Hi,
I've got an Ender-6 with stock Creality 4.3.1 mainboard running Klipper off a raspberry pi 3b+, with a Biqu H2 V2S extruder and a clone of @dc42 's IR differential height sensor.
My printer isn't running a Duet or any related hardware except the IR height sensor, but there's so little information available elsewhere about troubleshooting the sensor that I figured I'd post here asking for any possible advice to help with the issues I'm having.
It seems to be working correctly in every way that I can tell, it's in digital mode (two LED blinks) and when probing the same place multiple times the height readings are incredibly consistent, within less than 0.01 mm.
However, when I try to actually create a mesh with it, I get a jagged, mountainous mess: 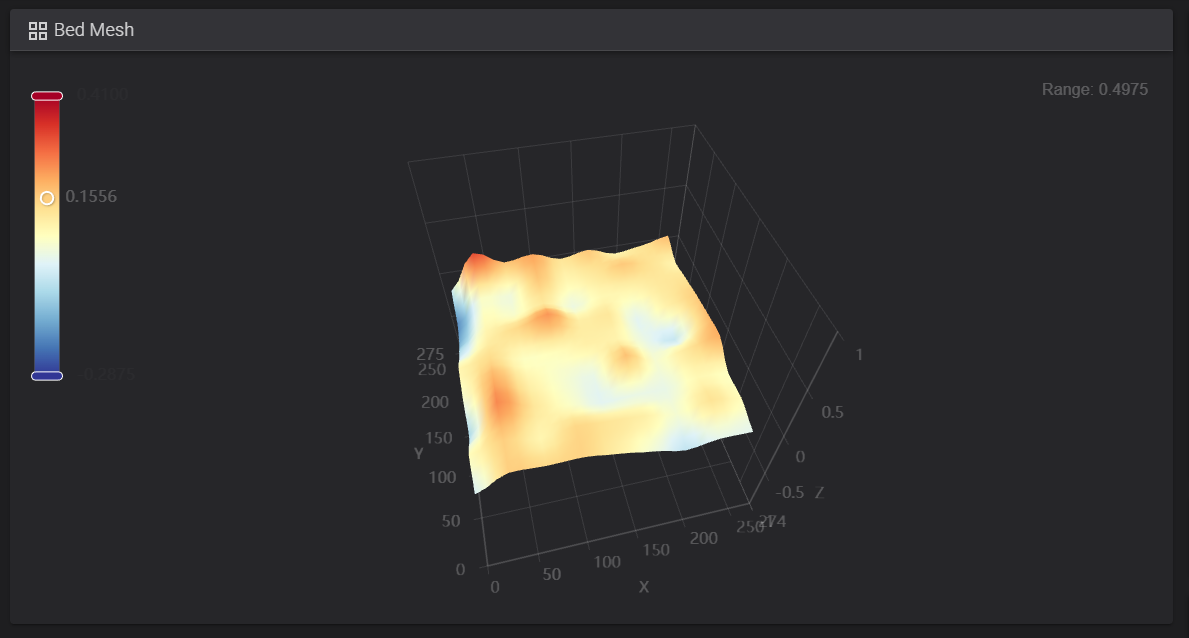
That mesh is a 9x9 with a piece of black G10 as a bed surface, 3mm/s probe speed.
Thinking it must be due to changes in reflectivity due to the imprint left by previous prints, I went over the whole bed surface with 180-grit on an orbital sander, and got a very similar result, or maybe even worse:
Thinking it may be a rigidity issue due to the mounting location, I remounted the sensor directly to the stepper motor: 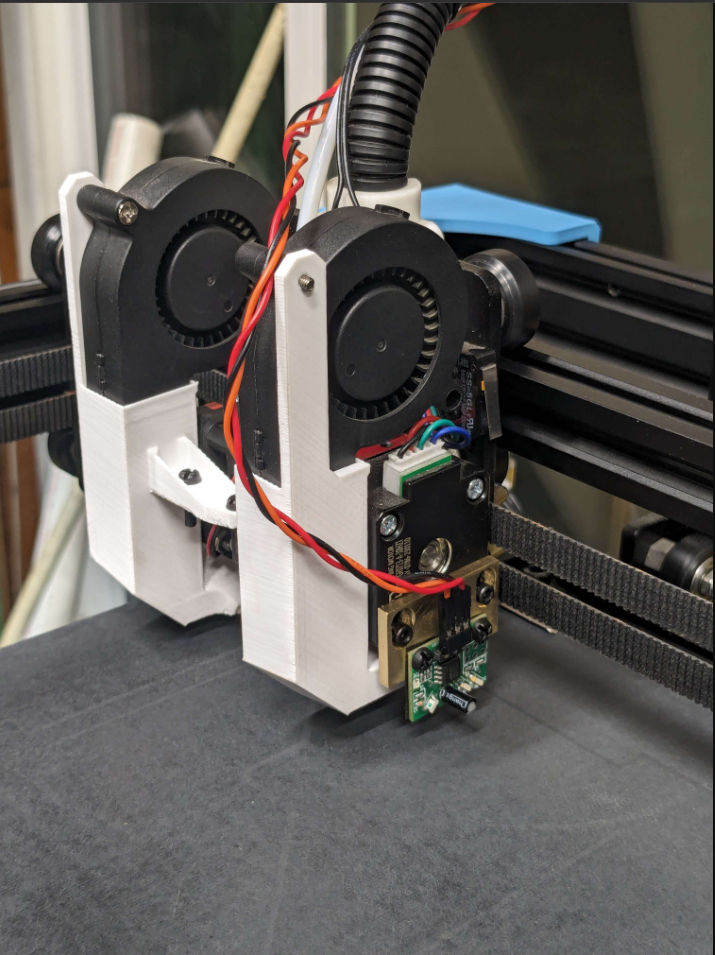
At someone else's suggestion I applied hairspray to the build plate in an attempt to give it an even more uniform surface: 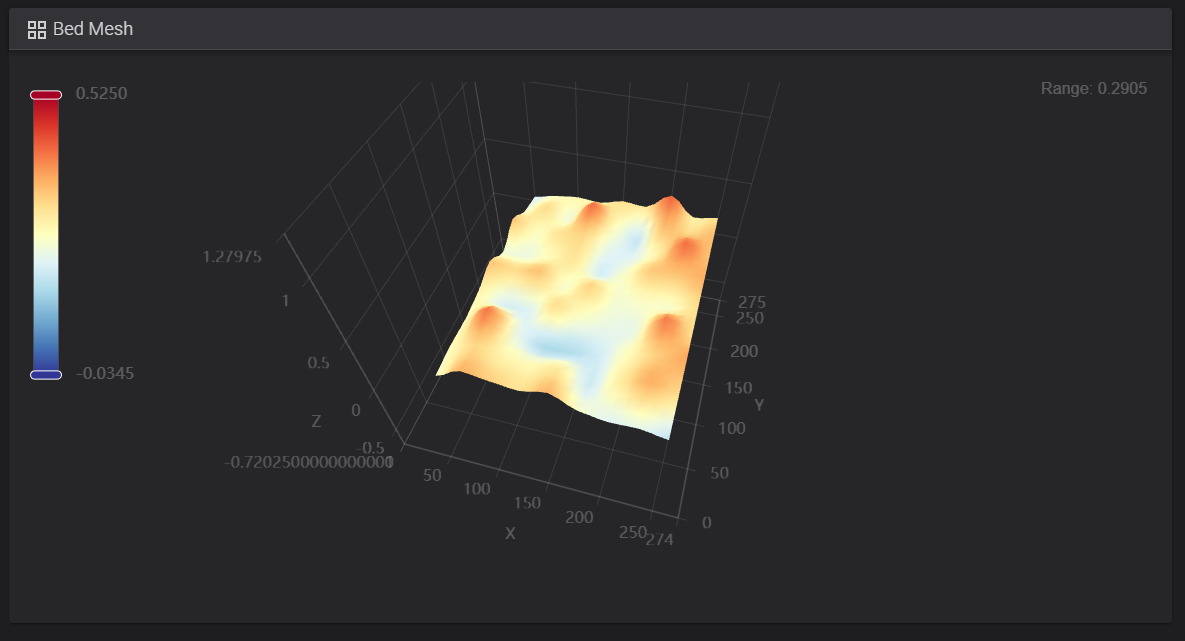
In desperation, I did a 20x20 point grid with 5x averaging on every point, only to see this monstrosity: 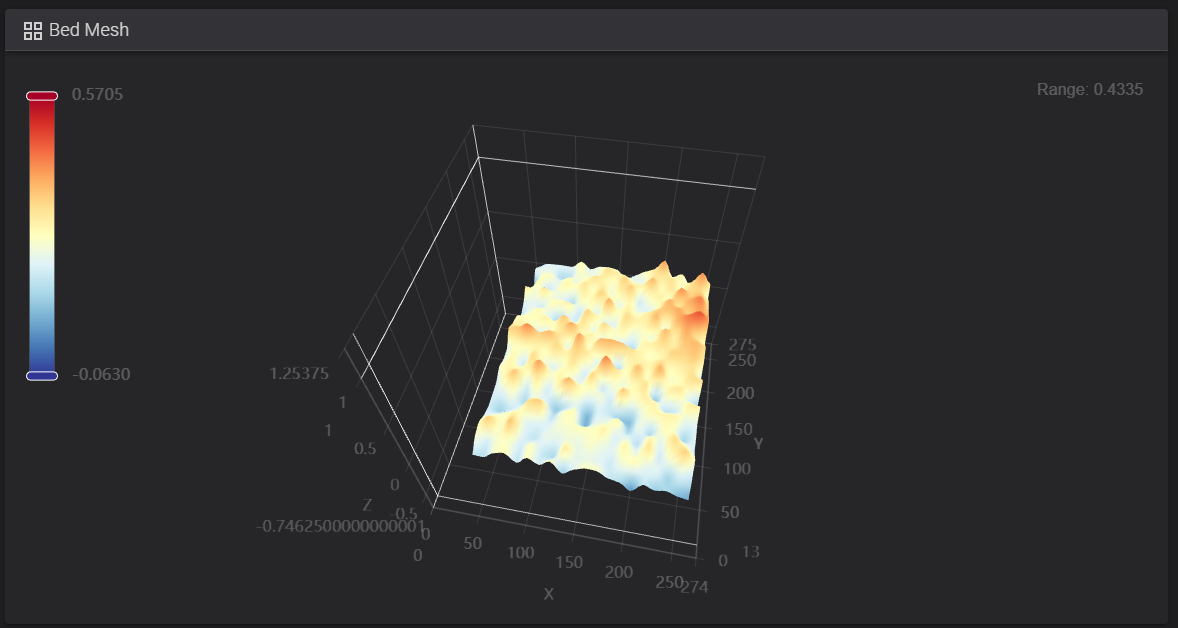
Somebody please help, I feel like I'm just running in circles at this point.