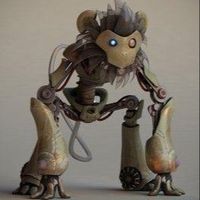
Posts made by QuentinLe
-
integrate an Infrared contact-less pyrometer
Hello ,
For one of our special project we are trying to integrate an Infrared contact-less pyrometer or temperature sensor.
We are trying to measure a substrate that should vary between 15°C and 150°C and for this the pyrometre should be capable of reading let's say from -50°C to 300°C.
+/-2°C precision is not a big issue for us.We are using a Duet3D 6HC main board. No daughter boards and we would like to avoid adding a board just for this.
Many type of sensors exist with different output possibilities:
UART
I2C
Analog voltage (mainly 0-5V or 0-10V)
4-20mA (Current loop)
Thermocouple type output for some (K/J)I undestand this topic has been treated before
https://forum.duet3d.com/topic/29639/contact-less-infrared-temperature-sensor-mlx90614
https://forum.duet3d.com/topic/28845/pir-pyrometer-sensor-as-temperature-sensor-for-liquid/6?=1680777925024
https://forum.duet3d.com/topic/7681/i2c-pyrometer-module-as-temperature-sensor/4?=1680854551896
But those are old now and I believe some updates have been integrated to Duet since.Under sensor type for M308 command we can now find the following.
"thermistor", "pt1000", "rtd-max31865", "thermocouple-max31855", "thermocouple-max31856", "linear-analog", "dht21", "dht22", "dht-humidity", "bme280", "bme-pressure", "bme-humidity", "current-loop-pyro", "drivers", "mcu-temp"1- would a 4-20mA output capable sensor work with "current-loop-pyro"? Where should we connect it? to tempx connectors? any polarities to respect?
2- If we go with an analog output sensor, what should we chose, 0-5V or 0-10V or even 0-50V, and why? How would the ADC know the "full scale" (sorry for my little knowledge in electronics)
3- I have read that I/O1 and I/O2 are now UART capable, we have no panel due but endstops connected there. Can you explain to us the correct way of cabling and programing a sensor there if we chose to go with an UART one?
4- what are your recommendations in terms of reliability, which type of sensors are more prone to noise...Your help and clarifications are appreciated.
Some sensors we are thinking about:
https://docs.rs-online.com/1fd1/A700000008530366.pdf
https://docs.rs-online.com/cb45/0900766b81344af0.pdf -
Spindle brushed DC + Encoder
Hello there,
I'm trying to control a pololu #4691 brushed DC motor with a 6HC board ( pololu has an integrated encoder - rpm sensor)
The motor comes with 6 wires:
2 wires (red and black) to power the motor
2 wires to power the encoder
2 wires to read the taco.I thought connecting it like a 4 wires fan would make it work, but apparently not.
I activated CNC mode, and only connect DC power wires to OUT7 (24V) but only M3 is working but not M4 nor M5 (not able to turn off motor when it start running)
I also have a pololu H bridge #2999, is it necessary?
On the long run we would be happy to be able to control the motor in a closed loop fashion with RPM speed as input and not PWM...
Your help would be appreciated
-
RE: Possible to add unique ID to 1LC or modify Name
@dc42 said in Possible to add unique ID to 1LC or modify Name:
M122 B# P1
Thanks for your reply => M122 B# P1 working like a charm in my case
-
RE: Possible to add unique ID to 1LC or modify Name
@t3p3tony
It is good to know that there is an unique ID in the board. You can find below the M122 B20 console answer:Diagnostics for board 20: Duet TOOL1LC firmware version 3.3 (2021-06-15 16:12:58) Bootloader ID: not available Never used RAM 3604, free system stack 2762 words Tasks: Move(notifyWait,1.3%,147) HEAT(delaying,124.7%,107) CanAsync(notifyWait,0.0%,61) CanRecv(notifyWait,16.0%,76) CanClock(notifyWait,12.8%,65) TMC(delaying,1943.7%,57) MAIN(running,3696.1%,352) IDLE(ready,0.0%,41) AIN(delaying,3334.0%,142), total 9128.6% Last reset 23:53:46 ago, cause: power up Last software reset data not available Driver 0: position 0, 335.4 steps/mm, standstill, SG min/max 0/0, read errors 0, write errors 0, ifcnt 11, reads 21464, writes 11, timeouts 0, DMA errors 0, steps req 0 done 0 Moves scheduled 0, completed 0, in progress 0, hiccups 0, step errors 0, maxPrep 0, maxOverdue 0, maxInc 0, mcErrs 0, gcmErrs 0 Peak sync jitter -2/4, peak Rx sync delay 219, resyncs 0/0, no step interrupt scheduled VIN: 24.2V MCU temperature: min 37.2C, current 54.4C, max 55.9C Ticks since heat task active 213, ADC conversions started 85682667, completed 85682666, timed out 0, errs 0 Last sensors broadcast 0x00000001 found 1 218 ticks ago, loop time 0 CAN messages queued 1032430, send timeouts 0, received 1118443, lost 0, free buffers 37, min 37, error reg 100000 dup 0, oos 0/0/0/0, bm 0, wbm 0, rxMotionDelay 0 Accelerometer detected: no I2C bus errors 4619, naks 4619, other errors 4619
So, on the 3.3 version, the unique ID is not reported.
The field "uniqueId" in the object model (under boards) returns "null", so nothing there either apparently.
In case it is an important information, I am running on SBC mode.
-
RE: Possible to add unique ID to 1LC or modify Name
Hello droftarts thanks for you reply.
I already know for the can adresse but it not working on my case. I have multiple machines with different main board and I would like to recognise tool between machine so I need unique variable and store in the 1LC like the unique id on the 6HC.
I don't Know if it's possible but I can see the field uniqueID on board so I think so.Quentin
-
Possible to add unique ID to 1LC or modify Name
Hello,
I needs to attribute a unique id to my 1LC board but i don't find anything about this. I have searched on gcode list and on reprap firmware and i saw nothing about this.
But i can see that field exist on ObjectModel => Board.
I would like to know if you have any solutions to set this variable and if is not it's possible did you have a solution to change an other variable like Name or ShortName.Thanks by advanced.