Hello,
I am helpless after building more than 12 printers by myself, but now
I have converted and Ender 3 with a Duet Wi-Fi board and linear guides,
and the print result are the worst and inconsistent of all my linear conversions incl. Two Tree Saphire s and Pro
What do I get, and have now idea why this happens:
See attached pictures for better understanding.
- Inconsistent layer lines seems that extrusion changes around the perimeters changing from the bottom to the top
- one mayor layer shift at 10 cm
- Massive and worse ghosting ever seen on my prints
- Print settings same as on other printers is way higher nearly double of other printer
I have checked all the parameters that could come into consideration:
- all cables are attached properly no wiggle
- All belts are properly tensioned with metal spanners
- every single linear rail slider was cleaned, greased, and checked of smooth running before assembling and after assembling with tensioned belts on. There is now stick and slip or other factor that could lead to not running smooth in any position of xyz.
- nozzle and cooling system are attached perfectly tight and with no clearance or wiggle noticeable.
-I don’t understand the massive difference in print time. in Prusa slicer the only thing I changed was the printer tab all other parameters remained the same. The only difference is pressure advance, but can this lead to so much dramatic higher print times?
From all my prints it should lead to the best print result, but it doesn’t, and a don’t have any idea any more what could cause the inconsistent and bad print result in any discipline .
Last for the setup the extruder is a all metall with dual hobbet gears that should produce nice and consistant layer lines all over
In the following I will post pictures of the print results and the config.g that was used to print the part
      
I set the motor current to 800 as I found in the guide somewhere here set as default.
If I take higher values the motors sound very agressive and my fear was that this would cause wiggling arefacts on the surface. What are your defaults.
Here no my config.g
; Configuration file for Duet WiFi (firmware version 3)
; executed by the firmware on start-up
;
; generated by RepRapFirmware Configuration Tool v3.1.9 on Sat Nov 28 2020 19:48:11 GMT+0100 (Mitteleuropäische Normalzeit)
; General preferences
G90 ; send absolute coordinates...
M83 ; ...but relative extruder moves
M550 P"Ender3ProDuetWifi" ; set printer name
; Network
M552 S1 ; enable network
M586 P0 S1 ; enable HTTP
M586 P1 S0 ; disable FTP
M586 P2 S0 ; disable Telnet
; Drives
M569 P0 S1 ; physical drive 0 goes forwards
M569 P1 S1 ; physical drive 1 goes forwards
M569 P2 S1 ; physical drive 2 goes forwards
M569 P3 S0 ; 3dp Extruder reverse physical drive 3 goes backward
M584 X0 Y1 Z2 E3 ; set drive mapping
M350 X16 Y16 Z16 E16 I1 ; configure microstepping with interpolation
M92 X80.00 Y80.00 Z400.00 E131.00 ; set steps per mm E Basis 95
M566 X900.00 Y900.00 Z60.00 E120.00 ; set maximum instantaneous speed changes (mm/min)
M203 X6000.00 Y6000.00 Z300.00 E1200.00 ; set maximum speeds (mm/min)
M201 X500.00 Y500.00 Z20.00 E250.00 ; set accelerations (mm/s^2)
M906 X800 Y800 Z800 E800 I30 ; set motor currents (mA) and motor idle factor in per cent
M84 S30 ; Set idle timeout
; Axis Limits
M208 X0 Y0 Z0 S1 ; set axis minima
M208 X235 Y230 Z250 S0 ; set axis maxima
; Endstops
M574 X1 S1 P"xstop" ; configure active-high endstop for low end on X via pin xstop
M574 Y1 S1 P"ystop" ; configure active-high endstop for low end on Y via pin ystop
M574 Z1 S2 ; configure active-high endstop for low end on Z via BLTouch
;M574 Z1 S1 P"zstop" ; org configure active-high endstop for low end on Z via pin zstop
; Z-Probe Achtung Reprap V3!
M558 P9 C"^zprobe.in" H5 F120 T6000 ; Set Z probe type to bltouch and the dive height + speeds
M950 S0 C"exp.heater7"
G31 P500 X-40 Y-12 Z1.60 ; Set Z probe trigger value, offset and trigger height je gGROESSER desto NAEHER DRAN
M557 X35:235 Y35:200 S40 ; Define mesh grid S40 bedeutet die Grid-Messpunkte sind 40mm voneinenander entfernt
M671 X35:200:200:35 Y200:200:35:35 P0.5 ; point1 (35,200), point2 (200,200), point3 (200,35), point4 (35,35)
; Heaters
;M308 S0 P"bedtemp" Y"thermistor" T107600 B4183 R4700 ; configure sensor 0 as thermistor on pin bedtemp
;M308 S0 P"bedtemp" Y"thermistor" T100000 B4138 ; configure sensor 0 as thermistor on pin bedtemp
M308 S0 P"bedtemp" Y"thermistor" T100000 B3950 ; Umbau Silikonheizbett NTC 3950 100kOhm configure sensor 0 as thermistor on pin bedtemp
M950 H0 C"bedheat" T0 ; create bed heater output on bedheat and map it to sensor 0
;M307 H0 B0 S1.00 ; diable bang-bang mode for the bed heater and set PWM limit "B1 is on"
M307 H0 P558.6 I136.699 D327.8 B0 S1.00 ; diable bang-bang mode for the bed heater and set PWM limit "B1 is on"
M140 H0 ; map heated bed to heater 0
M143 H0 S135 ; set temperature limit for heater 0 to 120C
M308 S1 P"e0temp" Y"thermistor" T100000 B4138 ; configure sensor 1 as thermistor on pin e0temp
M950 H1 C"e0heat" T1 ; create nozzle heater output on e0heat and map it to sensor 1
M307 H1 B0 S1.00 ; disable bang-bang mode for heater and set PWM limit
M143 H1 S280 ; set temperature limit for heater 1 to 250C
; Fans
M950 F0 C"fan0" Q500 ; create fan 0 on pin fan0 and set its frequency
M106 P0 S0 H-1 ; set fan 0 value. Thermostatic control is turned off
M950 F1 C"fan1" Q500 ; create fan 1 on pin fan1 and set its frequency
M106 P1 S1 H1 T45 ; set fan 1 value. Thermostatic control is turned on
M950 F2 C"fan2" Q500 ; create fan 2 on pin fan2 and set its frequency
M106 P2 S1 H1 T45 ; set fan 2 value. Thermostatic control is turned on
; Tools
M563 P0 D0 H1 F0 ; define tool 0
G10 P0 X0 Y0 Z0 ; set tool 0 axis offsets
G10 P0 R0 S0 ; set initial tool 0 active and standby temperatures to 0C
; Custom settings are not defined
; Miscellaneous
M575 P1 S1 B57600 ; enable support for PanelDue
and the start gcodes of the Ender 3:
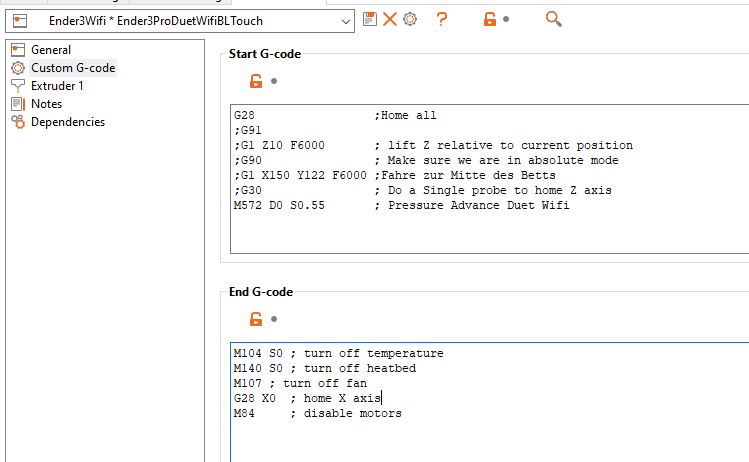
And as you can see my speed settings are, at least for my experiences low.
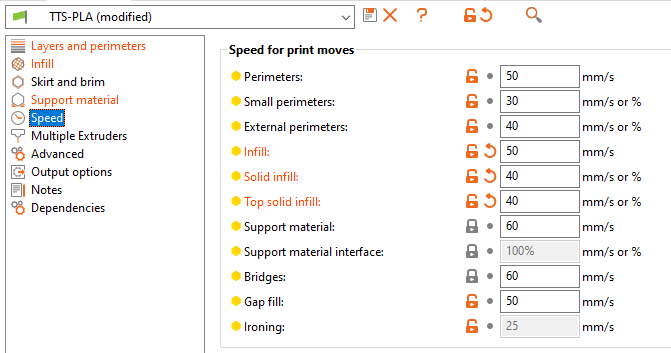
on the other machines I almost get no or hardly to see ghosting!
So, if you have the same type of machine setup and experiences better results than me please help me out with your experiences especially
and
that is why I am asking here, are there settings in the config.g wrong so it can be responsible for the different bad print results.
Thank you so much in advance
Regards