I dont like it all, things are not organized in any way, I just converted back
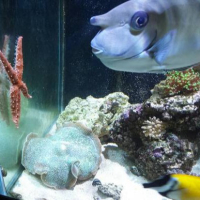
Best posts made by 57buick
-
RE: Magnetic Filament sensor issue
-
RE: DC42 IR sensor and Z homing
again, answered my own question, apparently the old deploy and retract g files for when I had the bltouch were conflicting. I deleted those files and error went away
Latest posts made by 57buick
-
RE: M376 and where to use it
@phaedrux So just put my G29 s1 and M376 H10 at the end of the drive section?
; Configuration file for Duet 3 (firmware version 3.3)
; executed by the firmware on start-up
;
; generated by RepRapFirmware Configuration Tool v3.3.10 on Sun May 08 2022 18:05:16 GMT-0700 (Pacific Daylight Time); General preferences
G90 ; send absolute coordinates...
M83 ; ...but relative extruder moves
M550 P"ratrig500" ; set printer name
M669 K1 ; select CoreXY mode; Wait a moment for the CAN expansion boards to start
G4 S1; Network
M552 P192.168.50.107 S1 ; enable network and acquire dynamic address via DHCP
M586 P0 S1 ; enable HTTP
M586 P1 S0 ; disable FTP
M586 P2 S0 ; disable Telnet; Drives
M569 P0.0 S0 ; physical drive 0.0 goes backwards
M569 P0.1 S0 ; physical drive 0.1 goes backwards
M569 P0.2 S0 ; physical drive 0.2 goes backwards
M569 P3 S1 ; physical drive 0.3 goes forwards
M569 P4 S1 ; physical drive 0.4 goes forwards
M569 P121.0 S0 ; physical drive 121.0 goes backwards
M584 X4 Y3 Z0:1:2 E121.0 ; set drive mapping
M350 X16 Y16 Z16 E16 I1 ; configure microstepping with interpolation
M92 X80.00 Y80.00 Z800.00 E420.00 ; set steps per mm
M566 X600.00 Y600.00 Z50 E600 P1 ; set maximum instantaneous speed changes (mm/min)
M203 X10800.00 Y10800.00 Z600.00 E3600.00 ; set maximum speeds (mm/min)
M201 X3000.00 Y3000.00 Z100.00 E3600.00 ; set accelerations (mm/s^2)
M906 X1200 Y1200 Z1400 E800 I50 ; set motor currents (mA) and motor idle factor in per cent
M84 S30 ; Set idle timeout
G29 S1
M376 H10; Axis Limits
M208 S1 X-11 Y20 z-550 ; set axis lower limits
M208 S0 X510 Y510 z500 ; set axis upper limits; Endstops
M574 X1 S1 P"121.io1.in" ; configure switch-type (e.g. microswitch) endstop for low end on X via pin 121.io1.in
M574 Y2 S1 P"io0.in" ; configure switch-type (e.g. microswitch) endstop for high end on Y via pin io0.in
M574 Z1 S2; Z-Probe
M558 P8 C"121.io0.in" H10 F150 T4000 ; set Z probe type to unmodulated and the dive height + speeds
G31 P50 X-20 Y-10 Z1.55 ; set Z probe trigger value, offset and trigger height
M671 X-85:238:560 Y-5:578:-5 S7.5 ;Leadscrew locations
M557 X30:470 Y30:470 P5 ;define mesh grid; Heaters
M308 S0 P"temp0" Y"thermistor" T100000 B4138 ; configure sensor 0 as thermistor on pin temp0
M950 H0 C"out0" T0 ; create bed heater output on out1 and map it to sensor 0
M307 H0 R0.359 K0.109:0.000 D5.73 E1.35 S1.00 B0 ; disable bang-bang mode for the bed heater and set PWM limit
M140 H0 ; map heated bed to heater 0
M143 H0 S150 ; set temperature limit for heater 0 to 150C
M308 S1 P"121.temp0" Y"pt1000" ; configure sensor 1 as PT1000 on pin 121.temp0
M950 H1 C"121.out0" T1 ; create nozzle heater output on 121.out0 and map it to sensor 1
M307 R=2.821 K=0.691:0.000 D=5.62 ; disable bang-bang mode for heater and set PWM limit
M143 H1 S280 ; set temperature limit for heater 1 to 280C; Fans
M950 F0 C"121.out1" Q500 ; create fan 0 on pin 121.out2 and set its frequency
M106 P0 S0 H-1 ; set fan 0 value. Thermostatic control is turned off
M950 F1 C"121.out2" Q500 ; create fan 1 on pin 121.out1 and set its frequency
M106 P1 S1 H1 T45 ; set fan 1 value. Thermostatic control is turned on; Tools
M563 P0 D0 H1 F0 ; define tool 0
G10 P0 X0 Y0 Z0 ; set tool 0 axis offsets
G10 P0 R0 S0 ; set initial tool 0 active and standby temperatures to 0C;accelerometer settings
M955 P121.0 I14 ; set to toolboard address 121 and orientation of 14; Miscellaneous
T0 ; select first tool -
RE: M376 and where to use it
I have CURA set to do a G32 at the beginning of every print so I assume I would put the M376 H10 at the end of the bed.g file?
-
M376 and where to use it
SO I put my G29 S1 command to use mesh bed leveling at the beginning of my bed.g file.
Do I put the M376 H10 to taper bed leveling in the same bed.g file? or somewhere else?
Do I put it directly after the G29 line or as a last step in the file? The instructions dont specify where to put the m376 -
RE: Failed to enable endstop configuring IR sensor
@fcwilt said in Failed to enable endstop configuring IR sensor:
@57buick said in Failed to enable endstop configuring IR sensor:
Ok I figured out that because its connected to a toolboard it has to be set to P8 not P1 that made it show up in web control so I hit home all and it homes x and Y and then shows all 3 axis homes even though it never went and actually probed the Z?
I don't think you have it all figured out.
Being an IR sensor you should be able to jog the Z axis and when the sensor is close to the bed you should be able to see that state of the Z probe, as reported on the DWC, change.
I always verify the individual pieces of hardware are working before trying to do things like "homeall".
Frederick
Yea I just figured out changed the P1 to P8 made it show up in DWC now and manually putting a aluminum plate under it it changes from 1000 to zero when the led turns on so it is seeing it now. But it still shows homed after it homes the X and Y the Z also immeditately shows homed without actually going and probing the Z
-
RE: Failed to enable endstop configuring IR sensor
Ok I figured out that because its connected to a toolboard it has to be set to P8 not P1 that made it show up in web control so I hit home all and it homes x and Y and then shows all 3 axis homes even though it never went and actually probed the Z?
-
RE: Failed to enable endstop configuring IR sensor
Also dose duet web control still supposed to show the Z probe sensor? Cus its not showing it anywhere on the web control to see what its reading?
-
Failed to enable endstop configuring IR sensor
Im building a ratrig and I have the X and Y homing fine but after configuring the DC42 IR sensor it homes the X and Y then says "G28 failed to enable endstop"
What am I doing wrong in the config here? I have it wired to a 1LC toolboard to 121.io0.in
Here is my config:
G90 ; send absolute coordinates...
M83 ; ...but relative extruder moves
M550 P"ratrig500" ; set printer name
M669 K1 ; select CoreXY mode; Wait a moment for the CAN expansion boards to start
G4 S1; Network
M552 P192.168.50.107 S1 ; enable network and acquire dynamic address via DHCP
M586 P0 S1 ; enable HTTP
M586 P1 S0 ; disable FTP
M586 P2 S0 ; disable Telnet; Drives
M569 P0.0 S0 ; physical drive 0.0 goes backwards
M569 P0.1 S0 ; physical drive 0.1 goes backwards
M569 P0.2 S0 ; physical drive 0.2 goes backwards
M569 P3 S1 ; physical drive 0.3 goes forwards
M569 P4 S1 ; physical drive 0.4 goes forwards
M584 X4 Y3 Z0:1:2 E5 ; set drive mapping
M350 X16 Y16 Z16 E16 I1 ; configure microstepping with interpolation
M92 X80.00 Y80.00 Z400.00 E420.00 ; set steps per mm
M566 X900.00 Y900.00 Z60.00 E120.00 ; set maximum instantaneous speed changes (mm/min)
M203 X24000.00 Y24000.00 Z180.00 E1200.00 ; set maximum speeds (mm/min)
M201 X10000.00 Y10000.00 Z20.00 E250.00 ; set accelerations (mm/s^2)
M906 X900 Y900 Z1000 E800 I30 ; set motor currents (mA) and motor idle factor in per cent
;M84 S30 ; Set idle timeout; Axis Limits
M208 X0 Y0 Z0 S1 ; set axis minima
M208 X500 Y500 Z500 S0 ; set axis maxima; Endstops
M574 X1 S1 P"121.io1.in" ; configure switch-type (e.g. microswitch) endstop for low end on X via pin 121.io1.in
M574 Y2 S1 P"io0.in" ; configure switch-type (e.g. microswitch) endstop for high end on Y via pin io0.in
M574 Z1 S2
; Z-Probe
M558 P1 C"121.io0.in" H5 F120 T6000 ; set Z probe type to unmodulated and the dive height + speeds
G31 P500 X-20 Y-10 Z2.5 ; set Z probe trigger value, offset and trigger height
M557 X15:400 Y15:400 S20 ; define mesh grid; Heaters
M308 S0 P"temp0" Y"thermistor" T100000 B4138 ; configure sensor 0 as thermistor on pin temp0
M950 H0 C"out1" T0 ; create bed heater output on out1 and map it to sensor 0
M307 H0 B0 S1.00 ; disable bang-bang mode for the bed heater and set PWM limit
M140 H0 ; map heated bed to heater 0
M143 H0 S150 ; set temperature limit for heater 0 to 150C
M308 S1 P"121.temp0" Y"pt1000" ; configure sensor 1 as PT1000 on pin 121.temp0
M950 H1 C"121.out0" T1 ; create nozzle heater output on 121.out0 and map it to sensor 1
M307 H1 B0 S1.00 ; disable bang-bang mode for heater and set PWM limit
M143 H1 S280 ; set temperature limit for heater 1 to 280C; Fans
M950 F0 C"121.out2" Q500 ; create fan 0 on pin 121.out2 and set its frequency
M106 P0 S1 H-1 ; set fan 0 value. Thermostatic control is turned off
M950 F1 C"121.out1" Q500 ; create fan 1 on pin 121.out1 and set its frequency
M106 P1 S1 H1 T45 ; set fan 1 value. Thermostatic control is turned on; Tools
M563 P0 D0 H1 F0 ; define tool 0
G10 P0 X0 Y0 Z0 ; set tool 0 axis offsets
G10 P0 R0 S0 ; set initial tool 0 active and standby temperatures to 0C;accelerometer settings
M955 P121.0 I14 ; set to toolboard address 121 and orientation of 14; Miscellaneous
T0 ; select first tool -
RE: 6HC power out
I guess I figured out you dont run the toolboard power off of that terminal block on the 6hc? ran power directly from power supply and it works
-
6HC power out
wiring up my printer, I have 24v coming into the "power in" AND into the "out 0 power in" and they both read 24v on my meter at those terminals but the "out 0" to the toolboard is only putting out 2.5v thus the toolboard wont power on properly whats going on, is there a jumper I need to change?
-
RE: configuring motor direction and endstops
@phaedrux said in configuring motor direction and endstops:
@57buick said in configuring motor direction and endstops:
M574 Y1 S1 P"io0.in" ; configure switch-type (e.g. microswitch) endstop for low end on Y via pin io0.in
If the endstop is at the rear and the maxima, the endstop must be configured as
M574 Y2 S1 P"io0.in"
0,0 will stay as the front left.
Also see the motor direction testing here: https://docs.duet3d.com/en/User_manual/Machine_configuration/Configuration_coreXY
ok got it, so now I hit Y home to test it and it triggered the switch and the LED turned on switch but motor did not stop. Also instructions say to go to the machine specific page to see the state of the switches but I cant find the switches anywhere in the duet web control that I can see?
I also tried adding the ! infront of pin to invert it but that doesnt work.
Does it have anything to do with my X switch not being hooked up yet?