@cosmowave
You need something like this
https://www.amazon.co.uk/QLOUNI-Converter-3-0-40V-Adjustable-Regulator/dp/B077VW4BTY
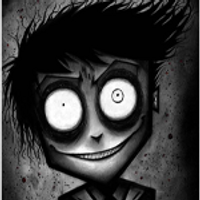
Posts made by bruce
-
RE: The ULTIMATE RepRap Post-Processor for Fusion 360
I updated the ULTIMATE post-processor for RepRap (get it here on GitHub).
With this release the backlash compensation is improved and now offers two compensation methods:- Steps: This method is preferred over the old compensation by distance method. This method compensates backlash by adjusting the Steps Per Unit and keeps motion distances as they are reported by the CAM. To use this method in this version you will need to know your current Steps Per Unit configuration. To get these configuration, open "config.g" file (normally under /sys/ folder) and note M92 X and Y and Z values. When posting your part, enter these values in the backlash compensation input as asked. (Section 4 of the post "Linear Backlash Compensation)
The post Steps Per Unit values you enter are ONLY effective if you choose "Steps" as your compensation method and check "Apply Backlash Compensation" tick box - Distance: This is the older method and still quite useful if you don't know your Steps per unit configuration, or for whatever strange reason you don't want to use Steps method.
In both methods X, Y and Z axis measured backlash for 1mm and 10mm is required for a successful compensation calculation. - Tolerance: By setting tolerance you tell the post-processor to not trigger backlash compensation for motion distances smaller that the tolerance value. When dealing with small detail this will increase the machine stability by ignoring tiny backlashes.
- Steps: This method is preferred over the old compensation by distance method. This method compensates backlash by adjusting the Steps Per Unit and keeps motion distances as they are reported by the CAM. To use this method in this version you will need to know your current Steps Per Unit configuration. To get these configuration, open "config.g" file (normally under /sys/ folder) and note M92 X and Y and Z values. When posting your part, enter these values in the backlash compensation input as asked. (Section 4 of the post "Linear Backlash Compensation)
-
RE: Firmware bundle 3.3beta2 released
Thank you for all the time and effort.
I was looking for a way to do variables and/or macro parameters in RepRap Gcode without having any idea of this work here.
I remember I googled many times only to find people said this was not possible in RepRap GCode so since last week I tried to create my own fork of your latest final release. (and it took me some time to figure out how you handled things within all those classes and back and forth functions!)
Little did know this is being done very nicely.Very useful at least for me. THANK YOU to all who contributed
-
RE: Macro for "automatic" calibration of BL Touch
@OwenD if only I knew any of these are possible in a macro before today...
-
RE: Maths in G-Code for RepRap: New M930 & M931, & #Px# values
@OwenD
In the above example we can have the probe known dimensions (P0, P1, P2) and or config,g steps (P4 and P5) saved in the file and load them at the beginning of the example macro with M931 P1, and the whole fine tuning steps can happen really quickly and accurately -
RE: Maths in G-Code for RepRap: New M930 & M931, & #Px# values
@OwenD Thank you for your comment
I mainly did this for the ability to create even smarter ‘Macros’. Another one is the ability to generate formula driven paths using G-Code only.
As a use case example:
Creating a macro to automatically set/fine tune /readjust axis steps per unit (using M92)Let’s say we need to fine tune steps per mm on X and Y (or automate it for every morning. For example to compensate for the room temperature changes)
We got a cuboid probe. The exact dimensions on each side are measured and know (L x W x H) - Let’s put the exact measurements in P0, P1, P2
We know our current step per unit in each axis from our config.g file (say X400 for the X drive and 400 steps per mm for the Y drive. Set in P3 and P4.
Now, in our macro, we probe a corner (say bottom-left) and set them in P5 and P5. Like:
M930 {X} P5
M930 {Y} P6The macro then moves to probe the opposite corner. We now have
M930 {X} P7
M930 {Y} P8
The motor/firmware ‘thinks’ that the tool has moved L mm (that is saved in P0), however, the probe shows that to reach the opposite corner we moved L+0.1 mm (+0.1 is an example error we got). So:
Actual (Measured) Movement Distance = L + 0.1 = P7 - P5
Desired Movement Distance = L = P0
Therefore 400 steps (= P3) took us 0.1 short of L
Now the macro does this and fine tunes the steps per mm for us automatically:
M930 {#P0# * #P3# / (#P7# - #P5#)} P9
M92 X#P9#
Here, M930 on the above line calculates the correct and super accurate steps needed for L mm and holds it in P9
The next M92 line sets the Steps per mm to the super accurate valueWe do similar thing for Y axis:
M930 {#P1# * #P4# / (#P8# - #P6#)} P9
M92 Y#P9#
The M92 line above sets the steps per mm for the Y axis automaticallyThis is just one example to show a use case in a macro. I hope I was able to make my use case example easy to follow
-
RE: Maths in G-Code for RepRap: New M930 & M931, & #Px# values
To whoever interested:
These 6 files are modified for this addition:(Under src/GCodes)
- GCodes.h
- GCodes.cpp
- GCodeBuffer.h
- GCodeBuffer.cpp
- GCodes2.cpp
- GCodes3.cpp
This file (and toolkit folder) added:
- src/toolkit/exprtk,hpp
-
Maths in G-Code for RepRap: New M930 & M931, & #Px# values
In my fork (this link) off of Dave's work for the RepRap firmware, I added two new M commands for in-G-Code arithmetic and mathematical calculations. I also added a general G-Code parsing feature to enable it using the result of the real-time arithmetic calculation:
I took a liberty to use an apparently empty bracket in M command numbers and created these two M commands to the firmware: M930 and M931
.
M930
M930 performs a maths expression between curly brackets ({}) and saves the results in one on the 10 memory slots called P0 to P9. If memory slots aren’t set, their default value will be 0 (zero)Example 1:
M930 { 2 * (2+1)} P0sets P0 to 6. The expression that is between the curly brackets is 2*(2+1) that is 2*(3) = 6. The result is 6 which will be saved in memory slot 0 because of P0 parameter given in the M930 command line
Using X or Y or Z in the expression copies the current position in the expression and uses the position as if it was a number.
Example 2:
Assume X is at 5mm (or whatever unit you are running on)M930 {2*X} P1
sets P1 to 10. Because X will be interpreted as 5.000 and the result of the expression 2*5.00 equals 10. This result is then saved in P1 memory slot to be used later.
Example 3:
M930 {X} P2 ;simply sets P2 to current X position 5 (assuming X is at 5, P2 value will be 5.000)
Px (such as P0, P1, … P9) values are accessible to other G or M commands using #Px# format (such as #P0#, #P1#, … #P9#)
Example 4:
G0 X#P0# ;Remember in Example 1 P0 was set to 6. This line will be translated as G0 X6. That is value of 6 replaced the variable name P0
Example 5:
M930 {(X * #P0#)+2} P0 ;remember in Example 1 P0 was set to 6, it is now set to be (X*6)+2. For example if X is at 5, P0 would be 32
If Px is not set, it’ll auto initialises to 0
Example 6:
G1 X#P1# Y#P2# F#P8#Assume before this line of GCode, P1 is set to be 76.23, P2 is 36.17, P8 is 400. The output of this line will be as if it was:
G1 X76.23 Y36.17 F400;If you need to make any calculation to be passed to any G command you will need to do it before that G command in a separate M930 command line.
Example 7:
M930 {X*2} P1 ; doubles the value of the current position of X axis
G1 X#P1# ; moves X axis to our newly calculated P1. Now the current X position is the changed to be P1
Assume X is at 5. The first M930 line above sets P1 to 10. The second line will be G1 X10. Therefore now the current position of X is 10 (as opposed to be 5). So the next time you do this P1 will be 20 (as opposed to 10)Similarly you can use this format #Px# (for P0 to P9) in any other G or M commands to pass your calculation results to other commands.
Example 8:
M930 {25} P0 ; #P0# is 25
M930 {100} P0 ; #P0# is now overwritten with 100 without any warningThe second M930 overwrites P0 value to 100, without giving any warning.
.
M931
M931 saves or loads all variables (P0 to P9) on SD Card in a file named: “arithmetics-memory-slots.g” that can be found under “sys” directory (/folder)
This can be useful to inspect the values, or to load them again for a later useM931 has a single parameter Pxx. P0 saves variables, P1 loads them from the file
Example 1:
M931 P0 ; this saves all P0 to P9 values into “arithmetics-memory-slots.g”Example 2:
M931 P1 ; this loads all values back to P0 to P9 when running your G-Code programme.
M930 Capabilities
M930 takes advantage of the ExprTk library that has the following capabilities:-
Mathematical operators (+, -, *, /, %, ^)
-
Trigonometry (sin, cos, tan, acos, asin, atan, atan2, cosh, cot, csc, sec, sinh, tanh, d2r, r2d, d2g, g2d, hyp)
-
Equalities & Inequalities (=, ==, <>, !=, <, <=, >, >=)
-
Assignment (:=, +=, -=, *=, /=, %=)
-
Logical operators (and, nand, nor, not, or, xor, xnor, mand, mor)
-
Functions (min, max, avg, sum, abs, ceil, floor, round, roundn, exp, log, log10, logn, pow, root, sqrt, clamp, inrange, swap)
-
And more …
I hope a few people find this useful for their projects as it is for mine. Please comment if you have any thoughts to improve this.
At this stage I only did this for my own use and obviously cannot be held responsible for whatever damages that could come out of this.
I will be pulling a request for this on GitHub to hopefully be added to an official release. I have a hard time compiling this correctly for RepRap so I hope Dave (or others) come to rescue
-
-
The ULTIMATE RepRap Post-Processor for Fusion 360
The ULTIMATE Duet3D RepRap CNC Post-Processor for Autodesk Fusion 360
Here is my take on a post-processor for Fusion 360Get it here from my GitHub
: https://github.com/BruceRoyce/UltimateRepRapPost/blob/main/UltimateRRPost.cps
This post-processor takes care of some issues and shortcomings that I found with other existing posts for RepRap, such as Linear Backlash Compensation, support for multi-tool and accurate tool change, inline probe and more
I made this for my own use, so please exercise caution if you take it! Obviously I won't be responsible for anything related to the use of this post-processor! Use own your own risk
-
RE: Backlash compensation
Backlash compensator post-processor
I appreciate this is an old topic, but that backlash on direction change was my issue no matter how much I fine tuned my 1000mmx1000mm WorkBee OX running on Duet3D RepRap, and I couldn't find an acceptable software solution. I also had a couple of issues with post-processor that were available for RepRap CNC, so I made (and will continue to improve) this Fusion 360 Ultimate Post-Processor for RepRap!
Get it here from GitHub: https://github.com/BruceRoyce/UltimateRepRapPost/blob/main/UltimateRRPost.cpsWhen posting check "Apply Backlash Compensation" on the side panel, under Linear Backlash Compensation options and input 2 measured backlash on each axis (the offset for 1mm motion on direction change and for 10mm motion on each axis. Input 0 if none, see image below) and let it take care of backlashes by adjusting movements.
This in no way is a replacement for adjusting your config.g parameters and/or tuning the hardware to the best of your capability. It's only a final resort to overcome backlash.It also takes care of manual tool change, corner or Z-probing, beeps when operator attention is required, fixes WCS issues and more.
Important note: I made this for my own use, so please exercise caution! Obviously I won't be responsible for anything related to the use of this post-processor! Use own your own risk