pro
Sorry in advance for the long post.
Before I invest in 6HC I wanted to see if the 5160's at 48v would provide the speeds I desire for non print moves. Im using my single axis test rig for this experiment. I already have several Duet Ethernets so I purchased the BTT drive as seen in this Amazon ad https://a.co/d/dh1Ueat with the intent of running it in "stand alone" mode. The wiring seems straightforward but I've yet to make it work. I have the motor supply connected to a 48v psu and the Duet on a 24v psu. Of course step, dir, en, grd, and 3.3v are connected to the Duets expansion header but it seems like the drive also requires 24v. The 7th slide in the ad shows "ordinary drive connector" pinout that I'm connecting to. If I connect 24v to that connector like it's marked, the 24v, 48v and logic will share a common ground. Does this seem safe? I don't want to kill the Duet. There's no literature that mentions specific wiring in Standalone mode. I did notice on the step stick adapter the 24v pin is marked Vm (for gate?) leading me to believe 24v is required for the circuitry to work but thats an ignorant guess. -
D3 magnetic encoder/1hcl max rpm
What would be the maximum motor rpm and are there factors that contribute to it?
Thanks -
RE: Very slight systematic waves every about 2mm on the prints
@luc since the 2mm spacing suggests its related to tooth pitch flip the belt so the teeth aren't engaged, tension to provide enough grip to execute a test print.
-
Removing axis in console
My 2 axis CNC lathe is finally approaching completion. Since I only need x and z can I remove the y axis from the console. If so, how?
Thanks -
Signal input help
I'm using a VESC to control the BLDC spindle motor on my Duet Ethernet (FW=3.4) mill. Having recently configured a different spindle for the same mill using PWM I would like to set this one up to act like the other, i.e control through "spindle" in DWC and use M3 .... in my gcode program. Unfortunatly the VESC doesn't support PWM input. PPM, ADC (duty cycle), NRF (whatever that is) and UART are the options. Is there a path forward to making this happen? Thanks
-
RE: Measuring PWM output and duty cycle
@o_lampe I haven't tried it yet but if I put 5 Volts to the pwm lead to the spindle that should essentially be 100% duty or is the pwm from Duet pulsing the ground?
I tried much higher frequencies but it didn't have any effect. Im waiting to hear what the spindle manufacturer has to say
Can you give me an example of the converter you mentioned? Is it an A/D converter? -
RE: Measuring PWM output and duty cycle
I have my spindle working but it's not reaching the 10k rpm as advertised. I have tried 100-2000 for the frequency with no noticeable effect. Im consistently seeing a range of approximately 50% duty cycle at about 4500rpm to a maximum of 90-93% at 7450rpm (ballpark numbers). The oscope is bouncing around when in the 90+% range so im not sure if it's not seeing 100% duty cycle or if the Duet isn't actually producing it. 100% duty cycle should show as flat lined on the oscope or possibley a consistant waveform? It looks pretty rough.
Basically I'm trying to determine if the Duet is producing the highest possible duty cycle or the spindle is not capable of the advertised 10k rpm. Any input would be appreciated -
RE: Measuring PWM output and duty cycle
@deckingman thank you. Ignorance is painful. I screwed with this thing for hours and it was simple as that
-
Measuring PWM output and duty cycle
I'm trying to configure a PWM controlled spindle but not having any luck. I guess the simplest question would be - shouldnt I be able to see the PWM signal with my oscope by connecting the probe to ground and the chosen pwm pin? Spindle becomes "active" after sending m3 command but flat lined on the scope
p.s.
having an oscope should not be construed as knowing what the hell I'm doing haha
my config, incase there's something obviously wrongBoard: Duet 2 Ethernet (2Ethernet) Firmware: RepRapFirmware for Duet 2 WiFi/Ethernet 3.4.2 (2022-09-13) Duet Web Control 3.4.2 ; Configuration file for Duet Ethernet (firmware version 1.20 or newer) ; executed by the firmware on start-up ; ; generated by RepRapFirmware Configuration Tool on Thu May 10 2018 21:56:20 GMT-0400 (Eastern Daylight Time) ; General preferences M453 ; Put the machine into CNC Modes G90 ; Send absolute coordinates... ;M83 ...but relative extruder moves ; Network M550 Micro Mill 1 ; Set machine name M552 P192.168.1.69 S1 ; Enable network and set IP address M553 P255.255.255.0 ; Set netmask M554 P192.168.1.254 ; Set gateway M586 P0 S1 ; Enable HTTP M586 P1 S0 ; Disable FTP M586 P2 S0 ; Disable Telnet ; Drive mapping M584 X0 Y1 Z2 A3 ; Drives M569 P0 S0 ; Drive 0 goes forwards M569 P1 S0 ; Drive 1 goes FORWARD M569 P2 S1 ; Drive 2 goes forwards M569 P3 S1 ; Drive 3 goes forwards M350 X8 Y8 Z8 A16 I1 ; Configure microstepping M92 X1600 Y1600 Z1600 ;Set steps per mm M92 A17.778 ;Set steps per degree M566 X17 Y17 Z17 A17 ; Set maximum instantaneous speed changes (mm/min) M203 X1000 Y1000 Z800 A1000 ; Set maximum speeds (mm/min) 800 = 31.5 in/min 100=3.937 10 mm/sec = 23.622 in/min M201 X600 Y600 Z600 A600 ; Set accelerations (mm/s^2) M906 X800 Y800 Z1600 A1300 I50 ; Set motor currents (mA) and motor idle factor in per cent M84 S120 ; Set idle timeout ; Axis Limits M208 X-90 Y-41.5 Z-90 A0 S1 ; w/ end stop y=40 Set axis minima M208 X90 Y40 Z90 A360 S0 ; Set axis maxima ; Endstops ; OLD RRF2 M574 X2 Y2 Z2 A0 S0 ; Set active low endstops, endstops high ;NEW RRF3 M574 X2 S1 P"!xstop" M574 Y2 S1 P"!ystop" M574 Z2 S1 P"!zstop" ; Z-Probe ;M558 P0 H5 F120 T6000 Disable Z probe but set dive height, probe speed and travel speed ;M557 X15:215 Y15:195 S20 Define mesh grid ; Heaters ;M140 H-1 Disable heated bed ; Fans ;M106 P0 S0.3 I0 F500 H-1 ; Set fan 0 value, PWM signal inversion and frequency. Thermostatic control is turned off ;M106 P1 S1 I0 F500 H T45 ; Set fan 1 value, PWM signal inversion and frequency. Thermostatic control is turned on ;M106 P2 S1 I0 F500 H T45 ; Set fan 2 value, PWM signal inversion and frequency. Thermostatic control is turned on ; Tools ;SPINDLE M950 R0 C"exp.heater3" Q250 M563 P0 R0 M42 P0 S0.5 ;also tried ; Tools ;SPINDLE ;M950 R0 C"exp.heater3" Q1000 ;M563 P0 R0 S"Spindle" ;M568 P0 F0 ; Automatic saving after power loss is not enabled ; Custom settings M501 ; Load Stored Parameters
-
RE: Duet3 D for CNC
@discoverycharles Grbl is a gcode interpreter. Duet has that integrated in. You send your gcode program to the Duet and control the machine directly from the Duet Web Control UI. Its not quite as refined as Chilipeppr, etc but its all in one package. If you check out Workbee CNC, it runs the Duet and can give you an idea of what to expect. One of the features I've come to appreciate is the ability to almost instantaneously tweak the FW. No compiling/uploading. As with anything new theres gonna be a learning curve, though
-
RE: Duet controlled micro mill
I can see it being a real hard guess
The dies to form the springs were finish machined on the mill with a .5mm ball endmill, too.
https://youtu.be/27zb8gcqGPA?si=suV_zfw9h41iTjDT
I posted this above already but this is what the part was for https://youtu.be/27_E8RawCyQ?si=GDXWU7Ujmx36qK8a -
RE: Duet controlled micro mill
@Phaedrux Its a retractable ID badge holder that goes on your belt with places to attach a zip drive and random number generator dongle. Grade 5 Titanium, Delrin and spring steel
Made on a wire EDM, Duet 2 controlled Lathe and my Duet 2 controlled micro mill -
RE: Duet controlled micro mill
 !
-
RE: Steel bed
Probably. Anything from 1050 on up if you can get it heat treated. 301 stainless would be a great choice because of its corrosion resistance but it's higher CTE may not be so great. It may not like the temperature and warp. Either way you probably cant go wrong with 1095
-
RE: Duet controlled micro mill
@JoergS5 thanks for the explanation and feedback. I wont concern myself with it but will monitor it for the sake of better understanding what might effect it
-
RE: Duet controlled micro mill
The Duet 2, with regularily updated FW has been flawless through many projects over the last few years guiding this little mill. I have the same confidence in it as any of the professional grade machines I run at work.
I thought if it could be tripped up the g code for 3d maching the .5mm radii on this part would do it. Resolving moves as small as 100nm for the inside corners there was no indication of lost steps or rounding errors (the floating point goes that low?) over the 8 parts that were made. Pretty cool
https://youtu.be/27_E8RawCyQ
There were 0 hiccups and 0 errors but underruns showed 0,0,4. What does that mean?