@infiniteloop @droftarts It was the fan miniblade fuse! Should've checked this sooner but haven't blown many fuses yet, lesson learned. I had even swapped my Duet 2 wifi with another at a point so I thought no way both have a blown fuse....sure enough they both did. I think it was long before I was setting up this machine as the electromagnet has less than 1A draw on 12V, but I'll be double checking
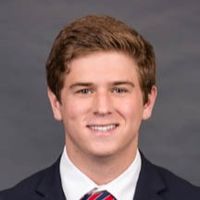
Posts made by JRCL
-
RE: Duet 2 Wifi Fan Issues
-
Duet 2 Wifi Fan Issues
Trying to use the fan ports on a Duet 2 wifi to control a 12V electromagnet. I have the fan jumper on the VIN selection and the board is powered at 12V. However, my always-on fans (just as a check) never turn on and I can't turn on the fan0 with M42 either. I checked both sets of pins with a multimeter and didn't get much of a reading, but unsure if you can given the PWM signal (though I thought I had before). M98 on my config yields no issues either. Any help is appreciated
; General preferences G90 ; send absolute coordinates... M83 ; ...but relative extruder moves M550 P"FSR Test Bench" ; set printer name ; Network M552 S1 ; enable network M586 P0 S1 ; enable HTTP M586 P1 S0 ; disable FTP M586 P2 S0 ; disable Telnet ; Drives M569 P0 S1 ; physical drive 0 goes reverse M569 P1 S0 ; physical drive 1 goes forward M584 X0:1 ; set drive mapping M350 X16 I1 ; configure microstepping with interpolation M92 X80.0 ; set steps per mm M906 X1000 I30 ; set motor currents (mA) and motor idle factor in per cent M84 S30 ; set idle timeout ; Axis Limits M208 X0 S1 ; set axis minima M208 X267 S0 ; set axis maxima ; EndStop M574 X1 S3 ; X endstop on low end with sensorless homing M915 X R0 F0 ;Relays M950 F0 C"fan0" Q500 ;tray electromagnets M106 P0 S1 H-1
-
RE: BL Touch Deploying but Always Triggered
@droftarts this was what I needed! I had been using the table above that, that says PCB Pinout, but I'm now realizing it's for the BL Touch's pins not the boards. Thanks!
-
RE: BL Touch Deploying but Always Triggered
@mikeabuilder it did live in a cable chain for a while but since troubleshooting and the rewire its been removed and still seems to have the issue
-
RE: BL Touch Deploying but Always Triggered
@Phaedrux yes the self test upon startup is working fine, which is the first time I've seen that working but holding a triggered state in DWC. It is wired like so to my MB6HC:
By servo commands do you mean just sending M42 or M280 commands to try and get it to go manually? If so I haven't tried those yet and will give that a go next
-
RE: BL Touch Deploying but Always Triggered
@zBeeble Unfortunately I tried a full rewire and different set of pins before posting this
-
BL Touch Deploying but Always Triggered
My BL Touch deploys correctly upon turning on my machine but doesn't respond to M401 or M402. The Z-Probe signal in my DWC seems to always show it as triggered so when I try to test dynamically it ofc triggers immediately. I seem to have it wired correctly so I believe something in my config.g is wrong. Just looking for a second set of eyes to see if anything sticks out in my config.g or where else to look. Thanks in advance!
; Enable network G4 S5 ;wait for board to start if {network.interfaces[0].type = "ethernet"} M552 P192.168.1.14 S1 else M552 S1 ;General Prefrences G90 ;send absolute coordinates... M83 ;...but relative extruder moves M586 P0 S1 ; enable HTTP M586 P1 S0 ; disable FTP M586 P2 S1 ; enable Telnet M586 C"*" M550 P"RL1 V3" ;set printer name M669 K1 ;switch to CoreXY mode ; Drives M569 P0.0 S1 ;X motor runs M569 P0.1 S0 ;Y motor runs M569 P0.2 S1 ;Z1 motor runs M569 P0.4 S1 ;Z2 motor runs M569 P0.5 S1 ;Z3 motor runs M569 P50.0 S0 ;E moves M569 P0.3 S0 ;U motor runs M569 P50.1 S1 ;V motor runs (front clamp driver) M569 P50.2 S1 ;W motor runs (back clamp driver) M207 S1.5 F7200 Z0.2 ;set retract length M584 X0.0 Y0.1 Z0.2:0.4:0.5 E50.0 U0.3 V50.1 W50.2 ;Set drive mapping M350 X16 Y16 Z16 E16 U16 V16 W16 I1 ;configure microstepping with interpolation M92 X80.00 Y80.00 Z400.00 E685.37234 U100 V80 W80 ;set steps per mm M566 X900.00 Y900.00 Z60.00 E300 U900.00 V900 W900 ;set maximum instantaneous speed changes (mm/min) M203 X6000.00 Y6000.00 Z180.00 E7200 U17000.0 V6000 W6000 ;set maximum speeds (mm/min) M201 X500.00 Y500.00 Z20.00 E3000 U500.0 V500 W500 ;set accelerations (mm/s^2) M906 X800 Y800 Z800 E1200 U3800 V800 W800 I30 ;set motor currents (mA) and motor idle factor in per cent M84 S30 ;Set idle timeout ; Axis Limits M208 X0 Y0 Z-1 U0 V0 W0 S1 ;set axis minima M208 X100 Y100 Z38.45 U330 V55 W55 S0 ;set axis maxima ; Endstops M574 X1 S1 P"0.io8.in" ;configure switch-type (e.g. microswitch) endstop for low end on X via pin io0.in M574 Y2 S1 P"0.io7.in" ;configure switch-type (e.g. microswitch) endstop for high end on Y via pin io1.in M574 Z2 S1 P"0.io2.in+0.io1.in+0.io5.in" ;configure switch-type (e.g. microswitch) endstop for high end on Z M574 U2 S1 P"0.io6.in" ;configure switch-type (e.g. microwswitch) endstop for high end on U M574 V1 S1 P"50.io6.in" ;configure switch-type end stop for low end on V M574 W1 S1 P"50.io5.in" ;configure switch-type end stop for low end on W ; Z-Probe M950 S0 C"0.io4.out" ; create servo pin 0 for BLTouch (use IO_4/5/7 for 6HC) M558 P9 C"0.io4.in" F100 H5 R0.2 T6000 A5 B1 ; set Z probe type to bltouch and the dive height + speeds G31 P25 X-19.14 Y0 Z4.242 ; set Z probe trigger value, offset and trigger height M557 X0:80 Y12:100 P3 ; define mesh grid ;Heaters M308 S0 P"temp0" Y"thermistor" T100000 B3950 ; configure sensor 0 as thermistor on pin temp0 M950 H0 C"0.out0" T0 ; create bed heater output on out0 and map it to sensor 0 M307 H0 R0.075 K0.161:0.000 D3.07 E1.35 S1.00 B0 M140 H0 ; map heated bed to heater 0 M308 S1 P"50.temp_0" Y"thermistor" ; configure sensor 1 as thermistor on pin temp1 M950 H1 C"50.out0" T1 ; create nozzle heater output on out1 and map it to sensor 1 M307 H1 R4.585 K0.421:0.683 D3.75 E1.35 S1.00 B0 V24.2 ; disable bang-bang mode for heater and set PWM limit M143 H1 S280 ; set temperature limit for heater 1 to 280C ; Fans M950 F0 C"0.out7" Q500 ; create fan 0 on toolboard out1 and set its frequency M106 P0 S0 H-1 T50 ; set fan 0 value. Thermostatic control is turned on M950 F1 C"0.out8" Q500 ; create fan 1 on toolboard out2 and set its frequency M106 P1 S0 H-1 ; set fan 1 value. Thermostatic control is turned off ;Tool Definitions M563 P0 D0 H1 F0 ; tool 0 uses extruder drive 0 and heater 1. Fan 0 and Fan 1 are mapped to tool 0 G10 P0 X0 Y0 Z0 ; set tool 0 axis offsets G10 P0 R0 S0 ; set initial tool 0 active and standby temperatures to 0C ;Misc M950 P3 C"0.out2" Q500 ; allocate port 3 to out2 on MB6HC for Inlet valve M42 P3 S0 ; set to off M950 P4 C"50.out2" Q500 ; allocate port 4 to out2 on Mini5 for IPV Direction M42 P4 S0 ; set to off M950 P5 C"50.out1" Q500 ; allocate port 5 to out1 on Mini5 for Chamber Valve M42 P5 S0 ; set to off M950 P6 C"0.out3" Q500 ; allocate port 6 to out3 on MB6HC for Release Valve M42 P6 S0 ; set to off ; Epilogue M556 S100 X0 Y0 Z0 ; Put your axis compensation here M912 P0 S0 ; Put your CPU temperature sensor correction here M501 ; load saved parameters from non-volatile memory M911 S10 R11 P"M913 X0 Y0 G91 M83 G1 Z3 E-5 F1000" ; set voltage thresholds and actions to run on power loss T0
-
RE: Webhooks/Push-Notifications/Polling Tools
@dc42 appreciate the clarification. I assume polling is the only way with ethernet boards then?
-
RE: Webhooks/Push-Notifications/Polling Tools
@oliof I had never heard of this but just did some reading. How cool! Thanks for your quick response
-
Webhooks/Push-Notifications/Polling Tools
I read a few posts from 2017 and 2018 talking push notifications and webhooks. However, it seems like RepRap Notify was the most cohesive project to tackle that problem and is no longer maintained with newer versions of Reprap. I'm wondering if any other developments have been made on this topic? Is polling rr_model the best way to get notifications when jobs are complete or other events happen?
-
RE: FSR Problems
@dc42 The first half of that makes sense. I'll play around with some other potentiometers, revert back to P1, and take the ! character out.
However, I'm uncertain about the series resistor you mention. Are you recommending adding another resistor in series with my pot in order to find the resistance that gets it triggering? or how do you mean?
-
RE: HTTP Endpoint and Cross-Origin Site
@chrishamm Thank you! I didn't realize you could literally use an asterisk. I thought it was a placeholder
-
RE: HTTP Endpoint and Cross-Origin Site
@chrishamm I'm sorry I'm not much of a software engineer so pardon my ignorance, I'll need some additional clarification. Would the C"site" be the site requesting the HTTP post like the backend of my app, like a localhost:3000? Or whats a correct "site" if not?
-
RE: FSR Problems
@Phaedrux Yes I'm using these DF9-40 FSR's all wired in parallel with no board. Switching to mode 8 didn't have any effect
-
HTTP Endpoint and Cross-Origin Site
Hello,
I'm continuing to work on a web app that can upload .gcode files to my machine. However, I've been unable to connect with my machine through HTTP requests. What is the correct formatting for an endpoint for this API? I currently have it like so:
http://xxx.xxx.x.xx/api/files/gcodes but didn't have too much confidence in that.
Additionally, I noticed M586 has a C variable for setting the site of cross-origin HTTP requests. Can I use this to set it to that exact same endpoint or how is the C variable effectively used in this case?
-
RE: FSR Problems
@Phaedrux That helped me clean up a few things but now it's just not triggering at all. Here are my new files
; Configuration file for Duet WiFi (firmware version 3.3) ; executed by the firmware on start-up ; ; generated by RepRapFirmware Configuration Tool v3.3.15 on Sun Mar 12 2023 14:20:36 GMT-0400 (Eastern Daylight Time) ; General preferences G90 ; send absolute coordinates... M83 ; ...but relative extruder moves M550 P"FSR Test Bench" ; set printer name ; Network M552 S1 ; enable network M586 P0 S1 ; enable HTTP M586 P1 S0 ; disable FTP M586 P2 S0 ; disable Telnet ; Drives M569 P0 S1 ; physical drive 0 goes forward M569 P1 S1 ; physical drive 1 goes forward M569 P2 S1 ; physical drive 2 goes forward M584 Y0 X1 Z2 ; set drive mapping M350 X16 Y16 Z16 I1 ; configure microstepping with interpolation M92 X80.0 Y80.0 Z400.00 ; set steps per mm M566 X900 Y900 Z60.00 ; set maximum instantaneous speed changes (mm/min) M203 X6000 Y6000 Z180.00 ; set maximum speeds (mm/min) M201 X500 Y500 Z20.00 ; set accelerations (mm/s^2) M906 X800 Y800 Z800 I30 ; set motor currents (mA) and motor idle factor in per cent M84 S30 ; set idle timeout ; Axis Limits M208 X0 Y0 Z0 S1 ; set axis minima M208 X100 Y100 Z100 S0 ; set axis maxima ; EndStop M574 X1 S1 P"xstop" M574 Y1 S1 P"ystop" M574 Z1 S2 ;define Z probe as low end ; Z-Probe M558 P1 C"^zprobe.in" H5 F100 ;mode 1 on z-probe in G31 P500 X0 Y0 Z0.7 ;set trigger value, xy offsets, and Z trigger height ;M557 X0:20 Y0:20 P2
; homez.g G90 ; back to absolute mode G1 X0 Y0 F2000 ; put head over the centre of the bed, or wherever you want to probe G30 ; lower head, stop when probe triggered and set Z to trigger height
-
FSR Problems
Hello,
I'm trying to use FSRs as a z probe and have them mounted on my bed. However, I get the error "G28 Z Error: Probe already triggered at start of probing move" immediately upon trying to home my Z. I'm using a 10k potentiometer, but tuning the resistance on it seems to have no effect. Here is how I have it wired and my config. g.
; Configuration file for Duet WiFi (firmware version 3.3) ; executed by the firmware on start-up ; ; generated by RepRapFirmware Configuration Tool v3.3.15 on Sun Mar 12 2023 14:20:36 GMT-0400 (Eastern Daylight Time) ; General preferences G90 ; send absolute coordinates... M83 ; ...but relative extruder moves M550 P"FSR Test Bench" ; set printer name ; Network M552 S1 ; enable network M586 P0 S1 ; enable HTTP M586 P1 S0 ; disable FTP M586 P2 S0 ; disable Telnet ; Drives M569 P0 S1 ; physical drive 0 goes forward M569 P1 S1 ; physical drive 1 goes forward M569 P2 S1 ; physical drive 2 goes forward M584 Y0 X1 Z2 ; set drive mapping M350 X16 Y16 Z16 I1 ; configure microstepping with interpolation M92 X80.0 Y80.0 Z400.00 ; set steps per mm M566 X900 Y900 Z60.00 ; set maximum instantaneous speed changes (mm/min) M203 X6000 Y6000 Z180.00 ; set maximum speeds (mm/min) M201 X500 Y500 Z20.00 ; set accelerations (mm/s^2) M906 X800 Y800 Z800 I30 ; set motor currents (mA) and motor idle factor in per cent M84 S30 ; set idle timeout ; Axis Limits M208 X0 Y0 Z0 S1 ; set axis minima M208 X100 Y100 Z100 S0 ; set axis maxima ; EndStop M574 X1 S1 P"xstop" M574 Y1 S1 P"ystop" M574 Z1 S2 ;define Z probe as low end ; Z-Probe M558 P1 C"!^zprobe.in" H5 F100 ;mode 1 on z-probe in G31 P500 X0 Y0 Z0.7 ;set trigger value, xy offsets, and Z trigger height ;M557 X0:20 Y0:20 P2
and homez.g in case
; homez.g G91 ; relative positioning G1 H1 Z-205 F1800 ; move Z down until the endstop is triggered G30
-
Static Testing FSRs
Hello, while reading through the test and calibrate a Z probe page I noticed that you cannot statically test FSRs as the pulse may be too short to notice on DWC.
I want to setup a test bench of just my bed and the FSRs to see if the sensors I choose work and if the arrangement is effective. Will the pulse be observable from the DWC if I continue to keep a force down on my bed such that it's longer than the nozzle briefing touching? or will it still only pulse once quickly right when the force is detected? Is there a better way to test the effectiveness of my FSR setup without a whole extruder?
-
Automatic Uploading to SD Card
Hello, I'm working on a web application to do some batch slicing, then automatically send the files to the machine to start printing. I noticed M32 is used to select and initiate the file from the SD card at .../gcodes.
I'm here to ask the best way to upload a .gcode file to the /gcode folder on the SD card using Java/HTML. Is there a way to use SSH/SFTP for File Transfer or HTTP POST? I'm only a novice when it comes to development so a little unsure how to approach this one.
(Posted in wrong forum before)