@phaedrux Nope, the config file loads completely successfully both with M98
or at board reset
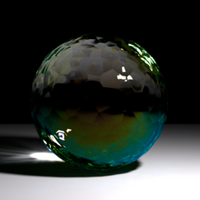
Posts made by dflemstr
-
RE: Trouble diagnosing high-temperature extruder (65W) heater faults
-
RE: Trouble diagnosing high-temperature extruder (65W) heater faults
@phaedrux sure, here you go! Thanks for the help so far. Full config.g. Please ignore some of the comments that are a bit out of date
-
RE: Trouble diagnosing high-temperature extruder (65W) heater faults
@phaedrux Here's a graph of me heating up Heater 1 to 250C:
I've very unscientifically marked with teal arrows where the heater faults occur, and at that point I run
M562 P1
followed by re-activating the tool withT0 P0
(or clicking on "Heater 1" in the UI). Eventually the tool heats up and is rock solid at 250C, no problems whatsoever.Some version info:
$ M115 FIRMWARE_NAME: RepRapFirmware for Duet 3 MB6HC FIRMWARE_VERSION: 3.3 ELECTRONICS: Duet 3 MB6HC v1.01 or later FIRMWARE_DATE: 2021-06-15 21:45:56 $ M115 B20 Duet TOOL1LC firmware version 3.3 (2021-06-15 16:12:58)
-
Trouble diagnosing high-temperature extruder (65W) heater faults
Hey,
I'm setting up my printer for high temperature printing (<500C) and I've step-by-step been replacing one part at a time on my extruder: first using a PT1000 sensor, then moving to a plated copper heater cartridge, then switching to a E3D NozzleX extruder, then a titanium heat break, and finally a water cooled extruder heat sink. These changes all went fine and I've been able to run the printer successfully for a few weeks after these changes. However the printer with this configuration struggled to maintain high temperatures; I assumed it was due to an underpowered heater cartridge.
Now I replaced the heater cartridge from using a 40W to using a 65W cartridge, to be able to keep temperatures more stable, and sure enough when the printer reaches the set temperature, it keeps that temperature perfectly. However, while heating up (even to a low temperature like 250C) the heater consistently faults with no apparent error message. If I reset the fault and resume heating, the heater eventually reaches 250C fine. I've been diagnosing the errors with 250C for now just to get repeatable measurements and to not play around with potentially dangerously high temperatures, but of course I'll be looking for a solution that also works up to 500C.
Things I have checked:
- My PSU is a reputable brand (Meanwell) and rated to 350W.
- I'm using 3 extruders like this with a Duet 3 Tool Board, and since my system is 24V, the tool board should be able to handle a 120W heater according to the specs, so that should be fine I think?
- I've PID auto-tuned the heater several times and it always completes successfully (model parameters are currently e.g.
M307 H1 R2.554 C349.500:118.400 D7.30 S1.00 V23.3 B0
for one of the 3 extruders) - The extruder has a pretty powerful PCF (as you can guess from the above heater params) but the faults don't ever occur due to turning on the PCF; they happen even when the PCF is completely turned off.
- Running with
M929 S3
logs absolutely nothing when the heater fault occurs. - Each heater is limited to 500C with e.g.
M143 H1 S500
- I have not changed
M570
at all, maybe I should for this case? Feels dangerous...
Any ideas?
-
RE: Wiring/configuration of standard 4-pin PWM fans on Duet 3 MB6HC
@dc42 I'll have to try that another day unfortunately since I'm in the middle of reorganizing my workshop and I don't have my stash of resistors available right now, and since I had a spare fan controller lying around that made things work I'm not in a hurry to try other methods. I'll try to remember to report back to this thread when I revisit this issue.
-
RE: Wiring/configuration of standard 4-pin PWM fans on Duet 3 MB6HC
@dc42 I used the standard PC fan-style connector and connected it straight to the board with all 4 pins aligned; the keyed piece of plastic fit into the matching slot in the fan connector.
-
RE: Wiring/configuration of standard 4-pin PWM fans on Duet 3 MB6HC
Immediately after my last post, I realized what could be a possible solution: I put the dedicated fan controller inbetween the Duet and the fan, and since the fan controller has a relative speed function (ie. if you set it to 90% it will output 90% of the incoming PWM, so 90% of 70% = 63% for example), it had to have some sort of timer circuitry on its own and do its own PWM generation.
So, setting the FC to 100% makes it interpret the (somehow non-standard) Duet PWM, and convert it into a PWM curve that the fan can understand, which means everything works now! There's an additional benefit that the FC has a "keep the fan running" function which will kick it even if the fan stalls under very low RPM.
Ideally it would be nice if the Duet 3/RRF could output a standard PWM signal that's compatible with these fans; I have used these fans on tons of PC builds before and they have never been problematic so I think there's something to fix with the Duet PWM, but I won't have time to dive in with an oscilloscope today unfortunately!
-
RE: Wiring/configuration of standard 4-pin PWM fans on Duet 3 MB6HC
@achrn said in Wiring/configuration of standard 4-pin PWM fans on Duet 3 MB6HC:
Is it installed with the filter? Does it run if it isn't pushing against the filter? (I'm only grasping at straws).
I can run it just fine with a separate 12V power supply and a dedicated fan controller (using a Noctua NA-FC1). If nothing else works, I might have to insert that fan controller in between the Duet and the fan and then I won't get software speed control, but at least on/off functionality.
-
RE: Wiring/configuration of standard 4-pin PWM fans on Duet 3 MB6HC
@achrn Thanks for linking to the other post, I hadn't found that one when searching for similar issues.
I tried a few different values for
B
now as you suggested, but it doesn't seem to help. I also notice that going down from 98% to anything lower makes the fan turn off completely, despite its momentum from having already been spinning just before, so I really think it has something to do with the PWM generation.I can always try a different fan but it would be unfortunate because I need a high-static-pressure fan for this purpose; it needs to push air through an activated carbon/HEPA filter.
-
Wiring/configuration of standard 4-pin PWM fans on Duet 3 MB6HC
Hey,
I'm trying to figure out how to wire/configure a standard PC fan (I'm using a Noctua NF-A14 industrialPCC-300 PWM fan), using a Duet 3 MB6HC with DWC 3.3.0 and RRF 3.3 (built 2021-06-15).
I already have tons of fans and tools set up just fine (this is a 4-tool toolchanger with 8 existing fans; various 24v/12v on dedicated toolboards etc), so I'm no stranger to setting things up in RRF.
I've attached this new fan to the OUT4 header on the mainboard without any custom stuff (no extra resistors or diodes etc) and the power delivery jumper for the bank is set to 12V (my input voltage is 24V).
I'm configuring the fan like so in
config.g
:M950 F8 C"!out4+out4.tach" Q25000 M106 P8 C"Exhaust" S0.5 H-1
When restarting the board with
M999
the fan speed is set automatically to 50% but the fan does not spin. When I bring the fan to around 98-100% it starts spinning at full speed and the RPM is reported correctly via the tach pin.How can I get the fan speed to scale linearly with the
M106 S
parameter? Do I need to do any hardware mods, or is there some setting I'm missing?