@chrishamm Thanks. Regards ssh, I assume that's only on the duets with a RPi or similar. Normal duet controller boatds don't do ssh do they?
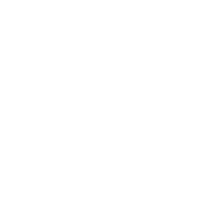
Posts made by DocTrucker
-
RE: Network Security - Which ports do Duets use?
-
RE: Network Security - Which ports do Duets use?
@droftarts Thanks Ian. MQTT is interesting, learnt something by mistake there!
As far as I understand it the Duet never attempts to contact the outside world, other than with clients that have established connection to the HTTP port, or perhaps the MQTT server/client, but I'll read up on that another time.
Knowing what the raspberry pi can be cut back to is a little more tricky as it will have to allow for "apt-get [update/upgrade]" and whatever other applications have been loaded on. I'm thinking about a script that will allow temporary external access for updates.
Just to clarify, I'm not worried about what the duets are up to, but I would like to limit general access to the outside WAN so the paper printer isn't trying to phone home, or more concerning any cheap web cams!
-
Network Security - Which ports do Duets use?
Hello!
I am looking to revisit my office/workshop network. I have a subnet which I have allocated for devices like 2D printers and my Duet based machines. What IP ports will I need to allow from my computer subnet to this one? Most of my machines are Duet2 boards, with one Duet 3 running through a Raspberry Pi. I appreciate that I would need to give the Raspberry Pi system additional privileges (perhaps temporary) to access the internet for updates. Are file uploads through the webpages all handled through port 80?
Thanks!
-
RE: UK Online safety regulations
@droftarts excellent, thanks. Missed that post in my abscence.
-
RE: UK Online safety regulations
Morning all,
Been abscent for a while, but will be returning shortly as I resume work to get my Raise3D system working properly & tuned up!
I was hoping for a bit of assurance that this forum is safe from the implications of the recent UK online safety legislation due to it's moderation practices?
-
RE: CE Certification
@Tricep-terry I'm guessing that work may have been to support people that are bulk buying boards for machines they are selling commercially. If the customers (rather than duet) funded the work they may not have wanted to share it. That said, They may just have their hands full!
-
RE: CE Certification
@Tricep-terry likely stating the obvious but a CE marked board won't make the whole machine CE marked. As a community the best we could do for home brewed machines is to provide example risk assessment and mitigation documents and user manuals which can be adapted by others to suit their machines. This would result in a set of documentation that demonstrates due diligence on making a custom made machine safe for use by employees, but it would still be significant work, and only worth the MBs of storage it is written on if effort is put in.
I've got a small business spec machine that I'm now rebuilding. That could be the start of example docs if they haven't happened already in the long periods of my abscence from this forum!
Edit: I believe the best duet3D could provide with the board is a certificate of incorporation.
-
RE: OrcaSlicer 1.9.0 adds codes that breaks printer.
@Phaedrux Parsing gcode files to use M201.1 or M204 would help control acceleration on the fly. Not sure why they'd want to change max speed on the fly rather than just use feed rates?
As for variable jerk/instant speed on the fly I'm not sure there is a way to deal with this with the current gcode library?
As there are already slicers in the wild using these gcodes badly perhaps it may be easier to have new gcodes for use in config files that can't be overriden in build files?
Edit: Whats the market share of Duet equipped/reprapfirmware compatible machines like vs Prusa compatible systems now?
-
RE: Which printed materials would self extinguish?
Thanks for the comments all. I'll take a better look on Monday, little one got turfed out of nursery with a temp. Nothing serious.
-
RE: Which printed materials would self extinguish?
As a side note I am doing what I can to manage fire safety in the usual ways too. My larger system will have relay isolation of the heaters and separate isolation of the fans and other 24DC devices such as the steppers. Latter mostly so I can power up the machine for setup and simulation tasks without the fans running flat out! Most wires will be sized so that a fault current of up to the fuse rating would not cause the wires rating to be exceeded. Some degree of diagnostic coverage on the isolation circuits will be there if I have spare inputs on the Duet, but it is wired so that if there was a fault on the fan PSU it would take out the heater isolation.
-
Which printed materials would self extinguish?
A lot of my printers have PLA and PETG near high current (heat bed, 600W PSU, etc) supplies or devices.
In industry these devices may be subjected to glow wire testing to gain reasonable confidence that components near the wiring would have minimal contribution to a fire caused by a fault. From what I understand this is an attempt to prevent a fire taking hold should a component fail catastrophically (e.g. DC motors often die smokey deaths) and reducing the tendancy of a fire to spread through means such as dripping plastic.
So, what printable materials have good flame resistance, and would be likely to pass glow wire tests if they were subjected to them?
Glow wire testing:
https://www.te.com/content/dam/te-com/documents/appliances/global/glow-wire-testing-appliance-industry-white-paper.pdf -
RE: Extrusion
It also may be worth checking out "M567: Set tool mix ratios".
-
RE: Stallguard Headaches & Multiple Shorts to Vin
Does look like there is a Gates Carbon/Volt antistatic range. Guess you have to brush a rotary part at some point to to reliably ground the rotating components. Not looked in to it propoperly yet as you can tell!
-
RE: Stallguard Headaches & Multiple Shorts to Vin
@tjhinton is there continuity between the stepper body and ground? Is the negative pole of the printers power supply tied to a mains electricity protective earth?
You mentioned static on the belt as a suspected cause. I will check my steppers to see if there is continuity between the axle and the stepper body. Antistatic belts are probably available if the gates belts aren't already so, although I do note you did check for charge build up.
-
RE: Pause command working late....
@India if you want this behaviour on all builds ran on this specific machine add it to your config file. You could also add it to the custom gcode your chosen slicer puts at the beginning of a build file.
Read through the detail for M669 here:
-
RE: Powering 12V_EXT on Duet3 1.01
@droftarts cheers. Missunderstood your first message as 2A limit when using 12V derived from VIN, rather than 2A limit per output when the jumpers are set to feed V_IN to the outs.
That said I'm surprised the selector-jumpers itself doesn't limit the current more than it aparrently does.
-
RE: Powering 12V_EXT on Duet3 1.01
@droftarts it's the full fat main Duet3 board with the steppers on board. Revision 1.01. The docs say 800mA draw when using the onboard 12V supply, but it doesn't say what the individual MOSFETs are rated too if I feed the 12V side of the devices being switched from an external source. I can't see the part codes for the MOSFETs. I think the Q references are simple the components ID on the board rather than it's manufacturer part code.
-
Powering 12V_EXT on Duet3 1.01
Morning All.
The advice for the 12V rail on the Duet3 is 800mA and "small fans". The fans on the Raise3D Pro2 dual head seem to be fine for that. Two small part cooling fans and a larger fan (all axial) for the heat break coolers.
The issue is I also have an LED strip for part bed illumination and a larger (rated 400mA, main case diameter ~70mm and ~20mm wide) radial blower that I'm repurposing to blow air under the main board. I think I may be pushing my luck on the 800mA guide.
I had thought about feeding 12V to the permanent fan connector but not sure how current draw would be ballanced between the onboard and external regulator. The former is diode protected against reverse current but if supplying marginally higher voltage it could end up supplying all the current anyway.
Plan b is just to feed the posative legs of the fans from the external source and sink through the board. The MOSFETs on the curcuit diagram are labelled Q25A/Q25B. I couldn't find a spec sheet on these. What is their safe continuous - rather than peak - current draw?
-
RE: Define RC Servo as Axis?
@o_lampe Good spot. Can't see the wood for the trees after a while.
I'll be using whatever the previous F setting was. The other issue that will be choking speed a bit is it will be looking to come to a full stop before executing each change of PWM.
-
state.gpOut[].pwm returns setting / 20000?
Hello.
Currently in 3.4.6 (Installed by sudo apt-get upgrade/sudo apt-get dist-upgrade on SBC & Duet 3 setup) state.gpOut[].pwm returns a value equal to the original setting divided by 20000. It hat how it will remain? Is the divisor board dependant? Is there a more reliable way to recover the current PWM setting of a port?
Thanks!