I ordered a new BL Touch, installed it and now works perfectly. Looks like it was defective all along.
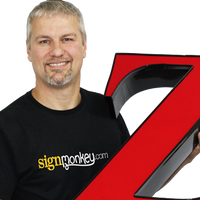
Best posts made by SignPostMan
-
RE: BL Touch Installation what is Servo Pin?
-
RE: Understanding Endstop and Z Probe
Thanks everyone for your input!
I think I got it.
I removed the Z-Probe pin, and it now works completely.
-
RE: Mesh bed leveling Z Endstop switch
@jay_s_uk OK, Thanks
Thanks for your help Jay_s_uk -
RE: G30 Lifts to high after probing
@jay_s_uk Oh wow, I looked but did not see, thanks.
-
RE: BL Touch Installation what is Servo Pin?
@fcwilt I am able to trigger the probe with M401 and M402
-
RE: BL Touch Installation what is Servo Pin?
@fcwilt yes BL Touch brand
-
RE: BL Touch Installation what is Servo Pin?
@fcwilt will try in the morning, thanks for your help
-
RE: BL Touch Installation what is Servo Pin?
Yes Black and Brown connected to the same pin
-
RE: BL Touch Installation what is Servo Pin?
@phaedrux I did go through that but couldn't get past this part. I think I am going to wait and see if a new probe works. Thanks for all your help, I will let you know if new probe make a difference.
Latest posts made by SignPostMan
-
RE: Repeated Deploy and Retract Probe G32
@oliof That worked! One more thing, it will take the probe to the middle of the bed and then go to the 1st probing point, do you have any idea why?
-
Repeated Deploy and Retract Probe G32
I have 3 Z motors and I am using a Euclid Probe that must be picked up before probing bed. When I run G32, the probe will be picked up and returned between each of the three probing locations. Don't know enough to determine why?
M561 ; clear any bed transform G30 P0 X4.5 Y14.65 Z-99999 ; probe near a leadscrew G30 P1 X311 Y625.65 Z-99999 ; probe near a leadscrew G30 P2 X618.5 Y14.65 Z-99999 S3 ; probe near a leadscrew and calibrate 3 motors
-
RE: Issue Leveling with G32 using 4 lead screws and motors
G90 ; send absolute coordinates... M83 ; ...but relative extruder moves M550 P"RR 650-1" ; set printer name M669 K1 ; CoreXY G21 ; Set Units to Millimeters M552 S1 ; enable network M586 P0 S1 ; enable HTTP M586 P1 S0 ; disable FTP M586 P2 S0 ; disable Telnet M569 P0.0 S1 ; physical drive 0.0 goes forwards M569 P0.1 S1 ; physical drive 0.1 goes forwards M569 P0.2 S1 ; physical drive 0.2 goes forwards M569 P0.3 S1 ; physical drive 0.3 goes forwards M569 P0.4 S1 ; physical drive 0.4 goes forwards M569 P0.5 S0 ; physical drive 0.5 goes forwards M569 P0.6 S0 ; physical drive 0.5 goes forwards M584 X0.5 Y0.6 Z0.0:0.1:0.2:0.3 E0.4 ; set drive mapping M350 X16 Y16 Z16 E16 I1 ; configure microstepping with interpolation M92 X80.00 Y80.00 Z800.00 E400 ; set steps per mm M906 X1600 Y1600 Z1600 E700 I30 ; set motor currents (mA) and motor idle factor in per cent -- safe for Duet 3 mini 5+ M84 S30 ; Set idle timeout M566 X600.00 Y600.00 Z8.00 E120.00 P1 ; set maximum instantaneous speed changes (mm/min) M203 X30000.00 Y30000.00 Z1600.00 E6000.00 ; set maximum speeds (mm/min) M201 X3000.00 Y3000.00 Z100.00 E3600.00 ; set accelerations (mm/s^2) M208 X0 Y0 Z0 S1 ; set axis minima M208 X650 Y650 Z480 S0 ; set axis maxima M574 X1 S1 P"io2.in" ; configure active low endstops M574 Y2 S1 P"io1.in" ; configure active high endstops ;(PanelDue is on io0) M671 X26:26:685:685 Y29:686:686:29 S5 ; position of leadscrew/bed pivot point at front left, rear left, rear right and front right M557 X30:618 Y30:650 S50 ; define 5x5 mesh grid ;PanelDue set baud rate----------------------------- M575 P1 B57600 S1 ;--------------------bed need work------------------ M308 S0 P"temp0" Y"thermistor" T100000 B3950 A"Bed" ; configure sensor 0 as thermistor on pin temp0 M950 H0 C"out0" T0 Q11 ; create bed heater output on out5 and map it to sensor 0, lower switching frequency to 11Hz M307 H0 B0 S1.00 ; disable bang-bang mode for the bed heater and set PWM limit ;M307 H0 A240.3 C608.7 D8.2 V24.1 B0 ; Bed Heater from other printer M140 H0 ; map heated bed to heater 0 M143 H0 S110 ; set temperature limit for heater 0 to 110C ;------------------Chamber Temp--------------------- M308 S2 P"temp1" Y"thermistor" T100000 B3950 A"Chamber"; configure sensor 2 as thermistor on pin temp2 M950 H2 C"out2" T2 ; create chamber heater output on out2 and map it to sensor 2 ;M307 H2 B0 S1.00 ; disable bang-bang mode for the chamber heater and set PWM limit M307 H2 R6 K0.17:0.11 D5.67 S1.00 ; set the process parameters for heater 1 M141 H2 ; map chamber to heater 2 M143 H2 S70 ; set temperature limit for heater 2 to 60C ;---------------------Fans------------------------- M950 F0 C"out4" Q500 ; create fan 0 on pin out4 and set its frequency M106 P0 C"Layer Fan" S0 H-1 ; set fan 0 name and value. Thermostatic control is turned off M950 F1 C"out3" Q500 ; create fan 1 on pin out3 and set its frequency M106 P1 C"Hotend Fan" S0 H1 T45 ; set fan 1 name and value. Thermostatic control turned on for Hotend M950 F3 C"out6" ; create fan 3 on pin out5 M106 P3 C"Chamber Filter Fan" S1 H2 T45 ; set fan 3 name and value. Thermostatic control turned on for Chamber Temp ;---------------------------------------- M563 P0 D0 H1 F0 ; define tool 1 G10 P0 X0 Y0 Z0 ; set tool 1 axis offsets G10 P0 R0 S0 ; set initial tool 1 active and standby temperatures to 0C M950 H1 C"out1" T1 ; create nozzle heater output on out2 and map it to sensor 1 M307 H1 B0 S1.00 ; disable bang-bang mode for heater and set PWM limit M143 H1 S350 ; set the maximum temperature in C for heater T0 M308 S1 P"spi.cs2" Y"rtd-max31865" ; configure sensor 1 as PT100 on pin spi.cs1 ;----Euclid Probe------------------------ M558 P8 C"io3.in" H5 F800 T10000 ; set Z probe type to unmodulated and the dive height + speeds G31 P500 X-31.5 Y0 Z3.4 ; set Z probe trigger value, offset and trigger height, more Z means closer to the bed ; Pressure Advance M572 D0 S.055 ;set tool 0 pressure advance M593 P"zvd" F41.5 ; use ZVD input shaping to cancel ringing at 40.5Hz
-
RE: Issue Leveling with G32 using 4 lead screws and motors
@deckingman I think you may be right. I was hopping for some voodoo, that I didn't know about. Thanks
-
RE: Issue Leveling with G32 using 4 lead screws and motors
@jay_s_uk Ok I will check that out, my bed is 680x680 and I was afraid if I used 3 points I would get to much sag in back corners. Also the bed is 10mm thick and is pretty heavy, so 4 motors handle the weight pretty good. I would also like to make even larger and proving out the 4 motors first.
-
Issue Leveling with G32 using 4 lead screws and motors
I am using a setup like the Rat Rig, where there are steel balls attached to the bed that are sitting on parallel bars. The steel balls can slide to accommodate any movement needed to sit level. Gravity and a small magnet is all that holds the bed ball on the parallel bars. This system works great and I am getting good first layers when I use a dial indicator to level the bed prior to running G32. Then of course G29 to build a mesh.
The problem I am having, is when running G32, the bed will try to compensate by lower one of the screws to low, this makes to ball in that corner no longer touch the parallel bars. Trying to by running G32 again only make the problem worse. Are there any kind of a solution for this issue?
-
Z Motors with Different steps per mm
I have 3 motors on my Z and two of them have 20 to 1 gearing and the third has 100 to 1 planetary gearing this is because the entire gantry moves in Z. The third motor would drift down when the power was turned off. The easiest way to fix this was to use a higher gear ratio.
Is it possible to have different gear ratios or steps per mm for each Z motor? -
RE: G30 Lifts to high after probing
@jay_s_uk Oh wow, I looked but did not see, thanks.