Hi everyone, I recently installed the Duet 2 wifi board on my Modix Big-60 with a CR Touch (metal pin) and everything seems to be working fine. The X and Y endstops are located on the left in the back and the printer homes X, Y and Z as it should. However.. when I slice a print in Cura 4.8.0 or Simplify3D, the printer homes in the back left as expected and then rushes and crashes into the front. In order to make everything work I had to switch the X and Y on the board. To eliminate the problem I removed everything except G28 from the start-Gcode in Cura. Below my config.g, homeall.g, and everything else which could be of importance. Many thanks in advance for any input which could solve my problem. I'm getting an Akismet Spam error when trying to post so placing it all in a text file.
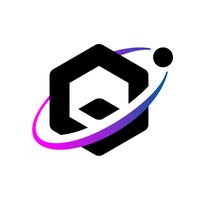
Best posts made by 3dorbit
-
Help! Print starts opposite of home
Latest posts made by 3dorbit
-
G28 Z "Error: probe 0 not found"
The Z axis home'd properly one week ago, but not anymore.
The BL touch itself is good, and i cannot remember remotely touching it in the config.
I don't know what to do, please help.; Configuration file for Duet WiFi (firmware version 3.3)
; executed by the firmware on start-up
;
; generated by RepRapFirmware Configuration Tool v3.3.10 on Sat Jan 08 2022 17:50:57 GMT+0100 (Midden-Europese standaardtijd); General preferences
M575 P1 S1 B57600 ; enable support for PanelDue
G90 ; send absolute coordinates...
M83 ; ...but relative extruder moves
M550 P"Modix Big-60" ; set printer name; Network
M552 S1 ; enable network
M586 P0 S1 ; enable HTTP
M586 P1 S0 ; disable FTP
M586 P2 S0 ; disable Telnet; Drives
M569 P0 S0 ; physical drive 0 goes forwards. X-Axis.
M569 P1 S0 ; physical drive 1 goes forwards. Y-Axis.
M569 P2 S0 ; physical drive 2 goes forwards. Z-Axis.
M569 P3 S1 ; physical drive 3 goes forwards. E0-Extruder.
M584 X0 Y1 Z2 E3 ; set drive mapping
M350 X16 Y16 Z16 E16 I1 ; configure microstepping with interpolation
;M92 X80.00 Y160.00 Z400.00 E420.00 ; set steps per mm
M92 X100 Y195 Z2000 E418.5:418.5
M566 X900.00 Y900.00 Z60.00 E120.00 ; set maximum instantaneous speed changes (mm/min)
M203 X6000.00 Y6000.00 Z2000.00 E1200.00 ; set maximum speeds (mm/min)
M201 X500.00 Y500.00 Z100.00 E250.00 ; set accelerations (mm/s^2)
M906 X1800 Y1800 Z2400 E1000 I40 ; set motor currents (mA) and motor idle factor in per cent
M84 S30 ; Set idle timeout; Axis Limits
M208 X0 Y0 Z0 S1 ; set axis minima
M208 X610 Y610 Z610 S0 ; set axis maxima; Endstops
M574 X1 S1 P"!^xstop" ; configure switch-type (e.g. microswitch) endstop for low end on X via pin xstop
M574 Y1 S1 P"!^ystop" ; configure switch-type (e.g. microswitch) endstop for low end on Y via pin ystop
M574 Z1 S2 ; Define Z to use BLTouch probe; Z-Probe BLTouch on Duet WiFi
M950 S0 C"exp.heater7" ; create servo pin 0 for BLTouch
M558 P7 C"^zprobe.in" H15 F120 T3000 A5 ; set Z probe type to bltouch and the dive height + speeds
M280 P7 S10 ; send control signal to BLTouch through servo/gpio 0"
G31 X20 Y0 Z3.3 P25; Heaters
M308 S0 P"bedtemp" Y"thermistor" T100000 B4138 ; configure sensor 0 as thermistor on pin bedtemp
M950 H0 C"bedheat" T0 ; create bed heater output on bedheat and map it to sensor 0
M307 H0 B1 S1.00 ; enable bang-bang mode for the bed heater and set PWM limit
M140 H0 ; map heated bed to heater 0
M143 H0 S120 ; set temperature limit for heater 0 to 120C
M308 S1 P"e0temp" Y"thermistor" T100000 B4138 ; configure sensor 1 as thermistor on pin e0temp
M950 H1 C"e0heat" T1 ; create nozzle heater output on e0heat and map it to sensor 1
M307 H1 B0 S1.00 ; disable bang-bang mode for heater and set PWM limit
M143 H1 S280 ; set temperature limit for heater 1 to 280C; Fans
M950 F0 C"fan0" Q500 ; create fan 0 on pin fan0 and set its frequency
M106 P0 S0 H-1 ; set fan 0 value. Thermostatic control is turned off
M950 F1 C"fan1" Q500 ; create fan 1 on pin fan1 and set its frequency
M106 P1 S1 H1 T45 ; set fan 1 value. Thermostatic control is turned on; Tools
M563 P0 D0 H1 F0 ; define tool 0
G10 P0 X0 Y0 Z0 ; set tool 0 axis offsets
G10 P0 R0 S0 ; set initial tool 0 active and standby temperatures to 0C; Custom settings are not defined
; Miscellaneous
M501 ; load saved parameters from non-volatile memory
M911 S10 R11 P"M913 X0 Y0 G91 M83 G1 Z3 E-5 F1000" ; set voltage thresholds and actions to run on power loss -
RE: scaling and bed seize trubel
thank you @droftarts , the Y axis indeed had the wrong amount of teeth
-
RE: scaling and bed seize trubel
@Phaedrux
the prints i tried to make we're meant to be circular, instead they came out oval. so i tried scaling the axis but later i figured out the Y axis didn't fully cover the bed. the Y axis was scaled properly but the same as the X axis but it could only do it well if i said the bed was 3~ times as long.I don't know whether this is a software of hardware problem, 'cos we've already replaced the motors, and now we're trying to remove the mistakes from the config.g
-
scaling and bed seize trubel
i am having a lots of problems with prints coming out in the wrong shape and the bed axis limits seems wrong but i can move the head all over the bed now butt stil the prints are miss shaped. are there any obvious mistakes
; Configuration file for Duet WiFi (firmware version 3.3)
; executed by the firmware on start-up
;
; generated by RepRapFirmware Configuration Tool v3.3.10 on Sat Jan 08 2022 17:50:57 GMT+0100 (Midden-Europese standaardtijd); General preferences
M575 P1 S1 B57600 ; enable support for PanelDue
G90 ; send absolute coordinates...
M83 ; ...but relative extruder moves
M550 P"Modix Big-60" ; set printer name; Network
M552 S1 ; enable network
M586 P0 S1 ; enable HTTP
M586 P1 S0 ; disable FTP
M586 P2 S0 ; disable Telnet; Drives
M569 P0 S0 ; physical drive 0 goes forwards. X-Axis.
M569 P1 S0 ; physical drive 1 goes forwards. Y-Axis.
M569 P2 S0 ; physical drive 2 goes forwards. Z-Axis.
M569 P3 S1 ; physical drive 3 goes forwards. E0-Extruder p3 s1.
M584 X0 Y1 Z2 E4 ; set drive mapping E3=E0
M350 X16 Y16 Z16 E16 I1 ; configure microstepping with interpolation
M92 X80.00 Y80.00 Z400.00 E420.00 ; set steps per mm
M566 X900.00 Y900.00 Z800.00 E120.00 ; set maximum instantaneous speed changes (mm/min)
M203 X6000.00 Y6000.00 Z4000.00 E1200.00 ; set maximum speeds (mm/min)
M201 X500.00 Y500.00 Z300.00 E250.00 ; set accelerations (mm/s^2)
M906 X1800 Y1800 Z2400 E1000 I40 ; set motor currents (mA) and motor idle factor in percent
M84 S30 ; Set idle timeout; Axis Limits
M208 X-300 Y-100 Z0 S1 ; set axis minima
M208 X300 Y1200 Z610 S0 ; set axis maxima
;M208 X0:600 Y0:600 Z-1:660 ; 101222 Set axis minima and maxima; Endstops
M574 X1 S1 P"!^xstop" ; configure switch-type (e.g. microswitch) endstop for low end on X via pin xstop
M574 Y1 S1 P"!^ystop" ; configure switch-type (e.g. microswitch) endstop for low end on Y via pin ystop
M574 Z1 S2 ; Define Z to use BLTouch probe;M579 X1.0 Y1.0 Z1.0
; Z-Probe BLTouch on Duet WiFi
M307 H7 A-1 C-1 D-1 ; Disable heater 7 for BLTouch
M950 S0 C"exp.heater7" ; create servo pin 0 for BLTouch
M558 P9 C"^zprobe.in" H15 F120 T9000 ; set Z probe type to bltouch and the dive height + speeds
M280 P0 S10 ; send control signal to BLTouch through servo/gpio 0"; Heaters
;M308 S0 T500000 B4723 C1.196220e-7 ; Set thermistor + ADC parameters for heater 1 ; configure sensor 1 as thermistor on pin e0temp
;M308 S0 P"e0temp" Y"thermistor" T100000 B4725 C7.060000e-8 A"Hotend"
M308 S1 P"e0temp" Y"thermistor" A"e0_heat" T500000 B4723 C1.196220e-7 ;Slicer Engineering 405°C thermistor
M950 H1 C"e0heat" T1 ; create nozzle heater output on e0heat and map it to sensor 1
M307 H1 B0 S1.00 ; disable bang-bang mode for heater and set PWM limit
M143 H1 S280 ; set temperature limit for heater 1 to 280C
;M950 H1 C"out1" T1 ; create nozzle heater output on out2 and map it to sensor 1
M307 H1 R2.662 C145.3:136.3 D5.08 S1.00 V24.1
;M307 H1 R2.185 C151.4:140.7 D4.45 S1.00 V24.1
;M307 H1 R2.247 C148.4:132.8 D5.56 S1.00 V24.1 ; disable bang-bang mode for heater and set PWM limit; Fans
M950 F0 C"fan0" Q500 ; create fan 0 on pin fan0 and set its frequency
M106 P0 S0 H-1 ; set fan 0 value. Thermostatic control is turned off
M950 F1 C"fan1" Q500 ; create fan 1 on pin fan1 and set its frequency
M106 P1 S1 H1 T45 ; set fan 1 value. Thermostatic control is turned on; Tools
M563 P0 D0 H1 F0 ; define tool 0
G10 P0 X0 Y0 Z0 ; set tool 0 axis offsets
G10 P0 R0 S0 ; set initial tool 0 active and standby temperatures to 0C; Miscellaneous
M501 ; load saved parameters from non-volatile memory
M911 S10 R11 P"M913 X0 Y0 G91 M83 G1 Z3 E-5 F1000" ; set voltage thresholds and actions to run on power loss -
RE: Help! Print starts opposite of home
@phaedrux Thanks for your suggestions! Will try them out and get back to you with the results.
-
RE: Help! Print starts opposite of home
@alankilian No actually homing goes ok. After homing the X and Y positions are both 0.0. After a G1 command both axes move in the right direction as well.
-
Help! Print starts opposite of home
Hi everyone, I recently installed the Duet 2 wifi board on my Modix Big-60 with a CR Touch (metal pin) and everything seems to be working fine. The X and Y endstops are located on the left in the back and the printer homes X, Y and Z as it should. However.. when I slice a print in Cura 4.8.0 or Simplify3D, the printer homes in the back left as expected and then rushes and crashes into the front. In order to make everything work I had to switch the X and Y on the board. To eliminate the problem I removed everything except G28 from the start-Gcode in Cura. Below my config.g, homeall.g, and everything else which could be of importance. Many thanks in advance for any input which could solve my problem. I'm getting an Akismet Spam error when trying to post so placing it all in a text file.