I have also tested the firmware and am very satisfied with the improved quality. I haven’t been able to make any fine adjustments yet, but I have increased the speed by 50mm/s as well.
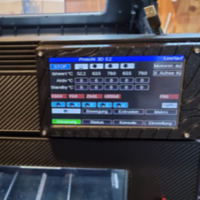
Best posts made by Proschi3D
-
RE: RepRapFirmware 3.6.0-alpha.2 for Duet main boards available
-
RE: U Axis not moving
@SonnyD1 this is my setting of the limit switches with an Idex printer
; Endstops M574 Y1 S1 P"io1.in" M574 X1 S1 P"io2.in" M574 U2 S1 P"io4.in" M574 Z2 S1 P"io6.in"
I think U2 S1 would be correct right?
-
RE: U Axis not moving
; Configuration file for Duet 3 Mini 5+ (firmware version 3.3) ; executed by the firmware on start-up ; ; generated by RepRapFirmware Configuration Tool v3.3.15 on Sat Nov 26 2022 13:27:47 GMT+0100 (Mitteleuropäische Normalzeit) ; General preferences M575 P1 S1 B57600 ; enable support for PanelDue G90 ; send absolute coordinates... M83 ; ...but relative extruder moves M550 P"Proschi 3D E2" ; set printer name ; Network M552 S1 ; enable network M586 P0 S1 ; enable HTTP M586 P1 S0 ; disable FTP M586 P2 S1 ; enable Telnet ; Drives M569 P0.0 S0 D3 H50 V30 ; physical drive 0.0 goes forwards M915 P0.0 T50 M569 P0.1 S1 D3 H50 V30 ; physical drive 0.1 goes forwards M915 P0.1 T30 M569 P0.2 S0 D3 H50 V30 ; physical drive 0.2 goes forwards M915 P0.2 T50 M569 P0.3 S1 D3 H50 V30 ; physical drive 0.3 goes forwards M915 P0.3 T50 M569 P0.4 S0 D3 H50 V30 ; physical drive 0.4 goes forwards M915 P0.4 T50 M569 P0.5 S1 D3 H50 V30 ; physical drive 0.5 goes forwards M915 P0.5 T50 M584 X0.0 Y0.1 Z0.2 E3:5 U4 ; set drive mapping M350 X16 Y16 U16 Z16 E16:16 I1 ; configure microstepping without interpolation M92 X80 Y80 U80 Z800 E286.216 :286.216 ; set steps per mm M566 X480 Y300 U480 Z24 E300:300 ; set maximum instantaneous speed changes (mm/min) M203 X12000 U12000 Y10000 Z600 E3000:3000 ; set maximum speeds (mm/min) M201 X1000 U1000 Y500 Z100 E3000:3000 ; set accelerations (mm/s^2) M906 X850 U850 Y850 Z800 E800:800 I30 ; set motor currents (mA) and motor idle factor in per cent M84 S30 ; Set idle timeout ; Axis Limits M208 X10 Y-3 Z0 U35 S1 ; set axis minima M208 X335 Y255 Z240 U355 S0 ; set axis maxima ; Endstops ; configure switch-type (e.g. microswitch) endstop for high end on Z via pin null M574 Y1 S1 P"io1.in" M574 X1 S1 P"io2.in" M574 U2 S1 P"Io4.in" ;M915 X S-63 H10 R1 ; Set very sensitive stall detect ;M574 X1 S3 ; configure endstop for stall detection ;M915 X S20 H140 R0 ; Set very sensitive stall detect ;M915 X S-63 H10 R1 ; Set very sensitive stall detect ; Filament Sensoren M591 D1 P1 C"io5.in" S1 M591 D0 P1 C"io6.in" S1 ; Z-Probe M558 P1 C"io3.in" H5 A5 S0.005 F150 T6000 ; set Z probe type to unmodulated and the dive height + speeds G31 P500 X10 Y20 Z0.5 ;0.55 Simplify set Z probe trigger value, offset and trigger height M557 X30:330 Y50:210 P3 ; define mesh grid ; Heaters M308 S0 P"Temp0" Y"thermistor" T100000 B4138 ; configure sensor 0 as thermistor on pin temp0 M950 H0 C"out0" T0 ; create bed heater output on out0 and map it to sensor 0 M307 H0 B1 S1.00 ; enable bang-bang mode for the bed heater and set PWM limit M140 H0 ; map heated bed to heater 0 M143 H0 S120 ; set temperature limit for heater 0 to 120C M308 S1 P"Temp1" Y"thermistor" T100000 B4725 C7.06e-8 ; configure sensor 1 as thermistor on pin temp1 M950 H1 C"out1" T2 ; create nozzle heater output on out1 and map it to sensor 1 M307 H1 B0 S1.00 ; disable bang-bang mode for heater and set PWM limit M143 H1 S340 ; set temperature limit for heater 1 to 340C M308 S2 P"Temp2" Y"thermistor" T100000 B4725 C7.06e-8 ; configure sensor 2 as thermistor on pin temp2 M950 H2 C"out2" T1 ; create nozzle heater output on out2 and map it to sensor 2 M307 H2 B0 S1.00 ; disable bang-bang mode for heater and set PWM limit M143 H2 S340 ; set temperature limit for heater 2 to 340C ; Temp Sensoren M308 S10 Y"mcu-temp" A"MCU" ; defines sensor 10 as MCU temperature sensor M308 S11 Y"drivers" A"Duet stepper drivers" ; defines sensor 11 as stepper driver temperature sensor ;M950 F5 C"out6" Q500 ; create fan 2 on pin fan2 and set its frequency ;M106 P5 H3 T40:70 ; set fan 2 value ; Fans M950 F0 C"vfd" Q500 ; create fan 0 on pin out4 and set its frequency M106 P0 C"Extruder&Bauteile" S0 H-1 ;M950 F5 C"out6" Q500 ;M106 P5 C"Board" S0 H-1 M950 F2 C"out3" Q500 ; create fan 0 on pin out4 and set its frequency M106 P2 C"Filter Lüfter" S0 H-1 Q25000 ; set fan 0 value. Thermostatic control is turned off ; set fan 1 value. Thermostatic control is turned off M950 F3 C"out5" Q500 ; create fan 2 on pin vfd and set its frequency M106 P3 C"LED" S150 H-1 ; set fan 2 value. Thermostatic control is turned off M950 F4 C"out4+out4.tach" Q25000 M106 P4 C"Aktiv Kühlung" S0 H-1 ; Create a tool that uses the low end (X) carriage M563 P0 D0 H1 F0 S"linker Extruder" ; tool 0 uses extruder 0, heater 1 and fan 0 G10 P0 X0 Y0 Z0 S0 R0 ; set tool 0 offsets and temperatures ; Create a tool that uses the high end (U) carriage M563 P1 D1 H2 X3 F0 S"rechter Extruder" ; tool 1 uses extruder 1, heater 2, fan 2, and maps X to U G10 P1 Y-0.4 U26.6 Z-0.10 R0 ; set tool 1 offsets and temperatures ; Create a tool that prints 2 copies of the object using both carriages M563 P2 D0:1 H1:2 X0:3 F0:0 S"Duplicate"; tool 2 uses both extruders, hot end heaters and fans, and maps X to both X and U G10 P2 X-25 Y0 U-176.3 Z0 S0 R0 ; set tool offsets and temperatures G10 P2 R0 S0 M567 P2 E1:1 ; set mix ratio 100% on both extruders ;Create a tool that Prints in Mirrior Mode M563 P3 S"Mirror" H1:2 D0:1 X0:3 F0:0 G10 P3 X-25 Y0 U-176.3 Z0 S0 R0 G10 P3 R0 S-2 ; Custom settings are not defined ;Temperatur anpassung MCU M912 P0 S2 ; Miscellaneous M501 ; load saved parameters from non-volatile memory M911 S10 R11 P"M913 X0 Y0 G91 M83 G1 Z3 E-5 F1000" ; set voltage thresholds and actions to run on power loss
-
RE: Simplify3d and Filament Timings
@markz post processing script:
{REPLACE "Material Length" "Filament length"}
-
RE: Sensorless homing with an Idex printer
@oliof OK thank you.
then it is better to apply it only on the y low and z high axis.
and to work with limit switches on the x and u axis -
RE: fan connection on the duet 3 mini
The conversion to the duet 3 mini is complete. Just a few things to adjust. Thank you for your help, you are great
-
RE: Duet2 WiFi Firmware on Raise 3d E2 ?
Hello everyone here who helped me. I was able to successfully install a version that was before 2.02. Then the printer could be updated via the Raise software. The whole thing was worth it for me, because now I have the possibility to control it via octoprint for whatever reason. thank you again
-
RE: Your start.g
M291 P"Start.g wird ausgeführt" S0 M98 P"/Macros/SUB/CheckDoor" ;Door open or closed M561 M106 P3 S0 G4 S1 M106 P3 S25 G4 S1 M106 P3 S0 G4 S1 M106 P3 S25 ;dimme LED for IR Probe M98 P"/Macros/SUB/Preheat" ;Preheat for Loaded Filament if !move.axes[0].homed || !move.axes[1].homed || !move.axes[2].homed G28 G28 Z0 M98 P"/Macros/Buildplate" ;Load Hightmap for Buildplate and Filament M98 P"config_probe.g"
-
RE: Adfruit Np8 on a Duet 3 mini
@oliof It works perfectly with 2 pieces. Thanks
-
RE: Duet2 WiFi Firmware on Raise 3d E2 ?
Wish you all a healthy and better year 2021
-
RE: SFS V2.0 to Duet 3 Mini
@SonnyD1 With version 3.5.2, it works perfectly. I mean my filament sensors on the Duet3 Mini and use two tool boards. Before version 3.5.2, I also got an error message unknown pin name.
-
RE: Two Duet 3 Mini 5+ and two toolboards over CAN
I think I have understood it now?! I go from my first Duet 5 to the first toolboard, then CAN L and H are simultaneously also the output to the 2nd toolboard. From the 2nd toolboard the same then to the endboard Duet 5.
-
RE: 3.5.0-beta.3
@dc42 It was a G1 command in the intro line. The right extruder came too close to the left one. I shortened the movement by 5mm and the message disappeared. Thank you for your explanation
-
RE: Unknown Pin Name
@oliof Exactly. I will try to create a macro like this. I still have about 250mm of filament after the sensor, that should be enough
-
RE: Auto Z offset calibration
it works fine now.
here is the gcode if anyone is interestedvar errorfix = 0.000 ; constant offset G31 Z0 ; set Z-offset to Z=0 echo >"0:/sys/config_probe.g" "G31 Z0" M291 S3 R"Heating up nozzle" P"Wait for the nozzle to reach printing temperatures" M568 P0 S210 ; set tool 0 (primary hotend) temperature to 210c T0 ; select tool 0 (primary hotend) M116 P0 H5 ; wait for temperature to reach within 5c of set temperature M300 S666 P666 ; beep M291 S3 R"Automatic Z Offset Calibration" P"Press OK to continue, or CANCEL to abort" M291 S3 R"Homing axes" P"Remove the puck. The printer will home the X, Y, and Z axises without the puck" M98 P"config_probe.g" ; Load BLTouch probe settings M280 P0 S60 I1 ; clear any probe errors G29 S2 ; cancel mesh bed compensation G91 ; relative positioning M913 X50 ; X axis 50% power G1 H2 Z5 F200 ; lift Z relative to current position G28 X0 U0 Y0 ; Home X,U and Y axis ; go back a few mm M913 X100 ; X axis 100% power G90 ; absolute positioning G1 X{move.axes[0].min+175} Y{move.axes[1].min+110} F6000 ; move to center G1 F600 ; reduce speed G30 ; home Z by probing the bed G31 Z0 ; set Z-offset to Z=0 M564 H1 S0 ; Negative movements are allowed G29 S2 ; cancel mesh bed compensation G90 ; absolute positioning G1 Z35 ; raise Z to 35mm M83 ; relative extruder moves G1 E-5 F300 ; retract 5mm of filament G4 P0 ; wait for the moves to finish M291 S3 R"Clean the nozzle" P"The nozzle has been pre-heated. Clean it from any plastic debris" G1 X100 Y200 F6000 ; go to X100, Y200 G4 P0 ; wait for movements to have stopped M300 S666 P666 ; beep M291 S3 P"Place the offset tool below the nozzle and press OK to perform the macro, or CANCEL to abort" G4 P200 ; wait 200ms G91 ; relative moves G1 H1 Z-19 F50 ; move 19mm down, stop when hitting the offset tool (but don't risk crashing the bed) G92 Z0 ; set current position as Z=0 G4 P200 ; wait 200ms G1 Z11 F200 ; move up 11mm G91 ; relative moves G1 X{sensors.probes[0].offsets[0] * -1} Y{sensors.probes[0].offsets[1] * -1} F1500 ; move nozzle so that BLTouch is in it's position G90 ; absolute moves G30 S-3 ; probes Z and adjusts the probe trigger height to match the actual stop height. G4 P200 ; wait 200ms G91 ; relative movement M568 P0 S0 ; set tool 0 temperatures to 0 var Z_auto_offset = {sensors.probes[0].triggerHeight+var.errorfix} ; math to calculate the BLTouch offset if var.Z_auto_offset < 0.01 M291 S2 R"The nozzle has not touched the puck." P"Please check the guide for troubleshooting" echo "The nozzle has not touched the puck. Please check the guide for troubleshooting" echo >"0:/sys/config_probe.g" "G31 Z-3" elif var.Z_auto_offset >= 0.01 & var.Z_auto_offset < 3.5 echo >"0:/sys/config_probe.g" "G31 Z"^{var.Z_auto_offset} M291 S2 R"Z-offset has been stored" P"the Z-offset has been stored in the config_probe.g file. Verify the value stored with the value displayed in the console" echo "the Z-offset has been stored in the config_probe.g file. The Z-offset is", var.Z_auto_offset, "mm. Remove the offset tool and place it back in the box" elif var.Z_auto_offset >= 3.5 M291 S2 R"Z-Offset is too high" P"Please verify the probe height using the probe-calibration" echo "Z-Offset is too high. Please verify the probe height using the probe-calibration" echo >"0:/sys/config_probe.g" "G31 Z-3" M564 S1 H1 ; Negative movements are forbidden M300 S666 P666 ; beep G91 ; relative moves G1 Z5 ; lift nozzle up 5mm G90 ; absolute moves T-1 ; deselect all tools M18 ; release steppers