@deckingman The hole is only 3mm. I think the misshapenness is just where the seam is. I have set the steps/mm as perfectly as I can with calipers measuring 100mm. My magnetic filament monitor which has been previously carefully calibrated also confirms my min/max extrusion is 98% to 102%. The extrusion factor I'm using in slicer is 98%, which for me has always given my a good compromise between quality and strength.
I ran a test with 3 test parts at 90%, 80% and 70% extrusion rate.
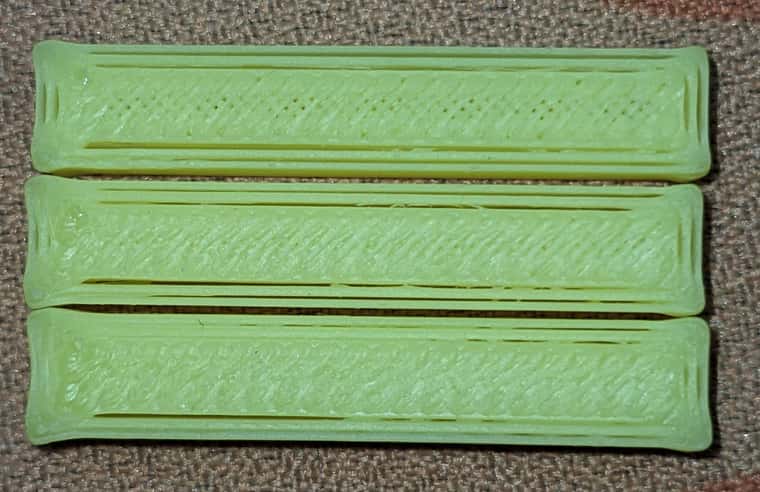
Despite underextruding a lot, the corner bulges are still there unfortunately.
The temperature sensor is a PT1000 and it is configured as a PT1000 in my config. My old sensor was also a PT1000, so I didn't have to change that in my config. The filament always behaves as I would expect it to at given temperatures, and when I start up from cold, the 3 temperature sensors in the printer all show the same temperature within 1-2 degrees (the other 2 are thermistors).
This is a benchy I printed in 20-25 minutes a few days ago on this setup.
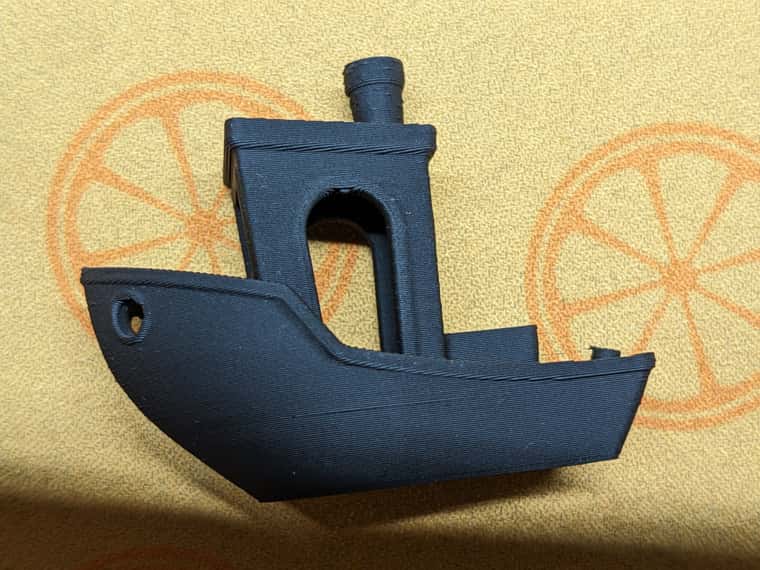
It looks pretty much flawless to me apart from the chimney having blobs on it, which was a problem I had with 3.5.0rc-1, (I've now gone back to 3.4.6) and the hull line. Which is just due to not having enough control in SuperSlicer or Orca to stop the fan from cooling as much on that layer, when the deck starts printing, without causing problems with cooling elsewhere. But there is no sign of overextrusion or high temperatures.
So I don't think there are any problems with my slicer settings or my config. Everything is now dialed in very well and the only problem I'm getting is the bulges on sharp corners. The benchy doesn't show up this issue because all corners are rounded.