@sebkritikel excellent! Thanks. Nice to know that you can do a bit of tuning contrary to what I thought - Cheers
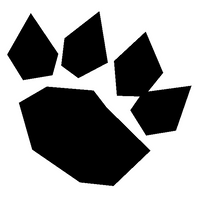
Posts made by pawPrinter
-
RE: Toolchanger Tool Prep
-
RE: Toolchanger Tool Prep
@Danal No, it just does it. So there is no control, and you are stuck with what Cura decides. I rather took it for granted until I tried out PrusaSlicer recently, and found their tool change handling not so well developed. Which is a shame because otherwise it is easier to use with multiple tools. I suppose its all still early days
-
RE: Toolchanger Tool Prep
@Danal Cura puts heating commands in the Gcode in advance of the tool change command so that the tool is up to heat by the time the change is due. The tool is parked at standby temp which can be whatever you like - off, if you prefer. I have found the timing works quite well, but I can see advantages to the firmware doing it
-
RE: Retractions are driving me crazy
I had a problem with blobs like that when I started using nozzles larger than 0.4mm. I ended up solving it by increasing my extruder speed, acceleration and jerk settings. I found that the blob was being laid down while the print head hesitated briefly as the extruder was retracting/unretracting too slowly. I suspect that using larger nozzles exposed the problem for me. Not sure if it will help you, but it is easy to try.
-
RE: Need some CoreXY advice
@gtj0 I built my CoreXY with a "twist" and I'm very pleased with how it works. I planned a belt separation arrangement, but didn't need to use it. I found that twisting the belts so that the smooth sides touched, worked without any noticeable wear or friction. I don't think it is as popular as offset belts but it works for me. Good luck with yours
-
RE: Full backup
@resam Many thanks for that tip. It has helped me a lot.
-
RE: Combine Tool Wiring
@nuverian Thanks, no prob, steal away
I can see that it is very error prone when wiring it up, so do take care. You may also notice that my plug can be put in the wrong way around. However, more by luck than judgement, my pin arrangement is tolerant of that error, other than the fact it won't work. I marked my plug so that I never put it in the wrong way - ha ha yeah right that didn't work! You probably should contrive a way to ensure that it cannot be wrong.
-
RE: Latching magnetic tool changer
@red-sand-robot No, I've not noticed any problems with the Bondtech being affected by the magnets (which are permanent magnets in my case, not electromagnets - I found electromagnets a bit heavy).
Interestingly, I have had one occasion when a fan didn't start up properly. I didn't think much of it at the time, because fans can be annoying, but it could have been related to the magnets as @dc42 predicts. -
RE: Combine Tool Wiring
@nuverian I have used perf board quite successfully, as you have been thinking. You're right: it does allow a very compact, bespoke, solution without having to search for hours to find the right plug! Even then, I never came across that lovely cable @sonderzug suggests.
I used common header pins and dupont connectors both sides of the board so that I could plug in the whole cable one side and have separate connectors to the individual head components on the other allowing them to be changed easily. It should also work nicely with soldered wiring to your board. The perf board/header is shrouded by a small print.The blue plug in the photo is a female header in hot glue/heat shrink. A bit fiddly to make. For the heater connection I used 2 pairs of pins to carry the current. I found it best to use through hole plated proto board which gives the pins a better mechanical fixing.
-
RE: Latching magnetic tool changer
@fma Ha ha - Yeah, I know how it is!!
-
RE: Latching magnetic tool changer
@fma Thanks. Yes, your idea would make a lot of sense. I might wait to see what you do, before I re-design mine.
-
RE: Latching magnetic tool changer
Here are some more heads that I've made for my latching tool changer.
Two are water cooled: One for a standard hot end, and one to fit a volcano. It turns out that water cooling is fantastic, and much less fuss than I thought it would be.
The other head is sporting a Bondtech BMG fitted for printing flexibles. It is a bit experimental to see if the magnetic mount can take the weight. So far it has worked very well, but it's perhaps not the most elegant solution. However, it was very simple to adapt the Bondtech in this way, and I get the advantage of a well proven feeder.
When you can easily swap heads over, it starts to get very versatile, but can be a configuration nightmare!
-
RE: Latching magnetic tool changer
@fma said in Latching magnetic tool changer:
Do you have to pull hard to disconnect the magnets?
Not once the plates have been angled apart by the wedging action of the latch. There is still some pull which is easily overcome. I was surprised how far the magnet's attraction is effective, but once the plates are split they are easy to separate fully. The remaining attraction is actually helpful to keep the heads aligned properly. Obviously there is a balance between the strength of the magnets and the size/angle of the wedged latches. I found it quite easily by trial and error.
-
RE: Latching magnetic tool changer
Yeah, sorry, I have enabled link sharing now so you should be able to view without an Onshape account.
-
RE: Latching magnetic tool changer
Thanks all for the kind remarks.
@Martin1454 I've dug out some pics of my changer's latching mechanism.
I CNC'd the rather elaborate brass guides, but it turns out that they are almost completely superfluous because of the way the magnets keep the head aligned even when not fully attached. Without the guides you would just need a stop to prevent the pawl from moving above horizontal when the head is docked. The shape of the pawls could easily be filed by hand.
You can look at my cad files on Onshape if you like but they are a complete mess.
I can't take credit for the magnetic kinematic mounts. They were based partly on commercial versions used in optical systems (such as these: https://www.thorlabs.com/newgrouppage9.cfm?objectgroup_id=1546) and partly on material from an engineering book that I have which was published in 1934 and has two chapters on kinematics! It seems there is nothing new in mechanics!@1ri The sturdy frame is just aluminium angle welded together, and is a nice cheap way to make a strong frame. It probably would have been easier/better to bolt the sections together, but I had just bought a new welder that I wanted to play with
@fma Your idea sound good. Gear mechs are fun. The four heads shown in my video are unplugable, and I have just made a version which carries a Bondtech BMG extruder so that I can print flexible material. I haven't properly tested it yet, but it looks like it will work ok.
@bearer Ha ha
-
Latching magnetic tool changer
Just for interest, I've developed a latching magnetic tool changer in the style of the brilliant e3d layout. I'm not claiming that it is any better, but it is a working variation without using servos. Pins on the print head carriages run up spring loaded pawls in the docks which act to wedge apart the magnetic kinematic mounts. The pins are latched by the pawls on docking and release when the carriage is pushed in beyond the pawls for un-docking. Perhaps a bit more suited to use in a heated build chamber like mine, but it is ultimately limited by the magnet temperature ratings. Docking is reasonably tolerant of poor alignement, and makes a satisfying, or annoying, locating sound depending on your point of view
Printed prototypes worked just about ok for a short while, but it's not too difficult to make if you don't mind a bit of metalwork (apologies for the use of such bad language!) Sorry about the crummy video, but otherwise I would never get around to uploading anything.
https://youtu.be/0ARCip5CrUk -
RE: Firmware 2.03beta2 available
CoreXY working well here, along with leadscrew bed levelling and sensorless homing
-
RE: Heated Chamber PWM fan Help
@Phaedrux Thanks, I didn't think about changing the frequency. I'll give it a go.
@sonderzug no problem. You rather confirm what I thought about ac motors, so yes, probably OT unless the above does work
@NitroFreak excellent idea! -
RE: Inverting PS_ON levels
I've recently wired up one of those PSUs with an inline logic inverter, which I had from a radio control plane, connected to the PS_ON. I reckon your plan should work. The rpi will need to connect the RC+ on the PSU to ground/RC- to turn off the PSU. RC+ can float open circuit or be connected to the +5v standby to enable the PSU. The PSU labelling is confusing, but think of RC+ as the signal wire to switch, RC- as ground, and +5v as +5v. The only problem I can think of is that the standby 5v only supplies 500mA - that might not be enough to power the duet and rpi....
-
RE: Heated Chamber PWM fan Help
@sonderzug , sorry, yes, I can control the heater element with PWM, but my fan motor didn't play nicely with PWM - it just stuttered or failed to run at all. I was generalizing a bit, but my particular fan motor is a single phase induction motor and it turns out that these need speed control with a variable frequency drive or a triac circuit like a dimmer switch. Other types of oven fan motors could be more straight forward. Like you, I have a thermistor in the build chamber. +1 for Paneldue support