I just set up my Smart Effector for the first time. I have been fiddling with it since yesterday trying to get it to be as accurate as I can. Here is my setup:
Marlin 2.1.2.2
Marlin Probe Feedrate = 66mm/s fast 33mm/s for accurate probe (probe speed)
Sensitivity and programming working (flashes when I change sensitivity or reset)
Mainboard: SKR Pro V1.2 terminal accessed through Octoprint connected to the mainboard
I tried using repeatable probing and changing the speed at which the probe would tap the bed. If I set the speed of the probe slow to something like 15 mm/s, it would have more accurate probe repeatability tests, but it would "flash" twice or flicker a bit after a probe instead of one solid flash. Should I only go for one solid flash?
Setting the sensitivity high (25) would cause false triggers and failed bed probes and calibrations with slow speeds, but changing the probe speed back to 33mm/s and low sensitivity causes rather high standard deviations (I think). Here is what my tests are showing in the screenshot.
What I want to know is does the tightness of the probe matter? I have it pretty securely tightened with the plastic nut that came with the effector, and I printed a thin M12 washer where the heatsink touches the PCB because it didn't butt up to it flat without one. What should I be getting for accuracy from the probe? Is this normal (see screenshot)?
Thank you!
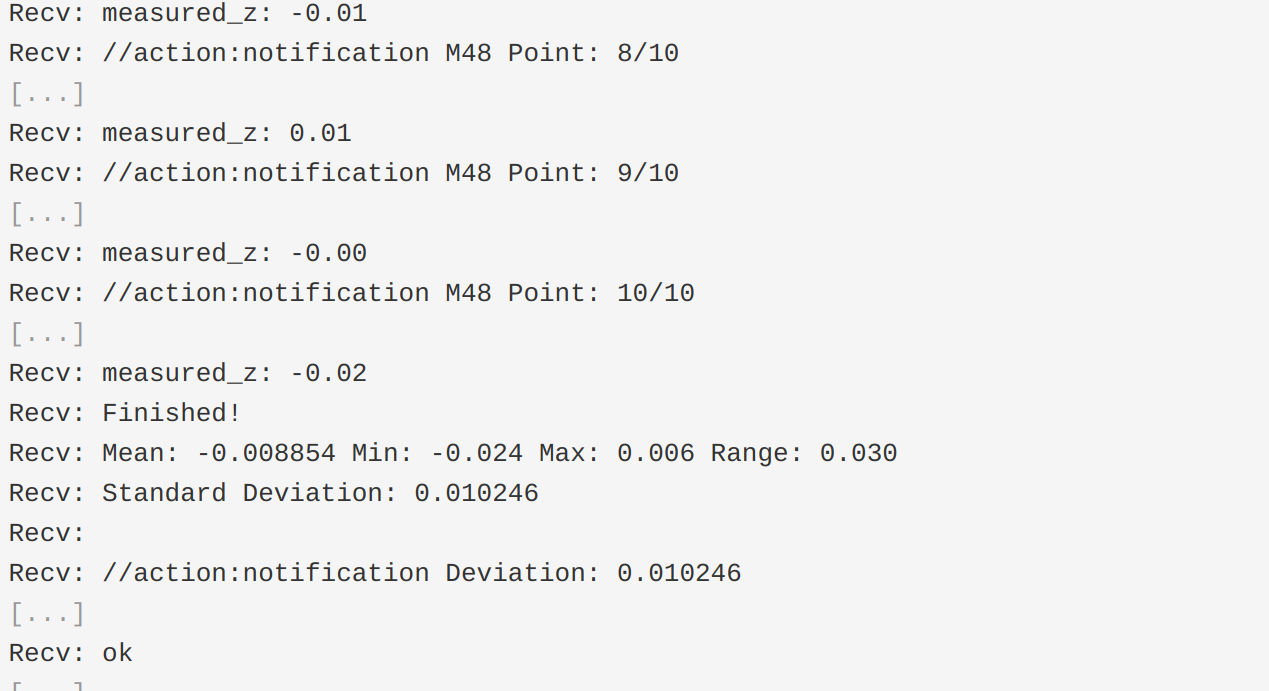
EDIT:
I had both a hot fan causing noise and my heated bed causing noise. I replaced the hot end fan with a few different ones and found one that doesn't interfere and I raised my probe height and added a delay to not be affected by the heated bed. After a bed level, it started printing about 3mm off the bed. I don't get why it is acting up so much for me.