@droftarts I installed HomeBrew and installed wxwidgets as described, and BOSSA worked after that. I am running Catalina 10.15.7.
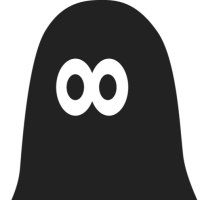
Posts made by Urban
-
RE: Flashing firmware on Mac OS X
-
RE: Different versions of Pt100 Temp Daughterboard
- The wiki links to an earlier post, no picture on the wiki.
- The capacity recommended is different from the 100nF you recommended in this post
- I mounted two 100nF for one channel between the inner pins and ground. I have a four wire configuration with maybe 2m cable. When I use the jumpers on the board to make it a 2-wire configuration the signal is improved significantly. When I remove the jumpers the signal deteriorate.
- The signal is poor even before the first usage of the steppers in the extruder.
- Shouldn't all four pins into the Wheatstone bridge have this capacitor?
I am using the 2-wire connection now (with jumpers) and the result is really good. I will try to add two more capacitors to the same channel (total of 4 per channel ) to see if this improves the 4-wire connection.
-
RE: Different versions of Pt100 Temp Daughterboard
@dc42 said in Different versions of Pt100 Temp Daughterboard:
Alternatively, wire-leaded ones can be soldered on the underside of the board
I could solder the underside with normal capacitors . However, there is no drawing (that I have found) and the text on the board is almost unreadable. I assume the capacitors should be between the two pin pair that can be closed by a jumper?
@bearer Thank you for the info! You know your own hometown least! And maybe I should give SMT a try someday.
-
RE: Different versions of Pt100 Temp Daughterboard
@dc42 I checked the solder pads this morning and I can't solder that small. If you would like you could send me a board with the capacitors on so that I can test it since I have the problem very consistent.
-
RE: Hotend temperature fluctuations
The M301 command. When you do the autotune the PID parameters are printed at the end of the tuning.
Hmm.. I also remember that I forgot to insert the ADC values in the config.g once and they disappeared somehow. Maybe that happened to you as well?
PID is the way you normally control a temperature. This is a good site to explain it:
http://brettbeauregard.com/blog/2011/04/improving-the-beginners-pid-introduction/ -
RE: Different versions of Pt100 Temp Daughterboard
@dc42 OK, thank you.
I have the 1.1a.
Yes, they are isolated and the cable shielded. -
RE: Hotend temperature fluctuations
Maybe you could try the PID settings instead, these should be listed when you autotune. To me it looks like the P part is to high, so try cutting it to half. I would also tune at the temperature that you intend to keep, so 300 in this case.
-
RE: Different versions of Pt100 Temp Daughterboard
@Veti Thank you for responding!
@dc42 OK, Thank you for the info. What type and size of capacitor do you recommend?
I have two daughterboards and one is used for the chamber and bed. These signals are good. For the board used for the two extruders the signal i jittery. I have done an extensive work trying to improve the situation but it is clear that it can't be as good as for the bed-chamber sensors.I have done everything except grounding the hotted itself (tried by holding a ground wire manually, and it did not help). I have a better version of Pt100 that I don't think connect to the heater block, and I have tried several. The jitter can be seen for both channels on one board, but not the other board.
Would it be a good idea for the Duet 3 to have a separat ground connection that you can take to the common ground for the machine?
-
Different versions of Pt100 Temp Daughterboard
Does anyone know the difference between version v1.1 and v1.1a of the Pt100 temperature daughterboard for the duet3D? I can not find 1.1a on GitHub.
I have the problem with spikes in the temperature reading (2000C) that many have reported on the forum, and is wondering if the revision change have been made to improve that. The problems probably come from the steppers used for the extruders by inductance despite having separate, shielded cabels and motor phase twisted pairs.
-
RE: Closed loop for X and Y
@iamturbo1978 You could check out this:
SimplexMotion
They use Out-runners and Hall sensors to read the magnetic field instead of encoders. Contact them directly with a project description if you are interested. I do not think they support linear encoders for position feedback.One advantage with a servo is that you can use a stiffer Polyurethane belt to get a stiffer system with better response and accuracy. The downside is the tuning of the servo that can be time consuming.
In my experience from industrial servo application with linear encoders, the inner loop is the encoder in the rotating servo and the outer loop is from the linear encoder. I think it would be difficult to control a servo with only the linear encoder.
I have build a screw based system that can go fast (1m/s) and accurate and the limiting factor I found was the extruder (with gear) that has difficulties providing a smooth flow during accelerations, specially with pressure advance that creates higher pressure. The effect is similar to ghosting, so it took a while to figure out the cause. I print at 150mm/s (limited by the melting of plastic) and with conservative values for acceleration.
-
RE: Stop or jerk during high speed non extruding moves
I see what you are getting at
- I will check if there are any hiccups.
- Yes, I do. The mesh could fit the stops.
- The Z jerk is 0. I set it to zero in an attempt to reduce ringing in the platform from z-hop. Never thought of that it could influence xy-movements.
I will test to increase the Z jerk. Thank you for the tip!
-
Stop or jerk during high speed non extruding moves
When I start a print from the maintenance station to the first extruding position the move stops shortly or maybe it is jerky. This happens after approximately 200mm (I have to make a high speed movie because it is really almost impossible to see what is happening).
The speed is 500mm/s and
M204 P2000 T6000
.I user a 20 mm lead ballscrew with 3200 steps per revolution. This gives 20mm/3200=0,0063mm per step. (The maximum speed for 180kHz would then be 1134mm/s.)
The move for 200mm is then approximately 30000 steps.
Does anyone have an idea of why this is happening?
-
RE: Driving micro steppers with DuetWiFi
OK, thank you!
-
Hmm, would it work to connect a stepper with similar inductance (4.7mH) in parallel to start with?
-
I was hoping to get away without doing that, but there are some sticks that are made for low voltage, like 5V, that could be used.
-
Can you please expand on why full step mode is better.
-
The chip on the duetWiFi doesn't have Trinamic StealthChop, but would that mode improve the capability to use micro steppers?
-
-
Driving micro steppers with DuetWiFi
I am trying to use the duetWiFi built in stepper drivers to move two micro steppers. The steppers will be used to switch tool on a printer.
The diameter is 15mm and the
- inductance per phase is 14mH
- resistance per phase is 39 ohm
- max current 100mA
I am using 24V.
The problem is that the motors move unpredictable and even continue to move when the move is finished. It also get very hot. The signal on the scope is mostly noice and it is impossible to get a clean trigger on the signal. I have set the the current to 100mA, and I think this is the minimum you can set. If I connect a small, but more normal stepper, everything works as expected.
Does anyone have experience in how to drive such small motors using the Trinamic chip?
Would it help to connect two power resistor in series? 200ohm?
Is there any setting in the Trinamic driver that can be changed to improve the situation?
-
RE: Rippels and Ghosting on Y-Axis of converted Ender 3
@devleon Can you:
- Confirm that you are using a Bondtech BMG with 1.75mm filament
- Measure 5 to10 waves as exactly as you can and calculate the average distance
- Tell us what the extruded width and layer height you are using
- The number of steps per mm
- and how many micro steps per full step (16?)
- how many full steps per turn the stepper has (200 or 400)
This is enough to calculate if it is the cogging that is causing you problem.
-
RE: Rippels and Ghosting on Y-Axis of converted Ender 3
@devleon said in Rippels and Ghosting on Y-Axis of converted Ender 3:
I just finished printing my XYZ cube as well, but I'm honestly baffled, and I really don't know how to interpret these results. I have never seen a texture like this before... I mean, it looks cool, but not perfect the way I want it, and I knew my printer could do better.
The Bondtech has 50 cogs on the plastic gear. (The gear on the motor has 17.) I have patterns very similar to yours as well. Can you relate the frequency on your parts to 50, each time a plastic cog hits a cog on the motor gear?
Do you use pressure advance?
Is the amplitude reduced if you increase the temperature 30C ? This would lower the viscosity and reduce the pressure and thereby lowering the force on the cogs.
-
RE: Patterns that change with Pressure Advance
The 400steps/turn motor did not make any difference. It could be the gears in the Bondtech BMG or the pressure advance that cause the problem. It is clear that the section with the lowest setting of pressure advance has the best surface.
-
RE: Patterns that change with Pressure Advance
@bot OK, thank you. I have now tried increasing the current to the extruder motor and different settings for the micro-stepping. A also repositioned the motor gear. Very little difference.
This could also be a gear problem since there are 4 tooth per step in the extruder.
@Phaedrux I redid the PID and this time I saved the result in the config-file. No difference.
It will be interesting to see the effect of the 400step/turn extruder motor.
-
RE: Patterns that change with Pressure Advance
@bot Can you expand on "low E-resolution". Do you mean the gear ratio in the extruder?
Actually it could be exactly one step, depending on how I interpret the reflections of the part.@Phaedrux I did make a PID, but I have not inserted the result in an M307?, and I am not sure the result is stored automatically. The mass (or heat capacity) of the copper block gives a longer heating time and the graph in the web-UI is fairly stable (+/- 0.2C). I use Pt100 with the special board sold by Duet3D.
-
RE: Patterns that change with Pressure Advance
@bot
I have a Bondtech with 420 (micro-)steps/mm. I use 16 micro steps with interpolation. This give 26.25 full steps /mm.The pattern is 3.12mm. The nozzle is 0.4mm. The filament 1.75mm.
The area ratio between filament and nozzle is 1.751.75 / (0.40.4) = 19.14
The amount of filament used for one pattern cycle is then:
3.12 / (2*19)= 0.0821mm filament.The number of steps would be:
0.0821mm filament * 420 micro-steps / mm = 34.48 micro-stepsSo the pattern is 34 micro-steps and there are 16 micro-steps for a full step. Maybe the pattern could also be twice as long since I looked on reflections and did not measure the actual hight?
The gearing has 17 and 50 teeth, and would generate a higher frequency.
The gears on the hob has 17 teeth.
The motor is 25mm long and I use 1000mA instead of the recommended 700mA.
Is there something wrong with the calculations?
I will get a 400steps/turn motor from Bondtech and test how that influence the result.
Maybe the newly fitted E3D copper nozzle and block has less/more friction and flow resistance?
I am pretty sure that an increase of the temperature with 20C reduced the amplitude of the pattern due to lower viscosity of the plastic, but this could also be an optical illusion since the part became more glossy.