I got a question about my Voron V0.1 and the 1LC toolboard. There's really no room so I made this ugly looking thing which is a modified Bondtech Olof Ogland Cowling and mount. The only place I could place it was in front of the LGX Lite extruder. So here it is the 2001: A Space Odyssey monolith's ugly brother
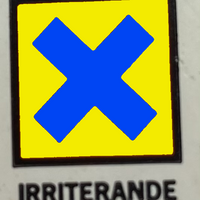
Best posts made by Gixxerfast
-
Voron V0.1 1LC Toolboard mount
-
Canned ERCF board v1.0-beta2
So, the latest beta version of the Canned ERCF expansion board is back from JLCPCB and is ready. It seems to work fine though I'm in the middle of building the actual ERCF
It will require some more testing to be sure that there are no major flaws left.
The main differences to the first version is:
- Added a 4.7Kohms pullup resistor on the TX/RX UART line to keep the line high when Duet firmware momentarily disables UART when reading and transmitting. This can be handled with software changes but that will make maintenance harder as there will be more code to keep up to date.
- Added a 480 ohms series resistor on the io0.out PWM pin (to the servo)
- Added over voltage protection (up to 30V) to the io1.in, io2.in and io3.in inputs
- Added VIN voltage monitoring.
- Added separate CAN connectors to make it easier to hook it in the middle between the board and for example a toolboard.
I have made a fork of the Duet3Expansion firmware here which with the changes above only required changes to the SammyC21.h configuration file.
There is some history regarding this board in this thread.
-
RE: Schrodinger's Parameters
@theolodian Use a small i instead of the capital I in if
-
RE: Self calibrating Z offset implementation
@joeprint Do you mean like the Auto Z calibration ( https://github.com/protoloft/klipper_z_calibration )?
EDIT: Didn't see the link first.
Yes, I have a version of it. Take a look here: https://github.com/gixxerfast/rrf-voron2/tree/master/macros/autoz
It takes some adapting to get it to work so it's not quite plug and play. And there might be better ways of doing it ...
-
RE: BL Touch not working
Which version of RRF are you using, ver 2? I can't see that you've mentioned it.
EDIT: OK, so you're using RRF 3.3
Then I think you should config the BLTouch differently:
Have you read this bit, "Software setup (RepRapFirmware 3)" for the https://duet3d.dozuki.com/Wiki/Connecting_a_Z_probe
Either I'm a sloppy reader or I can't see that you have the M950
AS in this example:
2. Create a GPIO/Servo pin index using your chosen control pin, for example:M950 S0 C"io7.out" ; Duet 3 MB6HC
M950 S0 C"io3.out" ; Duet 3 Mini 5+
M950 S0 C"exp.heater3" ; Duet 2 WiFi/Ethernet
M950 S0 C"duex.pwm1" ; Duet 2 WiFi/Ethernet + DueX2/5
M950 S0 C"!exp.heater6" ; Duet 2 WiFi/Ethernet + BoB
M950 S0 C"zprobe.mod" ; Duet 2 Maestro -
Sammy C21 support for 2 TMC2209 drivers with UART com
Hi,
I'm tinkering with a little project where I'm using the Sammy C21 and I want to enable support for two TMC2209 drivers with serial communication/configuration.It was fairly straightforward to modify the Sammy C21 firmware so that I can have two drivers with step/dir control. However when I want to enable UART/sercom things get a bit more complicated.
Part of it is probably because I don't know what I'm doing
These are the defines I'm using at the moment
#define BOARD_TYPE_NAME "SAMMYC21" #define BOOTLOADER_NAME "SAMMYC21" // General features #define HAS_VREF_MONITOR 0 // Nope no VREF-monitor #define HAS_VOLTAGE_MONITOR 0 // Nope, this wil break the build! #define HAS_12V_MONITOR 0 #define HAS_CPU_TEMP_SENSOR 1 #define HAS_ADDRESS_SWITCHES 0 // What is this? #define HAS_BUTTONS 0 // Nope // Drivers configuration #define SUPPORT_DRIVERS 1 #define HAS_SMART_DRIVERS 1 #define HAS_STALL_DETECT 0 #define SINGLE_DRIVER 0 // UE #define SUPPORT_SLOW_DRIVERS 0 // UE #define SUPPORT_DELTA_MOVEMENT 0 #define USE_EVEN_STEPS 0 // UE //------------------------------------------------------------------ #define ACTIVE_HIGH_STEP 1 // 1 = active high, 0 = active low #define ACTIVE_HIGH_DIR 0 // 1 = active high, 0 = active low #define SUPPORT_TMC51xx 0 #define SUPPORT_TMC2160 0 #define SUPPORT_TMC2660 0 #define SUPPORT_TMC22xx 1 constexpr size_t NumDrivers = 2; constexpr size_t NumSmartDrivers = NumDrivers; constexpr size_t MaxSmartDrivers = NumDrivers; #define TMC22xx_USES_SERCOM 1 // UE #define TMC22xx_HAS_MUX 1 // I don't have a MUX but if I set this everything gets easier it seems #define TMC22xx_SINGLE_DRIVER 0 // UE #define TMC22xx_HAS_ENABLE_PINS 0 // <- Am I supposed to set this ? #define TMC22xx_VARIABLE_NUM_DRIVERS 0 // No, it's fixed to two #define TMC22xx_USE_SLAVEADDR 1 // What does this mean ? #define TMC22xx_DEFAULT_STEALTHCHOP 0 // No thanks constexpr Pin GlobalTmc22xxEnablePin = PortAPin(9); constexpr uint8_t TMC22xxSercomNumber = 4; Sercom * const SERCOM_TMC22xx = SERCOM4; //Sercom * TMC22xxSercoms[NumDrivers] = {SERCOM3, SERCOM3}; constexpr Pin TMC22xxSercomTxPin = PortAPin(22); constexpr GpioPinFunction TMC22xxSercomTxPinPeriphMode = GpioPinFunction::C; constexpr Pin TMC22xxSercomRxPin = PortAPin(20); constexpr GpioPinFunction TMC22xxSercomRxPinPeriphMode = GpioPinFunction::D; constexpr uint8_t TMC22xxSercomRxPad = 2;
Does the defines above look right for a simple TMC2209 board?
I now have a few build errors left
../src/Platform.cpp: In function 'void Platform::Spin()': ../src/Platform.cpp:983:21: error: 'powered' was not declared in this scope 983 | SmartDrivers::Spin(powered); | ^~~~~~~ ../src/Platform.cpp: In function 'void Platform::SetOrResetEventOnStall(DriversBitmap, bool)': ../src/Platform.cpp:1814:3: error: 'eventOnStallDrivers' was not declared in this scope 1814 | eventOnStallDrivers |= drivers; | ^~~~~~~~~~~~~~~~~~~ ../src/Platform.cpp:1818:3: error: 'eventOnStallDrivers' was not declared in this scope 1818 | eventOnStallDrivers &= ~drivers; | ^~~~~~~~~~~~~~~~~~~ src/subdir.mk:24: recipe for target 'src/Platform.o' failed
The first is because I don't have a voltage monitoring so the variable is never defined.
The second is about the same but for stallguard.As you can see I'm testing my way forward
I know that you guys have probably a lot of more urgent things to handle but I would appreciate a nudge in the right direction if possible.
-
RE: Comparing klipper and RRF input shaper data collection
@gloomyandy
So. I assume this is the current standalone version of Andys script (with spaces instead of tabs) Thanks again!
var title = "Klipper style vibration test V0.3" var axis="Y" var datarate=1320 var stime = state.upTime var min_freq = 5.0 var max_freq = 10000/75 var accel_per_hz = 75 var hz_per_sec = 1 var freq = var.min_freq var max_accel = var.max_freq * var.accel_per_hz var X = 150.0 var Y = 150.0 var sign = 1.0 var t_seg = 0 var accel = 0 var max_v = 0 var L = 0 var nX = 0 var old_freq = 0 var filename = "/gcodes/vtest_" ^ var.axis ^ ".gcode" echo "max_accel " ^ var.max_accel ^ " min freq " ^ var.min_freq ^ " max freq " ^ var.max_freq echo >{var.filename} " " echo >>{var.filename} "M201 X" ^ var.max_accel ^ " Y" ^ var.max_accel echo >>{var.filename} "M205 X0 Y0" echo >>{var.filename} "G91" echo >>{var.filename} "M400" echo >>{var.filename} "G4 S1" echo >>{var.filename} "M956 P0 A0 S" ^ (var.max_freq - var.min_freq) * var.datarate * var.hz_per_sec echo "Testing " ^ floor(var.freq) echo >>{var.filename} "echo " ^ var.freq while var.freq < var.max_freq + 0.000001 set var.t_seg = 0.25 / var.freq set var.accel = var.accel_per_hz * var.freq set var.max_v = var.accel * var.t_seg echo >>{var.filename} "M204 P" ^ var.accel ^ " T" ^ var.accel set var.L = 0.5 * var.accel * (var.t_seg*var.t_seg) set var.nX = (var.sign * var.L) echo >>{var.filename} "G1 " ^ var.axis ^ var.nX ^ " F" ^ var.max_v*60 echo >>{var.filename} "G1 " ^ var.axis ^ -var.nX set var.sign = -var.sign set var.old_freq = var.freq set var.freq = var.freq + (2. * var.t_seg * var.hz_per_sec) if floor(var.freq) > floor(var.old_freq) ;echo >> var.filename "echo " ^ floor(var.freq) echo "Testing " ^ floor(var.freq) echo >>{var.filename} "G90" echo "total time " ^ state.upTime - var.stime
-
RE: Euclid probe kit with hardware in EU?
@zapta said in Euclid probe kit with hardware in EU?:
this is very useful. Where can I find the STL models?
https://github.com/nionio6915/Euclid_Probe/tree/main/stls/Voron
Think (probably) I used VoronGantryMount2_Bkt.stl and VoronGantryMount2NativeCarriage.stl
They could be optimized further but works fine as is for me.
-
RE: Y Homing on CoreXY
OK, I have a 2.4 as well and even though mine isn't a standard setup I home it on max (300, 305) in the top right corner.
I see two things when looking quickly:
- In the homey.g you go relative +360mm and then back up by trying to go relative +5 mm if I read it correctly?
- I have a pullup on my switches
; Endstops M574 X2 S1 P"^121.io0.in" M574 Y2 S1 P"^0.io1.in" M574 Z0 p"nil"
-
RE: wiring endstops on duet 3 6hc
@theolodian As a note, I've just learned that there is no need to enable the internal pullups on Duet 3 hardware since there are already external pullups for all inputs.
-
RE: Canned ERCF board v1.0-beta2
Apologizes to those who contacted me about the board, I have been (and still am) a wee bit under the weather but I'll respond to you shortly.
Anyway, I thought that a good test for the board would be to hook it up to drive the A & B motors on the Voron V0.1 running two Nema 14 motors at 1200 mA at 4000 mm/s^2 (5000 travel) and see what happens.
Said and done. Start:
https://youtu.be/Jh0_QzTjQ-QEnd:
https://youtu.be/QYoGkQ9I5lcFinished test print:
With this I'm pretty sure it will ahev no problems winding some filaments up and down with th ERCF
Btw, the enraged rabbit feeder is on the way
I have another new version in mind that utilizes more Duet hardware but it requires more changes to the firmware changing the slave addressing. Shouldn't be more that a few places. Maybe a couple of ifdefs is enough
I just love the Duet hardware and RRF. Swap two drive cables. change two lines in the config.g and restart and you have swapped motor drivers to another board.
-
RE: (EDIT) Already supported in RRF - Mesh probing with Rel Ref Ind
@dc42 I apologize if my questions seem stupid but my intentions are only to understand how to get it to work as I want.
I have now done some more testing and ...
... Yes, I have misunderstood the term of setting Z0 with the probe as I read that as setting the absolute Z0 position using the probe.
So by issuing the G30 command I set the z coordinate to the probe trigger height (probe offset) and thereby effectively cancelling the probe offset from the rest of the mesh points.
Then it works as I like and I can scrap this whole thread.
My config (that I borrowed starting with RRF a couple of weeks ago) didn't produce a correct mesh since it was obviously configured wrongly and together with a height value that differed a bit from zero probably due to probing inaccuracy led me to believe it worked in a different way than it does.
Well, I learned something new today, it took awhile though
BTW: The -3 flag to the G30 will produce the same result just the other way around, adjusting the probe offset instead of the read height value ?
Thanks
/U -
RE: RRF v3.3/Mini 5+ Wifi - Major problems with layer shifting
@fcwilt I should actually amend my comment. It could be old topics. So I really don't know and shouldn't make such statements.
It's getting late
I might have to edit this a bit tomorrow
Cheers
-
RE: TMC2660 problem
@jerolee Are you absolutely sure about the motor wiring? I have a similar motor (17mm) in my V0.1
My connector is red, green , yellow, blue as described below. Yours doesn't seem to be connected the same way. I assume you have checked this as you've measured the resistance.
https://cdn.shopify.com/s/files/1/0239/9287/files/HT_LDO-36STH20-1004AHG_XH_RevA.pdf
-
RE: Duet 2 wifi, Bltouch won't deploy anymore
@phaedrux said in Duet 2 wifi, Bltouch won't deploy anymore:
I wonder whatever happened to that guy...
AFAIK, he's alive and happy tinkering with other stuff
-
RE: Neopixel support on 1LC?
Yep, that would be really great.
The new voron toolhead is coming soon with nozzle lights (and a bling lit logo.)Would be nice to combine with the 1LC. I need only two max three leds.
Voron Design Stealthburner yet to be public -
RE: RRF v3.3/Mini 5+ Wifi - Major problems with layer shifting
EDIT: I almost forgot. I'm an ungrateful git. Big thanks to everyone that has helped trying to pinpoint the problem.
Finally! Swapped out the Voron branded 0.9 LDO 42STH40-2004MAC with the OMC 17HS19-2004S1 1.8 degr motors and YES it comes out as it should. Btw, all grub screws and pullies were rock solid. The belts ran super smooth and was even and the gantry wasn't racked but super square
I removed all drive mod config (D2 etc..) and just ran it vanilla.
Much more silent as well
Conclusion (I hope), must be after 20 something failed prints that either this setup just doesn't work with these 0.9 degr stepper motors unless you configure it some way unknown to me or I have faulty motors. Then again I came from a fast working setup where I regulary printed with 5000+ acceleration with these.
I just don't know. I just hope this is history for me now
-
RE: 24v Fans on Duet 3 Mini?
Yes, as long as Vin is 24V that's not a problem. They might already be set to 24V (Vin).
I assume you mean the Duet 3 Mini 5+ board version 1.0 (ish)?
I run two fans on 24V and two other on 12V.
-
RE: Dynamic settings / dampen vibrations
@romeofox FWIW, I have never seen a Voron 2.4 with a ZVD (resonance) frequency of 15Hz.
It's pretty normal around early 60 Hz X and about late 40 Y unless something is loose.