I include GFCI protection in the form of a GFCI cord cap.
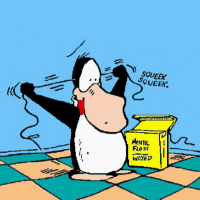
Posts made by Alexander Mundy
-
RE: AC Heated Bed Wiring Validation
-
RE: A way to extend the micro SD on the PanelDuet 5" to an SD card
Just a follow up note I learned yesterday. I bought a micro SD to micro SD extender to use with a PI 4 in a custom printed case for a digital dash display and it did not boot correctly. A little googlefu led me to https://forum.4dsystems.com.au/node/43404/page2#post55236 . There was a 330 ohm resistor on this new extender board between SCLK and VDD. Crushed (crude but effective) the 330 SMD resistor and it booted fine.
-
RE: A way to extend the micro SD on the PanelDuet 5" to an SD card
I have used this one on multiple 4D Systems intelligent display projects to make the card accessible on custom cases but never tried it on paneldue or duet.
-
RE: Duet Wifi and nimble acceleration issue
The patterns were also a sometimes symptom with V1. Mine were some of the first sold and 1 printed flawless and 1 had the repeating pattern. Turned out to be the shaft undersized on the hob which Zesty replaced. Some of the original flex shafts had a defect and Zesty sent everyone new replacements. Same with the bodies. I give them kudos for customer service. Later 1 of them started the patterns and it was a worm bearing going bad. I replaced all bearings with ceramic ones and no problems since. I certainly wish I would have bought additional V1's while they were available. Too bad they have had the technical problems, when working properly (and IMO with the portscap stepper no need to go to V2 with 20:1 as I have tested retraction all the way up to 100 mm/s without skipping) they are top notch.
-
RE: Duet Wifi and nimble acceleration issue
@fcwilt 4 times what I paid but still way cheaper than retail:
https://www.ebay.com/itm/192599739125
If you look at the pics it is the same part#. In fact mine came with the "theta assembly" label pigtail also. Escap is Portescap's old name.
-
RE: Duet Wifi and nimble acceleration issue
I did away with all the settings and interaction problems by going to Portescap P430 258 005 01 3.6 degree ultra low rotor inertia disc permanet magnet steppers for my Nimble extruders. I'll never go back to conventional steppers with a high ratio extruder after using them, they are like a sports car vs a Yugo for starting, stopping, and reversing direction in comparison to the suggested Nema 17 pancake and Nema 14. Expensive new, but they can occasionally be found used at a decent cost.
-
RE: RepRapFirmware 3.0 is released!
FYI for anyone else moving from early beta (before 11) I had to do the following:
Define heaters and associated temp sensors
Use M308 instead of M305
Activate the pullup resistors for endstops and z probe if needed since they are not active by default
I had remapped the bed heat and part cooling fans previously and had M950 H0 C"nil" and M950 H2 C"nil" but removed them since heaters are no longer automatically assigned. -
RE: RepRapFirmware 3.0 is released!
Thank you. I lost track of 3 beta after I got it working for one of my printers that needed the remapping features because it worked and I didn't need more. But now that stable is out I figure time to upgrade because future release will be based from this one.
-
RE: RepRapFirmware 3.0 is released!
Not before Beta 12, at least that I could find.
-
RE: RepRapFirmware 3.0 is released!
So what if any config changes would I need to make going from 3.0 Beta on a Duet2 WiFi? I already use S1 in M574.
Firmware Name: RepRapFirmware for Duet 2 WiFi/Ethernet
Firmware Electronics: Duet WiFi 1.02 or later
Firmware Version: 3.0beta5+4 (2019-06-22b1)
WiFi Server Version: 1.23
Web Interface Version: 1.22.6G90 ; Send absolute coordinates... M83 ; ...but relative extruder moves M665 R226.747 L470.983 B200 H860.970 X-0.483 Y-0.268 Z0 ; Set delta radius, diagonal rod length, printable radius and homed height M666 X0.18 Y-0.11 Z-0.07 A0.17 B-0.18 ; Put your endstop adjustments here, or let auto calibration find them M579 X0.998 Y0.999 ; Non Linear Advance M592 D0 A0.001 B0.0004 L0.4 ; PETG ; Network M550 P"400" ; Set machine name M552 S1 ; Enable network M586 P0 S1 ; Enable HTTP M586 P1 S0 ; Disable FTP M586 P2 S0 ; Disable Telnet ; Drives M569 P0 S1 ; Physical drive 0 goes forwards M569 P1 S1 ; Physical drive 1 goes forwards M569 P2 S1 ; Physical drive 2 goes forwards M569 P3 S1 ; Physical drive 3 goes forwards M350 E16 I0 ; Configure microstepping without interpolation M350 X16 Y16 Z16 I1 ; Configure microstepping with interpolation M92 X160 Y160 Z160 E1330 ; Set steps per mm M566 X600 Y600 Z600 E600 ; Set maximum instantaneous speed changes (mm/min) M203 X18000 Y18000 Z18000 E10000 ; Set maximum speeds (mm/min) M201 X1500 Y1500 Z1500 E1500 ; Set accelerations (mm/s^2) M906 X1200 Y1200 Z1200 E1200 I30 ; Set motor currents (mA) and motor idle factor in per cent M84 S30 ; Set idle timeout ; Axis Limits M208 Z-0.1 S1 ; Set minimum Z ; Endstops M574 X2 Y2 Z2 S1 ; Set active high endstops ; Z-Probe M558 P5 R0.5 H3 F100 T3000 I1 A5 S0.02 ; Set Z probe type to effector and the dive height + speeds G31 P500 X0 Y0 Z-0.064 ; Set Z probe trigger value, offset and trigger height ;M558 P1 R0.5 H2 F100 T3000 I1 A5 S0.02 ; Set Z probe type to effector and the dive height + speeds ;G31 P485 X0 Y0 Z-0.064 ; Set Z probe trigger value, offset and trigger height M557 R195 S20 ; Define mesh grid M950 H0 C"nil" M950 H2 C"nil" M950 F0 C"nil" ; Heaters M950 H0 C"e1heat" Q10 ; Remap bed heater to e1 heater and frequency to 10hz M143 H0 S120 ; Set Bed temperature limit to 120C M305 P0 T100000 B3950 R4700 ; Set Bed thermistor + ADC parameters M307 H0 A318.5 C876.2 D4.2 B0 ; Bed PID M143 H1 S280 ; Set Hot End temperature limit to 280C M305 P1 T100000 B4388 R4700 ; Set Hot End thermistor + ADC parameters M307 H1 A491.5 C268.4 D3.8 B0 ; Hot End PID ; Fans M950 F0 C"bedheat" Q25500 ; Map Part Fan to bed heater mosfet / freq 25.5Khz M106 P0 S0 L125 X255 B0.2 ; Part Fan starts off / Min 50% / Max 100% / 100% for 0.2 Sec when turned ; on M106 P1 T50 S255 H1 ; Hot End Fan 100% when Hot End >= 50C M106 P2 T50 S125 H1 ; Extruder Stepper Fan 50% when Hot End >= 50C ; Tools M563 P0 D0 H1 ; Define tool 0 G10 P0 X0 Y0 Z0 ; Set tool 0 axis offsets G10 P0 R0 S0 ; Set initial tool 0 active and standby temperatures to 0C T0 ; select first hot end M80 ; PS_ON to activate relay for heaters
-
RE: PS_ON pin: what can control it?
BTW as far as I know it currently will not deactivate when not printing.
-
RE: PS_ON pin: what can control it?
Forgot to mention, and you may have one already, that you should have a thermal fuse in the heater or mechanically attached to the bed unless it is powered low enough it won't get to dangerous temperatures anyway.
-
RE: PS_ON pin: what can control it?
It deactivates when the print is cancelled by a heater fault. I think default is still 10 min which is way too long if wanting to kill the heater via relay etc but is configurable now.
https://duet3d.dozuki.com/Wiki/Gcode#Section_M570_Configure_heater_fault_detection
"Snnn Timeout in minutes for print to be cancelled after heater fault (Firmware 1.20 and later)."
-
RE: PS_ON pin: what can control it?
On my mains bed powered printer I use a contactor (relay) and an SSR wired in series on the ungrounded mains wire and another contact of the same contactor and another SSR wired in series on the grounded conductor of the mains bed heat all controlled by PS_ON. All 3 would have to fail closed to cause the bed heat not to respond. The contactor also will open the hot end heater circuit if for some reason the Mosfet in the Duet failed on. I also have a GFCI cord cap on the printer cord so it and the cord are ground fault protected. Overkill? Some would say yes but I have better peace of mind with the few additional components. I have intention of adding an independent watchdog in case for some reason the Duet freezes because all the above would be moot in that event but haven't implemented that yet. I do not however leave any of my printers printing without human oversight either in person or on premise via camera.
-
RE: Polar CNC?
For tax purposes before midnight I went ahead and ordered another Duet 2. If CNC mode and polar kinematics don't play well together at least I've got another board for a printer.
-
RE: Polar CNC?
Sorry, should have mentioned I have no intention of using the aluminum frame it came with. Was thinking of possibly making it an add on mount for my lathe/mill or possibly building a stand alone micro for very small (less than an inch work piece) mill. I didn't know if the polar kinematics would be appropriate since I have the parts to implement that.
-
Polar CNC?
I have aquired 2 Parker Daedal linear tables and a rotary table with vacuum table in an assembly with SLO-SYN KML061F03 stepper motors, SLO-SYN SS2000MD7 drives, 48V linear power supply, 24V linear power supply, and a few misc sensors and steppers that came from a prototyping rig. Crazy idea, but since I picked up this stuff for next to nothing I was thinking about using the rotary table and one linear table for polar with the other linear table for Z axis for a miniature CNC mill. Does anyone have any experience with using the polar kinematics for CNC milling or will it not work? If it will work does anyone have a suggestion between Duet 2 or 3 for controller board? I have only built printers so I have no experience with CNC milling equipment.
-
RE: Any good light weight direct extruder/hot-end?
@zapta said in Any good light weight direct extruder/hot-end?:
@gtj0 said in Any good light weight direct extruder/hot-end?:
Balance that against the mass of the drive shaft, which you still have to move, and it may be a better arrangement for some.
IIRC, several people mentioned in posts here that the flex cable tends to wear out. Is it so?
I've had 2 for over 2 years and they are just fine. As I posted before, I am a hobbiest so probably just 30 kg or so of filament used.
-
RE: Any good light weight direct extruder/hot-end?
He designed an adapter and had it shapeways printed that accepts the small D shaft and has a square end that goes in the worm gear where the cable normally goes.
My cables are original black sheath version (well they sent us original buyers replacements shortly thereafter because of a production defect) and they have been using a newer version for some time now but I don't have the red sheath version. I have had no problems, but I'm a hobbiest printer. However I have followed the Nimble since the beginning and have not heard of cables wearing out, only a few production issues here and there.
Can't speak to the Nema 8 since I've not tried it.