Setting the max temperature with M143 helped and I am up and running.
Thanks for the help, and thanks for a great platform.
--bill
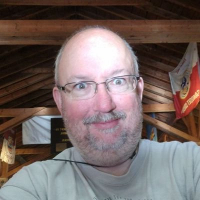
Posts made by Billwhit
-
RE: Heater config struggles
-
RE: Heater config struggles
@dc42 They are very stable after 75C but at room temp they flop around to almost +/-15C.
The TValues were provided by the manufacturer.
I have only had the patience to get all three of them up to 300C, and that took almost an hour of sitting by the console and resetting the faults. I have made a couple test prints at 250 and the sensors are stable.
-
RE: Heater config struggles
@Phaedrux
The heaters are 110VAC controlled by 3 DC-AC SSR relays.
They are 450,250, and 100 watts, respectively.If I start from room temp, we get the "temperature not reached" error.
-
RE: Heater config struggles
Thank you for the information!
My M143 is back in.
Here is my config.g
The heaters and thermistors are custom from my extruder vendor. -
Heater config struggles
I have a pellet extruder with 3 heaters. Each heater and thermistor is rated up to 500C.
The sensors are not stable at room temperature, so I have been running the heater tuning by starting at a higher temperature (75-100C). I have been able to complete tuning up to 250 (M303 h2 S250) but any higher and the tuning will time out before completing.
I cannot set an active temperature for any of these heaters without a half hour of heating fault->reset fault->set heater active cycles.
The tuning parameters are not right, because I get overshoots when trying to go from 240-250, for example.We no longer have a simple command to tell RRF that the max temp for this sensor/heater is 480C (M143).
Can anyone suggest some configuration or tuning tricks to get these heaters tuned properly?Running a Duet 2 ethernet board, RRF 3.1.1.
Thanks in advance. -
RE: Temp Sensor Madness
Things are working.
I added ferrite cores on the motor output lines of the external stepper drivers, to help reduce the noise. I made sure all the cable shields, power supplies, and drivers are on the same ground. And finally I wrapped the TC in a layer of kapton tape to make sure it wasn't grounding against the nozzle housing. -
RE: Temp Sensor Madness
I failed to mention the basics:
Firmware Version: 2.02(RTOS) (2018-12-24b1)
Web Interface Version: 1.22.6
This is an IDEX sort of mechanism with 2 independent X drives on a moving Y gantry.
There are external stepper drivers Wantai DQM542 and the motors are big Nema23's with part number 23HS45-4204S.
I replaced the Arduino/ramps hardware with the Duet board, and replaced the overstuffed direct-wired electronics cabinet with a larger industrial enclosure. -
RE: Temp Sensor Madness
UPDATE: No chance to apply a 'scope to look at the signals, so I am using lower-tech methods. I have reverted back to the thermocouple daughterboard and my previous sensors. I was able to get a good solid temperature reading from the Duet, but only if I disabled all my external stepper drivers by disconnecting their power. As soon as I connected power to even one driver, the temperature returns to 2000C, and the fault LED on the daughter board flashes about once per 1-2 seconds.
I will continue to seek the interference source(s) that are preventing me from running and will let you know the results. -
RE: Temp Sensor Madness
The cap(s) didn't help. We are going to try getting a scope on the cable this weekend and see what is happening.
-
RE: Temp Sensor Madness
I made some more tests. Replaced the CAT5 with some 22gauge shielded cable with stranded vs solid conductors. Resistance of my cable with my multimeter seems to be 7-8 Ohms on each individual conductor. I have the 2-wire PT100 wired up in 4-wire configuration with the jumpers removed on the daughterboard. I still get a solid 2000C temperature, even with the included resistor instead of the sensor. If I shorten the cable, the sensor reads correctly.
I am unable to shorten the cable enough to make a difference with my machine geometry.
Is there a way to introduce a cable length compensation for temperature sensors?
Other ideas? -
RE: Temp Sensor Madness
@bpislife These are good points to check. I will investigate when I am back at the machine. I used conventional cat5e cable because of the colored pairs and the shielding to help me keep things correctly wired. I did remove the jumpers when I did the 4wire, per the documentation. I am not giving up hope just yet. Thank you.
-
RE: Temp Sensor Madness
@aidar Agreed. This line was an artifact from my thermocouple tests, and I should have dropped it. I am going to head back to the machine this evening and do some more investigating re: the resistance across my cables and noise reduction. Thanks @Dougal1957 and @Wyvern as well for the info.
-
Temp Sensor Madness
Background: I have been struggling with the commissioning a large format printer that I am rebuilding. The focus seems to be the temperature daughterboards and my long, noisy cable run. The machine has cable run from the Duet3d cabinet to the hotend of almost 10 meters. All the drive/signal cables run through drag chains in a large bundle. I have grounded the shields of all the motor cables at the computer end of the harness. I have replaced a working Ramps/Arduino controller with the Duet3d Ethernet and the machine was coming back online well. The old cabinet was very tightly packed with no room for expansion, so I have installed everything in a larger, more appropriate enclosure with room to grow.
I am using external stepper drivers for the axes (the same ones that were installed before) and motion and endstops are working well. I have the expansion breakout board with all the steppers connected there, including one for the extruder. I also am using an SSR for the heater control. Each axis/extruder has it's own power supply, as does the computer.
I have attached a copy of my config.g but at this point there are no fans, nothing extra connected to the computer except power, ethernet cable, and the above hardware.
0_1549725201948_config.gMy central problem is that I have tried both K-type thermocouples and PT100 sensors but I cannot seem to get a stable temperature reading from the hotend. It always goes to 2000C. I currently have a new PT100 daughterboard and sensor. If I connect the resistor to the PT100 at the daughterboard, it works fine (0-0.2C). The existing wiring seemed sketchy, so I took a long piece of Cat 5, used 2 pairs to rig up the sensor as a 4wire PT100 (as DC showed in the wordpress article) thinking that the twisted pairs of the cat5 would help me, but again I get a solid 2000C with the resistor or the sensor. I can't do much more commissioning of this machine until I can get a solid temperature.
-
RE: End stop LEDs flickering
Yes the cables do run together in a large bundle from the machine to the cabinet with the Duet. The switches are configured as normally closed at the moment, but it would be easy to make them N.O.
-
RE: End stop LEDs flickering
I have a 12VDC supply connected to the Power In connections, .
-
RE: End stop LEDs flickering
They are bare wired microswitches.They are wired to pins 1 and 3 of the connectors on the board.
-
End stop LEDs flickering
Hi I have a Duet2 ethernet board, running firmware 2.02, on a large custom printer.
I am seeing the endstop LEDs go bright red when the microswitch is triggered, but afterwards, they remain faintly lit and flickering. Is this normal?