aha ok wil do that ,thank u !
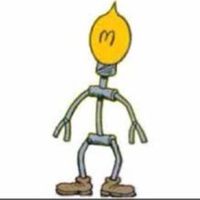
DennisD
@DennisD
Dutchy that loves to tinker but lacks of patience and is having problems reading./understanding codes
having Dyslexia so please bare with me.. its taking longer than any other tinkerer and i am sorry for that..
... ;) i try though
Best posts made by DennisD
-
RE: why is the engine speed macro 04 test
-
RE: Cr10 heatbed stays in tuning mode
ok than i will have to get me some patience i think. thank u.
Latest posts made by DennisD
-
Error: short-to-ground reported by driver(s) 3
Seems i had a short in the wiring cable to the extruder and fried the duet wifi motor chip.
lots of smoke from the board and visible damage (burn damage to the chip)but it still is putting out console messages
Error: short-to-ground reported by driver(s) 3can i use the drive 4 E1 connector for driving the extruder again?
little afraid to just switch over .
but it should be possible to remap this?thanks
-
RE: error regarding temps
@jay_s_uk
but i never seen such warning.. why does it come up now? -
error regarding temps
hi i got a question regarding this error.
Warning: Heater 1 appears to be over-powered. If left on at full power, its temperature could reach 576C
i did the following changes to my creality cr 10 s Pro version frame.
removed old stock motherboard and inserted the duet motherboard.
used the flat cable and refitted all cables so it's still plug and play.
used a bondtech DDS with pancake stepper and E3D V6 kit.now when i start the printer. its working but i get a error
i did a pid tune and inserted the outcome in the config.gbut i think i made more errors so thats why i put in the config i have.. hope u can see more errors
and help me a bit with them please. .; Configuration file for Duet WiFi (firmware version 3) ; executed by the firmware on start-up ; ; generated by RepRapFirmware Configuration Tool v3.2.3 on Wed Jul 28 2021 18:02:58 GMT+0200 (Midden-Europese zomertijd) ; General preferences G90 ; send absolute coordinates... M83 ; ...but relative extruder moves M550 P"Duet-Wifi-CR10SPRo" ; set printer name M918 P1 E4 F2000000 ; configure direct-connect display ; Network M552 S1 ; enable network M586 P0 S1 ; enable HTTP M586 P1 S0 ; disable FTP M586 P2 S0 ; disable Telnet ; Drives M569 P0 S0 ; physical drive 0 goes backwards M569 P1 S0 ; physical drive 1 goes backwards M569 P2 S0 ; physical drive 2 goes backwards M569 P3 S0 ; physical drive 3 goes backwards M584 X0 Y1 Z2 E3 ; set drive mapping M350 X16 Y16 Z16 E16 I1 ; configure microstepping with interpolation M92 X80.00 Y80.00 Z400.00 E415 ; set steps per mm M566 X1200.00 Y1200.00 Z24.00 E300.00 ; set maximum instantaneous speed changes (mm/min) M203 X9000.00 Y9000.00 Z180.00 E6000.00 ; set maximum speeds (mm/min) M201 X500.00 Y500.00 Z100.00 E5000.00 ; set accelerations (mm/s^2) M906 X900 Y900 Z900 E600 I50 ; set motor currents (mA) and motor idle factor in per cent M84 S30 ; Set idle timeout ; Axis Limits M208 X0 Y0 Z0 S1 ; set axis minima M208 X300 Y300 Z260 S0 ; set axis maxima ; Endstops M574 X1 S1 P"xstop" ; configure active-high endstop for low end on X via pin xstop M574 Y1 S1 P"ystop" ; configure active-high endstop for low end on Y via pin ystop M574 Z1 S1 P"zstop" ; configure active-high endstop for low end on Z via pin zstop ; Z-Probe ;M558 P0 H5 F120 T6000 ; disable Z probe but set dive height, probe speed and travel speed ;M557 X15:215 Y15:195 S20 ; define mesh grid ; Heaters M308 S0 P"bedtemp" Y"thermistor" T100000 B3950 ; configure sensor 0 as PT1000 on pin bedtemp M950 H0 C"bedheat" T0 ; create bed heater output on bedheat and map it to sensor 0 M307 H0 R0.405 C736.635:736.635 D7.91 S1.00 V24.2 B0 M307 H1 R1.864 C159.2 D8.88 S1.00 V24.1 M140 H0 ; map heated bed to heater 0 M143 H0 S60 ; set temperature limit for heater 0 to 60C M308 S1 P"e0temp" Y"thermistor" T100000 B4725 C7.06e-8 ; configure sensor 1 as thermistor on pin e1temp M950 H1 C"e0heat" T1 ; create nozzle heater output on e0heat and map it to sensor 1 M307 H1 B0 S1.00 ; disable bang-bang mode for heater and set PWM limit M143 H1 S260 ; set temperature limit for heater 1 to 260C ; Fans M950 F0 C"fan0" Q500 ; create fan 0 on pin fan0 and set its frequency M106 P0 S0 H-1 ; set fan 0 value. Thermostatic control is turned off M950 F1 C"fan1" Q500 ; create fan 1 on pin fan1 and set its frequency M106 P1 S1 H1 T45 ; set fan 1 value. Thermostatic control is turned on M950 F2 C"fan2" Q500 ; create fan 2 on pin fan2 and set its frequency M106 P2 S1 H1:0 T45 ; set fan 2 value. Thermostatic control is turned on ; Tools M563 P0 D0 H1 F0 ; define tool 0 G10 P0 X0 Y0 Z0 ; set tool 0 axis offsets G10 P0 R0 S0 ; set initial tool 0 active and standby temperatures to 0C T0 ; Custom settings are not defined ; Miscellaneous M575 P1 S1 B57600 ; enable support for PanelDue M501 ; load saved parameters from non-volatile memory
config.override
; config-override.g file generated in response to M500 at 2023-01-21 19:30 ; This is a system-generated file - do not edit ; Heater model parameters M307 H0 R0.405 C736.635:736.635 D7.91 S1.00 V24.2 B0 M307 H1 R1.864 C159.2 D8.88 S1.00 V24.1 ; Workplace coordinates G10 L2 P1 X0.00 Y0.00 Z0.00 G10 L2 P2 X0.00 Y0.00 Z0.00 G10 L2 P3 X0.00 Y0.00 Z0.00 G10 L2 P4 X0.00 Y0.00 Z0.00 G10 L2 P5 X0.00 Y0.00 Z0.00 G10 L2 P6 X0.00 Y0.00 Z0.00 G10 L2 P7 X0.00 Y0.00 Z0.00 G10 L2 P8 X0.00 Y0.00 Z0.00 G10 L2 P9 X0.00 Y0.00 Z0.00 M486 S-1
homeall.g
; called to home all axes ; ; generated by RepRapFirmware Configuration Tool v3.2.3 on Wed Jul 28 2021 18:02:58 GMT+0200 (Midden-Europese zomertijd) G91 ; relative positioning G1 H2 Z5 F6000 ; lift Z relative to current position G1 H1 X-305 Y-305 F3000 ; move quickly to X and Y axis endstops and stop there (first pass) G1 H2 X5 Y5 F6000 ; go back a few mm G1 H1 X-305 Y-305 F240 ; move slowly to X and Y axis endstops once more (second pass) G1 H1 Z-265 F240 ; move Z down stopping at the endstop G90 ; absolute positioning G92 Z0 ; set Z position to axis minimum (you may want to adjust this) ; Uncomment the following lines to lift Z after probing ;G91 ; relative positioning ;G1 Z5 F100 ; lift Z relative to current position ;G90 ; absolute positioning
start.g
T0M92 E415; set new E-step value for Bondtech BMG Extruder
homex.g
; called to home the X axis ; ; generated by RepRapFirmware Configuration Tool v3.2.3 on Wed Jul 28 2021 18:02:58 GMT+0200 (Midden-Europese zomertijd) G91 ; relative positioning G1 H2 Z5 F6000 ; lift Z relative to current position G1 H1 X-305 F3000 ; move quickly to X axis endstop and stop there (first pass) G1 H2 X5 F6000 ; go back a few mm G1 H1 X-305 F240 ; move slowly to X axis endstop once more (second pass) G1 H2 Z-5 F6000 ; lower Z again G90 ; absolute positioning
homey.g
; homey.g ; called to home the Y axis ; ; generated by RepRapFirmware Configuration Tool v3.2.3 on Wed Jul 28 2021 18:02:58 GMT+0200 (Midden-Europese zomertijd) G91 ; relative positioning G1 H2 Z5 F6000 ; lift Z relative to current position G1 H1 Y-305 F3000 ; move quickly to Y axis endstop and stop there (first pass) G1 H2 Y5 F6000 ; go back a few mm G1 H1 Y-305 F240 ; move slowly to Y axis endstop once more (second pass) G1 H2 Z-5 F6000 ; lower Z again G90 ; absolute positioning
homez.g
; homez.g ; called to home the Z axis ; ; generated by RepRapFirmware Configuration Tool v3.2.3 on Wed Jul 28 2021 18:02:58 GMT+0200 (Midden-Europese zomertijd) G91 ; relative positioning G1 H2 Z5 F6000 ; lift Z relative to current position G1 H1 Z-265 F3000 ; move Z down until the endstop is triggered G92 Z0 ; set Z position to axis minimum (you may want to adjust this) ; Uncomment the following lines to lift Z after probing ;G91 ; relative positioning ;G1 Z5 F100 ; lift Z relative to current position ;G90 ; absolute positioning
-
RE: cr10s steppers with Duet2 no joy
tried it and the comment is gone. so that is solved , i used some other cables
but now if i press level x then z moves . i have managed to break it once again
can someone please help me fix the config files.i have to map the steppers but i have no idea..
i have one x stepper
one y stepperAnd two Z motors.. there connected to the dual output ports on my duet2 wifi
i also like to know what are the files on my sd card doing.i have
config-override
config.bak
config.g
what is the correct file?i want to reuse the old endstops (two wires mechanical ones)
the rest is hardware used from my older cr10 printer..
below is the config i used on the old printer but its not working although it also creality cr10
if someone can help me out, that would be appreciated a lot..code_text ; Configuration file for Duet WiFi (firmware version 3) ; executed by the firmware on start-up ; ; generated by RepRapFirmware Configuration Tool v3.2.3 on Wed Jul 28 2021 18:02:58 GMT+0200 (Midden-Europese zomertijd) ; General preferences G90 ; send absolute coordinates... M83 ; ...but relative extruder moves M550 P"Butcher" ; set printer name M918 P1 E4 F2000000 ; configure direct-connect display ; Network M552 S1 ; enable network M586 P0 S1 ; enable HTTP M586 P1 S0 ; disable FTP M586 P2 S0 ; disable Telnet ; Drives M569 P0 S0 ; physical drive 0 goes backwards M569 P1 S0 ; physical drive 1 goes backwards M569 P2 S0 ; physical drive 2 goes backwards M569 P3 S0 ; physical drive 3 goes backwards M584 X0 Y1 Z2 E3 ; set drive mapping M350 X16 Y16 Z16 E16 I1 ; configure microstepping with interpolation M92 X80.00 Y80.00 Z400.00 E400 ; set steps per mm M566 X1200.00 Y1200.00 Z24.00 E300.00 ; set maximum instantaneous speed changes (mm/min) M203 X9000.00 Y9000.00 Z180.00 E6000.00 ; set maximum speeds (mm/min) M201 X500.00 Y500.00 Z100.00 E5000.00 ; set accelerations (mm/s^2) M906 X800 Y800 Z800 E600 I50 ; set motor currents (mA) and motor idle factor in per cent M84 S30 ; Set idle timeout ; Axis Limits M208 X0 Y0 Z0 S1 ; set axis minima M208 X300 Y300 Z260 S0 ; set axis maxima ; Endstops M574 X1 S1 P"xstop" ; configure active-high endstop for low end on X via pin xstop M574 Y1 S1 P"ystop" ; configure active-high endstop for low end on Y via pin ystop M574 Z1 S1 P"zstop" ; configure active-high endstop for low end on Z via pin zstop ; Z-Probe ;M558 P0 H5 F120 T6000 ; disable Z probe but set dive height, probe speed and travel speed ;M557 X15:215 Y15:195 S20 ; define mesh grid ; Heaters M308 S0 P"bedtemp" Y"thermistor" T100000 B3950 ; configure sensor 0 as PT1000 on pin bedtemp M950 H0 C"bedheat" T0 ; create bed heater output on bedheat and map it to sensor 0 M307 H0 R0.116 C633.1 D0.47 S1.00 V11.8 ; enable bang-bang mode for the bed heater and set PWM limit M140 H0 ; map heated bed to heater 0 M143 H0 S60 ; set temperature limit for heater 0 to 60C M308 S1 P"e0temp" Y"thermistor" T100000 B4725 C7.06e-8 ; configure sensor 1 as thermistor on pin e1temp M950 H1 C"e0heat" T1 ; create nozzle heater output on e0heat and map it to sensor 1 M307 H1 B0 S1.00 ; disable bang-bang mode for heater and set PWM limit M143 H1 S260 ; set temperature limit for heater 1 to 260C ; Fans M950 F0 C"fan0" Q500 ; create fan 0 on pin fan0 and set its frequency M106 P0 S0 H-1 ; set fan 0 value. Thermostatic control is turned off M950 F1 C"fan1" Q500 ; create fan 1 on pin fan1 and set its frequency M106 P1 S1 H1 T45 ; set fan 1 value. Thermostatic control is turned on M950 F2 C"fan2" Q500 ; create fan 2 on pin fan2 and set its frequency M106 P2 S1 H1:0 T45 ; set fan 2 value. Thermostatic control is turned on ; Tools M563 P0 D0 H1 F0 ; define tool 0 G10 P0 X0 Y0 Z0 ; set tool 0 axis offsets G10 P0 R0 S0 ; set initial tool 0 active and standby temperatures to 0C T0 ; Custom settings are not defined ; Miscellaneous M575 P1 S1 B57600 ; enable support for PanelDue M501 ; load saved parameters from non-volatile memory
-
RE: cr10s steppers with Duet2 no joy
@droftarts ok thank u for responding.. when finished from work i will try it and post the outcome.. once again thank u
-
cr10s steppers with Duet2 no joy
hi all
and first of all best wishes and a healthy 2023i have a question.. i have a duet 2 wifi and i have a used printer frame. (gift because broken motherboard ) really neat looking creality sc10s pro i want to use the Duet 2 wifi that i have here.. i am totally rewiring it. inc flat cable
now the printer has standard creality cr 10s pro steppers and i have problems finding info about the steppers. and what settings to use with the online config tool.
the text on the stepper is bj42d22-23
i tried multiple versions of the online config generator but the steppers do move . but keep making weird noises and making lots of noise. and it's giving errors like A motor may be disconnected reported by driver. that error that has to do with faulty wiring .but i checked the old wiring and bought new cables with connectors but no luck, . does anyone have any clue what i am doing wrong here.. ps i am using the 24v volt to power the duet.. as far as i know this can't be the problem because the cr10s pro is stock 24volt. hope that some of u can point me in the right direction.. thanks -
RE: Z-Wobble vs temperature instability - Video
i have noticed that one also.. so if the light flash fast its pid if its slowly on and off its bang bang..
-
RE: blob related
@Argo said in blob related:
cooling fan running and at
Hi Argo
yes the fan is running the one cooling the extruder is always on.
and the other fan the one that is blowing at nozzle ison first layer to bed it is off. 0 prorcent
40 procent at second layer.
than 50 at third
and 100 at fourth layer -
blob related
hi all
got a question regarding the weird looking prints
i think its some sort of blobbing?tried other slicers also
prusaslicer
cura
and back to simplify3d
changed layerhights, temps checked the belts. did a new pidtune.. leveleld the bed again.
its after i changed some new hardware
that is Bondtech direct drive with pancake stepper and v6 hotend
i have done the following so far, pidtuning other pla spool, leveled the bed a lot.
adjust the retractings was on 6 now on 2 but no luckBoard: Duet 2 WiFi (2WiFi)
Firmware: RepRapFirmware for Duet 2 WiFi/Ethernet 3.2.2 (2021-02-11)
Duet WiFi Server Version: 1.22
hope that someone over here can help me out a bit..thank u