@fcwilt I remove those statements and turns out I had the XY's not lined up with the z drivers and now it works great The only problem I'm having now and I was going to spend tomorrow messing with it is that my first test print the z-axis everything leveled at home that's wonderful but then it was 5 mm away from the bed so I'm sure I've got it some adjustments to do
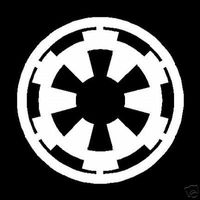
Best posts made by austinious
-
RE: 3 Independent Z Motors - Trouble with Autolevel
Latest posts made by austinious
-
RE: 3 Independent Z Motors - Trouble with Autolevel
@fcwilt I remove those statements and turns out I had the XY's not lined up with the z drivers and now it works great The only problem I'm having now and I was going to spend tomorrow messing with it is that my first test print the z-axis everything leveled at home that's wonderful but then it was 5 mm away from the bed so I'm sure I've got it some adjustments to do
-
RE: 3 Independent Z Motors - Trouble with Autolevel
@engikeneer
We'll see if I get that far. I usually stop tweaking when I get an acceptable print. I'm largely going to be making jigs and stamps for leatherworking, but I hope to make some neat stuff out of NylonX -
RE: 3 Independent Z Motors - Trouble with Autolevel
@engikeneer
G28
Leadscrew adjustments made: -0.591 -1.472 -2.315, points used 3, (mean, deviation) before (-1.019, 0.476) after (0.000, 0.000)WooHoo!
Thanks for the help, I really appreciate it! I increased my M671 to 3mm, reading up on the mesh. -
RE: 3 Independent Z Motors - Trouble with Autolevel
@engikeneer thanks! I found the M671 just as you replied....lol. Is there any reason to not increase that to 5mm?
I'm reading up on the heightmap and mesh, thanks for the links!
-
RE: 3 Independent Z Motors - Trouble with Autolevel
Success! Sort of...
G28
Error: Some computed corrections exceed configured limit of 0.50mm: -0.599 -1.480 -2.324
Error: Height map file 0:/sys/heightmap.csv not foundI assume there is a setting to determine how much adjustment. But hey! Progress!
bed.g
<
; bed.g - I added some lowering between probes due to the bed being off.
; called to perform automatic bed compensation via G32
;
; generated by RepRapFirmware Configuration Tool v3.3.10 on Sat Dec 11 2021 09:34:44 GMT-0500 (Eastern Standard Time)
G30
G30 P0 X100 Y0 Z-99999 ; probe near rear leadscrew
G1 Z-10 F6000 ; lower Z again
G30 P1 X233 Y280 Z-99999 ; probe near left leadscrew
G1 Z-10 F6000 ; lower Z again
G30 P2 X0 Y280 Z-99999 S3 ; probe near right leadscrew and calibrate 3 motors
G29 S1 ; probe the bed and enable compensation -
RE: 3 Independent Z Motors - Trouble with Autolevel
@engikeneer Thanks, I'll work with that when I get home. I have to do some reading about height map it seems....no idea what it does.
-
RE: 3 Independent Z Motors - Trouble with Autolevel
One thing just hit me....I'm not sure the G30 P#'s in the bed.g correspond to the driver assignments in config.g, could it be that simple?
-
RE: 3 Independent Z Motors - Trouble with Autolevel
I do not have the exact bed file here at work, the only difference is the X,Y's are different than what I am posting here. I can post the exact file later today. Just a reminder as you look through this, everything works EXCEPT autolevel. G30 will home the z axis, and the probe works as intended.
Thanks!
config.g
<; Configuration file for Duet 3 (firmware version 3.3)
; executed by the firmware on start-up
;
; generated by RepRapFirmware Configuration Tool v3.3.10 on Sat Dec 11 2021 09:34:44 GMT-0500 (Eastern Standard Time); General preferences
M575 P1 S1 B57600 ; enable support for PanelDue
G90 ; send absolute coordinates...
M83 ; ...but relative extruder moves
M550 P"redacted" ; set printer name; Network
M551 P"nothingToSeeHere" ; set password
M552 P0.0.0.0 S1 ; enable network and acquire dynamic address via DHCP
M586 P0 S1 ; enable HTTP
M586 P1 S0 ; disable FTP
M586 P2 S0 ; disable Telnet; Drives
M569 P0.3 S1 ; physical drive 0.3 goes forwards
M569 P0.4 S1 ; physical drive 0.4 goes forwards
M569 P0.0 S1 ; physical drive 0.0 goes forwards
M569 P0.5 S1 ; physical drive 0.5 goes forwards
M584 X3 Y4 Z0:1:2 E5 ; set drive mapping
M350 X16 Y16 Z16 E16 I1 ; configure microstepping with interpolation
M92 X160.00 Y160.00 Z8000.00 E409.00 ; set steps per mm
M566 X900.00 Y900.00 Z60.00 E120.00 ; set maximum instantaneous speed changes (mm/min)
M203 X6000.00 Y6000.00 Z180.00 E1200.00 ; set maximum speeds (mm/min)
M201 X500.00 Y500.00 Z20.00 E250.00 ; set accelerations (mm/s^2)
M906 X800 Y1600 Z800 E800 I30 ; set motor currents (mA) and motor idle factor in per cent
M84 S30 ; Set idle timeout; Axis Limits
M208 X0 Y0 Z0 S1 ; set axis minima
M208 X400 Y400 Z400 S0 ; set axis maxima; Endstops
M574 X1 S1 P"!io1.in" ; configure switch-type (e.g. microswitch) endstop for low end on X via pin !io1.in
M574 Y1 S1 P"!io2.in" ; configure switch-type (e.g. microswitch) endstop for low end on Y via pin !io2.in; Z-Probe
M950 S0 C"io4.out" ; create servo pin 0 for BLTouch
M558 P9 C"io4.in" H5 F120 T6000 ; set Z probe type to bltouch and the dive height + speeds
G31 P500 X0 Y0 Z2.5 ; set Z probe trigger value, offset and trigger height
M557 X50:350 Y50:350 S25 ; define mesh grid; Heaters
M308 S0 P"temp0" Y"thermistor" T100000 B4725 C7.06e-8 ; configure sensor 0 as thermistor on pin temp0
M950 H0 C"out1" T0 ; create bed heater output on out1 and map it to sensor 0
M307 H0 B1 S1.00 ; enable bang-bang mode for the bed heater and set PWM limit
M140 H0 ; map heated bed to heater 0
M143 H0 S120 ; set temperature limit for heater 0 to 120C
M308 S1 P"temp1" Y"thermistor" T100000 B4725 C7.06e-8 ; configure sensor 1 as thermistor on pin temp1
M950 H1 C"out2" T1 ; create nozzle heater output on out2 and map it to sensor 1
M307 H1 B0 S1.00 ; disable bang-bang mode for heater and set PWM limit
M143 H1 S280 ; set temperature limit for heater 1 to 280C; Fans
M950 F0 C"out8" Q500 ; create fan 0 on pin out8 and set its frequency
M106 P0 C"HotEnd" S0 H1 T45 ; set fan 0 name and value. Thermostatic control is turned on
M950 F1 C"out9" Q500 ; create fan 1 on pin out9 and set its frequency
M106 P1 C"Blower" S0 H-1 ; set fan 1 name and value. Thermostatic control is turned off; Tools
M563 P0 S"HotEnd" D0 H1 F0:1 ; define tool 0
G10 P0 X0 Y0 Z0 ; set tool 0 axis offsets
G10 P0 R0 S0 ; set initial tool 0 active and standby temperatures to 0C; Custom settings
M671 X215:7:424 Y-14:395:395 S0.5bed.g
<
; bed.g
; called to perform automatic bed compensation via G32
;
; generated by RepRapFirmware Configuration Tool v3.3.10 on Sat Dec 11 2021 09:34:44 GMT-0500 (Eastern Standard Time)
M561 ; clear any bed transform
G29 ; probe the bed and enable compensation
G30 ; home Z by probing the bed
G30 P0 X130 Y0 Z-99999 ; probe near a leadscrew
G30 P1 X0 Y280 Z-99999 ; probe near a leadscrew
G30 P2 X240 Y280 Z-99999 S3 ; probe near a leadscrew and calibrate 3 motorshomeall.g
<
; homeall.g
; called to home all axes
;
; generated by RepRapFirmware Configuration Tool v3.3.10 on Sat Dec 11 2021 09:34:44 GMT-0500 (Eastern Standard Time)
G91 ; relative positioning
G1 H2 Z5 F6000 ; lift Z relative to current position
G1 H1 X-405 Y-405 F1800 ; move quickly to X and Y axis endstops and stop there (first pass)
G1 H2 X5 Y5 F6000 ; go back a few mm
G1 H1 X-405 Y-405 F360 ; move slowly to X and Y axis endstops once more (second pass)
G1 H1 Z-405 F360 ; move Z down stopping at the endstop
G90 ; absolute positioning
G92 Z0 ; set Z position to axis minimum (you may want to adjust this); Uncomment the following lines to lift Z after probing
;G91 ; relative positioning
;G1 Z5 F100 ; lift Z relative to current position
;G90 ; absolute positioninghomex.g
<
; homex.g
; called to home the X axis
;
; generated by RepRapFirmware Configuration Tool v3.3.10 on Sat Dec 11 2021 09:34:44 GMT-0500 (Eastern Standard Time)
G91 ; relative positioning
G1 H2 Z5 F6000 ; lift Z relative to current position
G1 H1 X-405 F1800 ; move quickly to X axis endstop and stop there (first pass)
G1 H2 X5 F6000 ; go back a few mm
G1 H1 X-405 F360 ; move slowly to X axis endstop once more (second pass)
G1 H2 Z-5 F6000 ; lower Z again
G90 ; absolute positioninghomey.g
<
; homey.g
; called to home the Y axis
;
; generated by RepRapFirmware Configuration Tool v3.3.10 on Sat Dec 11 2021 09:34:44 GMT-0500 (Eastern Standard Time)
G91 ; relative positioning
G1 H2 Z5 F6000 ; lift Z relative to current position
G1 H1 Y-405 F1800 ; move quickly to Y axis endstop and stop there (first pass)
G1 H2 Y5 F6000 ; go back a few mm
G1 H1 Y-405 F360 ; move slowly to Y axis endstop once more (second pass)
G1 H2 Z-5 F6000 ; lower Z again
G90 ; absolute positioninghomez.g - This is the file I have messed with the most with no luck.
<
; homez.g
; called to home the Z axis
;
; generated by RepRapFirmware Configuration Tool v3.3.10 on Sat Dec 11 2021 09:34:44 GMT-0500 (Eastern Standard Time)
G91 ; relative positioning
G1 H2 Z5 F6000 ; lift Z relative to current position
G1 H1 Z-405 F1800 ; move Z down until the endstop is triggered
G92 Z0 ; set Z position to axis minimum (you may want to adjust this); Uncomment the following lines to lift Z after probing
;G91 ; relative positioning
;G1 Z5 F100 ; lift Z relative to current position
;G90 ; absolute positioning -
RE: 3 Independent Z Motors - Trouble with Autolevel
@fcwilt no endstops for the z, just the BLTouch. Not sure why I get the error, "G28 Z endstop not enabled". I didn't define an endstop in the config tool, just the probe. And G30 works like a charm.