@fcwilt Thank you. Sounds well thought out!
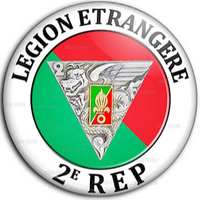
Posts made by Rudy2A
-
RE: Pulley VS belts
@fcwilt said in Pulley VS belts:
Salut,
Je suppose que vous parlez d'une vidéo? Je peux certainement en inventer une rapide si vous le souhaitez.
J'ai inclus un capteur de butée sur chaque axe Z qui gère le lit s'il est grossièrement hors de niveau.
Ensuite, la fonction de mise à niveau automatique termine le travail.
FrédéricIndeed I would like to see the result on video, but I don't want to disturb you! Did you create your printer by taking a model or plan from the internet or did you create it according to your own plans and ideas?
-
RE: Pulley VS belts
@fcwilt said in Pulley VS belts:
Très heureux avec les resultats.
Hi Frédéric, This is exactly what I want to do ... I want to put three independent belts each with their own motor (in a triangle position on the bed frame) with the automatic leveling ... Do you have a demonstration of your printer? Thank you
-
RE: Pulley VS belts
@mrehorstdmd said in Pulley VS belts:
Mon imprimante utilise des courroies pour soulever l'axe Z et un réducteur à vis sans fin sur le moteur qui empêche le mouvement du lit lorsque l'alimentation du moteur de l'axe Z est coupée. Ça marche bien.
Do you have an example of your reducer ?
Thank's
-
Pulley VS belts
Good morning all.
Straps instead of lead screws for guiding the bed (Z) on a CoreXY?
I am thinking about modifying the displacement of my bed on a CoreXY. My idea is to replace the lead screws with a belt system ... The advantage in my opinion is that this system is less strict in alignment and therefore has less friction. However, the flaw is that you may need a pulley system to increase the force and find a solution so that the plate does not come down when the machine is off. Who uses belts on this type of installation?
Thank you
-
RE: Capacitive Sensor
@ziggymanpopo Late response due to my work ... Thank you for sharing, I admit that your technique has already turned in my head!
-
What do you use as a slicer?
Good morning all,
I'm using your time to do a little survey ...
What do you use as a slicer?
Personally, I used Simplify3D quite a while, I was almost happy.
Cura, I've always complicated it a lot so I can't assess how it looks.
And there, I have been working with PrusaSlicer for 6 months and find it perfect.
Thank you
-
M558 Axxx ?
Hello, try to have three sounding point polls.
I put this command : M558 P1 C"zprobe.in" H5 F120 A03 T10000 S0.03 , but I only get two polls at most each time. Thank's -
RE: Purge and prime nozzle
@Phaedrux said in Purge and prime nozzle:
Le résultat final est une petite languette de filament qui est facile à retirer du lit et laisse la buse très propre avant le début de l'impression.
I have modified some values to adapt them to my configuration, and it works very well ... Thank you
-
RE: Capacitive Sensor
I definitely left the capacitive probe to the detriment of the mini IR probe.
The reason is that for me the weight of the capacitive probe was a bit too heavy. She was exerting a difference on my bed when polling.
FYI, my bed is not absolutely stable and the slightest difference in weight causes a difference in the measurement in the height map.
I will be working on another much more stable bed system soon, so I will test again.
-
RE: Purge and prime nozzle
@Phaedrux said in Purge and prime nozzle:
Je l'utilise pour une buse d'amorçage et cela fonctionne assez bien.
Perfect, I'll look into it as soon as I have some time ... Thank you
-
Purge and prime nozzle
I'm desperately looking for a way to start all my prints with a light purge and prime my nozzle.
I would like the front right of my bed to a place where the impression is not possible (I know my X&Y) that my nozzle purges a small amount of material then a light rubbing over a small distance to clean .
To be included in the slicer startup G-Code or as a file? Do you have an idea, or are you using something extra? Thank you
-
RE: Capacitive Sensor
@Veti said in Capacitive Sensor:
Y252 ne peut pas être atteint avec un décalage de -43
changez ceci en
M557 X11: 250 Y11: 220 S20; définir la grille de maillagethank you,
Indeed, with that it works ...
On the other hand, depending on the tests carried out, the capacitive or IR probe is similar. I would tell you that my finding to come.
-
RE: Capacitive Sensor
This configuration works perfectly with the IR probe.
S2 probes the 4 corners (2X2).
If you put S4, it will probe 4 points on the first line multiplied by 4, so 16 points on the bed.
This is valid for S3, S6 ...
-
RE: Capacitive Sensor
I have known this for a little while and thanks to this forum that there is a difference between G32 and G29. It was just a tip in case ...
; bed.g
G28 ; Home all Axes
M561 ; Efface la correction de plan
M290 R0 S0 ; Efface Baby-stepping; Bed levelling (G32)
G30 P0 X0.0 Y132 Z-99999; sonde près d'une vis sans fin, à mi-chemin le long de l'axe Y
G30 P1 X260 Y132 Z-99999 S2; sonde près d'une vis et calibrez 2 moteurs -
RE: Capacitive Sensor
Exactly, I thought about taking the offset of my probe ... the G32 work good.
; Configuration file for Duet WiFi (firmware version 3)
; executed by the firmware on start-up
;
; generated by RepRapFirmware Configuration Tool v3.1.4 on Mon Oct 26 2020 11:25:15 GMT+0100 (CET); General preferences
G90 ; send absolute coordinates...
M83 ; ...but relative extruder moves
M550 P"My Printer+" ; set printer name
M669 K1 ; select CoreXY mode; Network
M552 S1 ; enable network
M586 P0 S1 ; enable HTTP
M586 P1 S0 ; disable FTP
M586 P2 S0 ; disable Telnet; Drives
M569 P0 S0 ; physical drive 0 goes forwards
M569 P1 S0 ; physical drive 1 goes forwards
M569 P2 S0 ; physical drive 2 goes forwards
M569 P3 S0 ; physical drive 3 goes forwards
M569 P4 S0M584 X0 Y1 Z2:4 E3 ; set drive mapping
M671 X-58:317 Y132:132 S10 ; vis à plomb à gauche (connectées à Z) et à droite (connectées à E1) de repère XM350 X16 Y16 Z16 E16 I1 ; configure microstepping with interpolation
M92 X80.00 Y80.00 Z1600.00 E830.00 ; set steps per mm
M566 X600.00 Y600.00 Z60.00 E2400.00 ; set maximum instantaneous speed changes (mm/min)
M203 X11639 Y11639 Z200 E600 ; set maximum speeds (mm/min)
M201 X800.00 Y800.00 Z40.00 E300.00 ; set accelerations (mm/s^2)
M906 X950 Y950 Z950 E1120 I20 ; set motor currents (mA) and motor idle factor in per cent
M84 S30 ; Set idle timeout; Axis Limits
M208 X0 Y0 Z-0.5 S1 ; set axis minima
M208 X270 Y270 Z245 S0 ; set axis maxima; Endstops
M574 X1 S1 P"xstop" ; configure active-high endstop for high end on X via pin xstop
M574 Y1 S1 P"ystop" ; configure active-high endstop for high end on Y via pin ystop
;M574 Z1 S2 P"io2.in" ; Axe Z avec deux moteurs, butées min.; Z-Probe
M558 P5 C"zprobe.in" H5 F120 T6000 ; set Z probe type to unmodulated and the dive height + speeds
G31 P500 X0 Y-43 Z1.30 ; set Z probe trigger value, offset and trigger height
M557 X11:250 Y11:252 S20 ; define mesh grid; Heaters
M308 S0 P"bedtemp" Y"thermistor" T100000 B4725 C7.06e-8 ; configure sensor 0 as thermistor on pin bedtemp
M950 H0 C"bedheat" T0 ; create bed heater output on bedheat and map it to sensor 0
M307 H0 A435.0 C388.3 D7.8 B0 S0.8 V13.4
;M307 H0 B0 S1.00 ; disable bang-bang mode for the bed heater and set PWM limit
M140 H0 ; map heated bed to heater 0
M143 H0 S120 ; set temperature limit for heater 0 to 120C
M308 S1 P"e0temp" Y"thermistor" T100000 B4725 C7.06e-8 ; configure sensor 1 as thermistor on pin e0temp
M950 H1 C"e0heat" T1 ; create nozzle heater output on e0heat and map it to sensor 1
M307 H1 A650.7 C221.3 D4.8 B0 S1 V13.3
;M307 H1 B0 S1.00 ; disable bang-bang mode for heater and set PWM limit; Fans
M950 F0 C"fan0" Q500 ; create fan 0 on pin fan0 and set its frequency
M106 P0 S0 H-1 ; set fan 0 value. Thermostatic control is turned off
M950 F1 C"fan1" Q500 ; create fan 1 on pin fan1 and set its frequency
M106 P1 S1 H1 T45 ; set fan 1 value. Thermostatic control is turned on; Tools
M563 P0 D0 H1 F0 ; define tool 0
G10 P0 X0 Y0 Z0 ; set tool 0 axis offsets
G10 P0 R0 S0 ; set initial tool 0 active and standby temperatures to 0C; Custom settings are not defined
-
RE: Capacitive Sensor
Return to the installation.
The wiring is very simple and the adjustment of the probe in Config.g too.Where it goes wrong is with the mesh of the bed ... impossible to have a complete mesh. The nozzle only probes the 2 ends of the front of the deck and stops ... yet normally it should probe all 4 corners as configured.
Tired of searching, I will put back my mini IR probe which for me is not exceptional either (I expected to be frank to be more precise).