I think the easiest answer is all of the issues related to Cartesian printers and movements were solved with pen plotters and dot matrix printers. Big companies have been able to produce the most efficient and cheap way to solve the issues so other than a moving Z platform it's virtually plug and play. Also, as I stated previously the processing power to control 4 stepper motors was right at the limit for 8 bit boards. Another disadvantage is the size of the machine, it has to be much taller than the equivalent sized cartesian due to movement required for the edges of the bed, also the bed is round rather than square / rectangular.
The Kinematic control of the head has caught up now so it's lovely and smooth, by design the head will be horizontal (although I did read of paper where they had printed in a terrain following method for the top layers, just required knowledge of the head shape to avoid clashes - this was a few years ago and I can't find any further work carried out - maybe Simplify3D V5 
My SpiderBot is the V1.5 with various upgrades through SpiderBot and the prototype dual head. Attached are a couple of pictures, maybe best to have them side by side as the cantilever of the head via the servo is subtle but is an elegant solution to dual head woes (one of my other printers is the BigBox Dual with print heads the same height so I'm used to suffering the issues with the 1st layer).
[http://www.spiderbot.eu/spiderbot-v2-1-whats-new/?lang=en](link url)
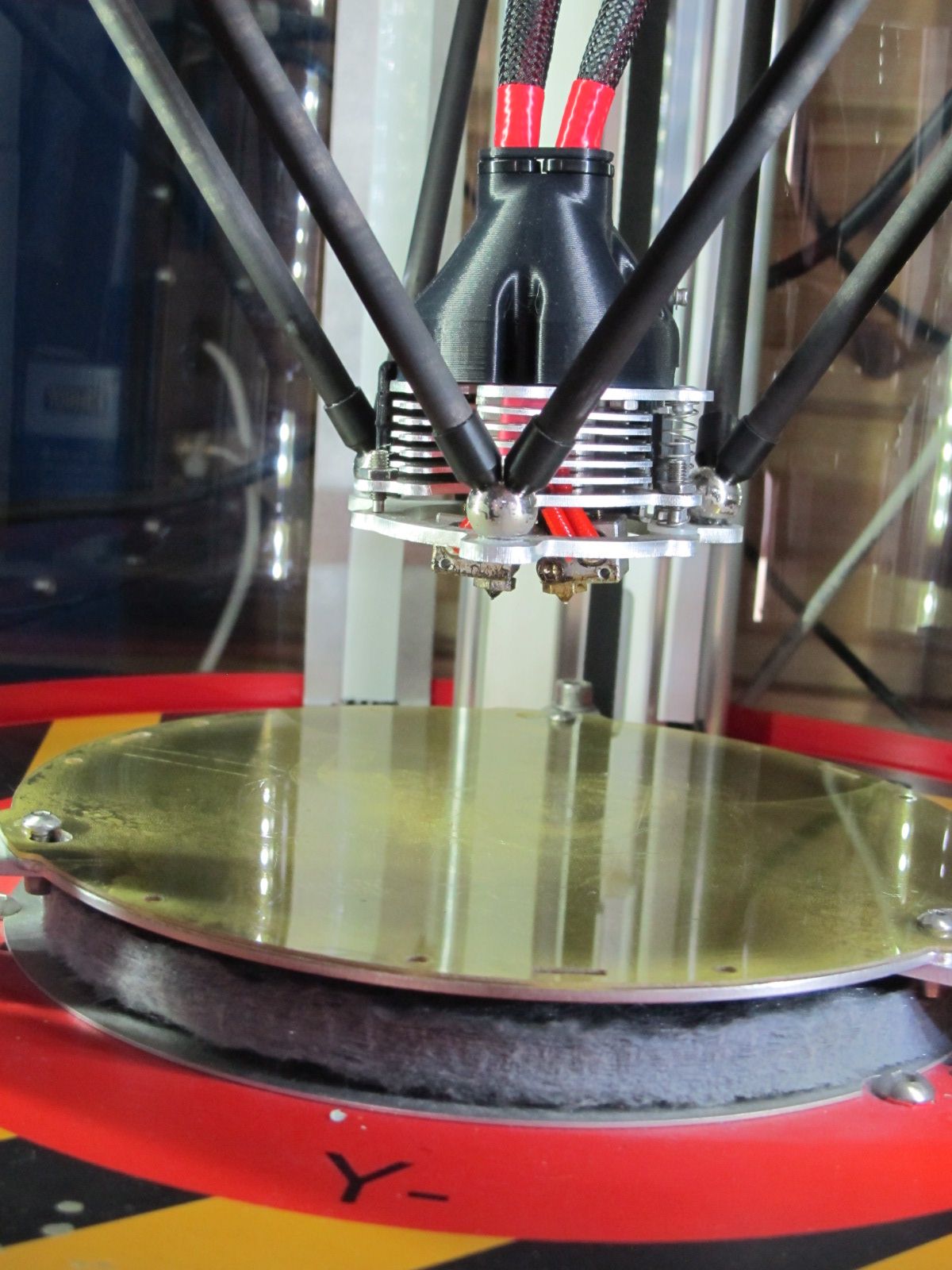
The original design used ball bearings secured with epoxy, as the printer is used with a heated chamber this heat cycling (or my cold shed) caused them to fall off. Philippe (owner of SpiderBot) improved the design by riveting the balls onto the aluminium.
I'm more than happy with mine and the assistance I've had over the years for SpiderBot, it just doesn't get used as much due to having multiple printers and not using ABS.
It's well worth having a nosey though the older blog articles to see the engineering iterations leading up to the latest versions.