@deckingman I'll remove some retraction and use Z hop more aggressive, thanks for the tips! I had an enclosure for the PanelDue printing and it went well until it lifted from the bed (and was Y axis inverted)
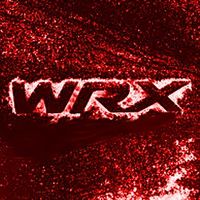
Posts made by oBezruki
-
RE: Brim prints fine, then Extruder stepper motor starts stalling
-
RE: Brim prints fine, then Extruder stepper motor starts stalling
@deckingman the print went great until the last few layers, then it appeared to clog again. I'm going to clear the jam and try a different print
-
RE: Brim prints fine, then Extruder stepper motor starts stalling
@deckingman after adjusting Z height better and adding better cooling it appears the print is going well. I have to change some speed issues but I have a solid baseline for config! Thank you!
-
RE: Brim prints fine, then Extruder stepper motor starts stalling
@owend i have yet to locate that setting
-
RE: Brim prints fine, then Extruder stepper motor starts stalling
@deckingman I believe this is causing issues yes. I'm not using auto bed leveling, so I think my bed was too close to the print head. I had to clean out the nozzle and heat break which led me to believe that it was backing up, Ive also installed a stronger heatsink fan as of now. Going to try again and will let you know
-
Brim prints fine, then Extruder stepper motor starts stalling
Hey everyone,
I just completed my RepRap conversion on my printer.
I have my extruder stepper set for the correct steps/mm (that was a good hour and a bit of my night)
I sent a test print to the printer and the brim support prints fine, but when the print gets to the actual part the extruder seems to stall/constantly skip steps. Is this an issue with my firmware? It extrudes fine when I do it manually.
I'm using Cura slicer and I will throw my Config.g below
Any help would be amazing!
Thanks,
Jake; Configuration file for Duet WiFi (firmware version 3.3)
; executed by the firmware on start-up
;
; generated by RepRapFirmware Configuration Tool v3.3.10 on Fri Jan 21 2022 22:14:04 GMT-0500 (Eastern Standard Time); General preferences
M575 P1 S1 B57600 ; enable support for PanelDue
G90 ; send absolute coordinates...
M83 ; ...but relative extruder moves
M550 P"Cube Pro Duo" ; set printer name; Network
M552 S1 ; enable network
M586 P0 S1 ; enable HTTP
M586 P1 S0 ; disable FTP
M586 P2 S0 ; disable Telnet; Drives
M569 P0 S1 ; physical drive 0 goes forwards
M569 P1 S1 ; physical drive 1 goes forwards
M569 P2 S0 ; physical drive 2 goes backwards
M569 P3 S0 ; physical drive 3 goes backwards
M584 X0 Y1 Z2 E3 ; set drive mapping
M350 X16 Y16 Z16 I0 ; configure microstepping without interpolation
M350 I1 ; configure microstepping with interpolation
M92 X87.90 Y87.90 Z1066.67 E82.89 ; set steps per mm
M566 X8500.00 Y8500.00 Z12.00 E1000 ; set maximum instantaneous speed changes (mm/min)
M203 X4000.00 Y4000.00 Z1200.00 E1800.00 ; set maximum speeds (mm/min)
M201 X500.00 Y500.00 Z250.00 E500.00 ; set accelerations (mm/s^2)
M906 X800 Y800 Z800 E800 I30 ; set motor currents (mA) and motor idle factor in per cent
M84 S30 ; Set idle timeout; Axis Limits
M208 X0 Y-30 Z0 S1 ; set axis minima
M208 X280 Y290 Z190 S0 ; set axis maxima; Endstops
M574 X1 S1 P"!xstop" ; configure switch-type (e.g. microswitch) endstop for low end on X via pin !xstop
M574 Y1 S1 P"!ystop" ; configure switch-type (e.g. microswitch) endstop for low end on Y via pin !ystop
M574 Z1 S1 P"!zstop" ; configure switch-type (e.g. microswitch) endstop for low end on Z via pin !zstop; Z-Probe
M558 P0 H5 F0 T6000 ; disable Z probe but set dive height, probe speed and travel speed
M557 X15:215 Y15:195 S20 ; define mesh grid; Heaters
M140 H-1 ; disable heated bed (overrides default heater mapping)
M308 S0 P"bedtemp" Y"thermistor" T100000 B4138 ; configure sensor 0 as thermistor on pin bedtemp
M950 H0 C"bedheat" T0 ; create chamber heater output on bedheat and map it to sensor 0
M307 H0 B0 S1.00 ; disable bang-bang mode for the chamber heater and set PWM limit
M141 H0 ; map chamber to heater 0
M143 H0 S300 ; set temperature limit for heater 0 to 300C
M308 S1 P"e1temp" Y"thermistor" T100000 B4138 ; configure sensor 1 as thermistor on pin e1temp
M950 H1 C"e1heat" T1 ; create nozzle heater output on e1heat and map it to sensor 1
M307 H1 B0 S1.00 ; disable bang-bang mode for heater and set PWM limit
M143 H1 S280 ; set temperature limit for heater 1 to 280C; Fans
M950 F0 C"fan0" Q500 ; create fan 0 on pin fan0 and set its frequency
M106 P0 S1 H-1 ; set fan 0 value. Thermostatic control is turned off
M950 F1 C"fan1" Q500 ; create fan 1 on pin fan1 and set its frequency
M106 P1 S1 H-1 T45 ; set fan 1 value. Thermostatic control is turned on; Tools
M563 P0 S"Extruder 1" D0 H1 F1:0 ; define tool 0
G10 P0 X0 Y0 Z0 ; set tool 0 axis offsets
G10 P0 R0 S0 ; set initial tool 0 active and standby temperatures to 0C; Custom settings are not defined
; Miscellaneous
M911 S10 R11 P"M913 X0 Y0 G91 M83 G1 Z3 E-5 F1000" ; set voltage thresholds and actions to run on power loss
T0 ; select first tool